목차
고체의 특성은 물질을 구성하는 입자(원자 및 분자)의 배열에 따라 크게 달라집니다. 배열이 무질서하면 물질은 비정질입니다. 결정성 물질에서는 입자가 일정한 간격으로 고정된 패턴으로 배열되어 있습니다.
가교 폴리머(듀로머, 열경화성 엘라스토머)는 항상 무정형 구조를 갖지만 열가소성 폴리머에서는 결정이 형성될 수 있습니다. 대부분의 경우 결정 구조의 영역과 비정질 구조의 영역이 나란히 나타납니다. 이 경우 반결정성 플라스틱이 존재합니다.
결정화 정도는 플라스틱이 고체가 되는 조건에 따라 달라집니다. 응고되는 동안의 온도와 온도 변화 속도가 결정적인 영향을 미칩니다.
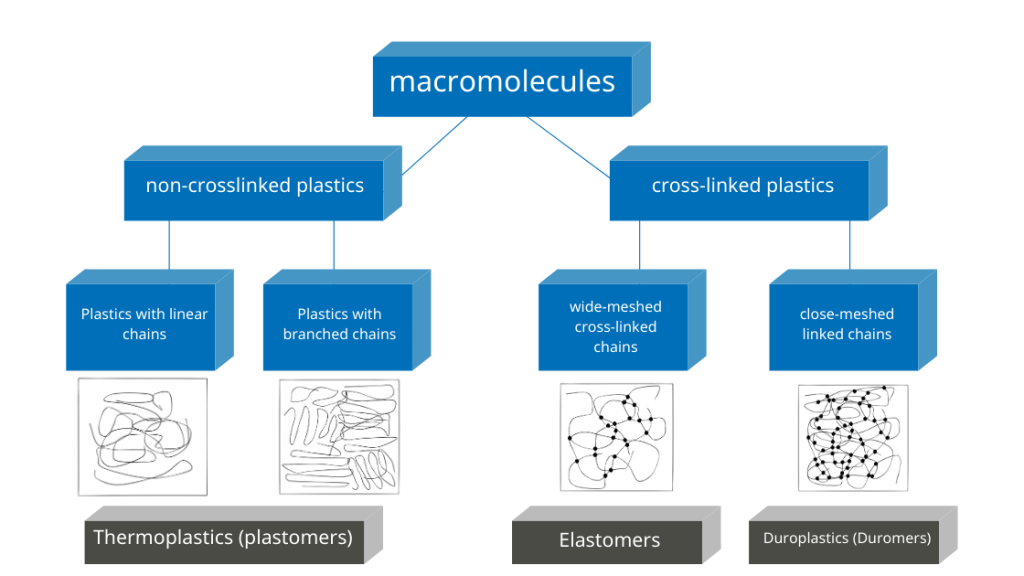
결정화에 따른 머티리얼 속성
플라스틱의 결정화는 밀도, 유리 온도, 용융 온도 및 견고성을 증가시킵니다.
그 결과 치수 안정성과 기계적 마모에 대한 저항성도 향상됩니다.
동시에 열팽창 계수와 액체 및 가스의 침투 용량이 감소합니다.
이러한 특성으로 인해 반결정성 폴리머의 적용 범위가 확장됩니다.
결정화 과정에서 열이 방출됩니다.
이 결정화 엔탈피는 다음 방법으로 결정할 수 있습니다. 차동 주사 열량 측정법(DSC) 로 측정하고 알려진 값과 비교할 수 있습니다.
측정된 결정화 엔탈피와 열 분석 중에 얻은 기타 데이터를 통해 폴리머의 생산 및 품질 관리를 최적화할 수 있습니다.
결정화
폴리머의 액체에서 고체 상태로의 전환은 두 가지 방법으로 이루어질 수 있습니다: 용융된 폴리머가 고체화되거나 과포화 용액에서 침전됩니다. 이 과정에서 고분자는 운동 에너지의 상당 부분을 잃게 되며, 이는 열로 환경으로 방출됩니다.
제한된 온도 범위 내에서 공 모양의 분자 사슬은 “늘어날” 수 있습니다. 이렇게 하면 소방 호스나 케이블이 겹겹이 쌓인 것처럼 접힌 거대 분자로 구성된 평행 구조로 배열됩니다. 일부 폴리머에서는 서로 다른 분자의 사슬이 서로 평행하게 정렬되기도 합니다. 이러한 구조의 형성을 결정화라고 합니다.
결정 구조의 형성에는 결정화 핵이라고 하는 시작점이 필요합니다. 이러한 핵은 이미 결정화된 폴리머 또는 석영과 같은 이물질 분자의 가장 작은 양일 수 있습니다. 결정은 다른 결정이나 비정질로 굳어진 물질 영역과 만날 때까지 이 핵을 중심으로 성장합니다. 용융물이나 용액에 결정화 핵을 추가하면 결정의 수와 크기에 영향을 미칠 수 있습니다.
어떤 물질이 핵으로 적합한지는 개별 폴리머 시스템에 따라 다르며 실험적으로 결정해야 합니다. 결정 성장에 필요한 시간과 최적의 온도 범위도 실험을 통해 결정됩니다. 열 분석 방법이 이에 적합합니다.
재결정화
재결정화는 결정이 새롭게 형성되고 변형되는 것을 말합니다. 이 과정은 결정성 또는 반결정성 물질의 온도가 특정 값에 도달하거나 폴리머가 외부 기계적 힘에 의해 변형될 때 무의식적으로 발생합니다. 또한 입자의 이동성의 증가 또는 감소와도 관련이 있습니다. 재결정화는 필요한 재료 특성을 얻기 위해 목표한 방식으로 사용할 수 있습니다. 이를 위해 다양한 공정을 사용할 수 있습니다.
스트레칭을 통한 사후 결정화
이 공정은 합성 섬유, 필름 및 중공체 생산에 사용됩니다. 합성 섬유와 필름은 가열된 폴리머를 압출하여 생산됩니다. 이 과정에서 재료는 노즐 또는 이와 유사한 구멍을 통해 고압으로 압착되어 모양을 갖추게 됩니다.
그런 다음 인장력을 가하면 분자 사슬이 늘어나면서 평행하게 배열됩니다. 내부의 과압에 의해 팽창된 블랭크에서 속이 빈 몸체(용기, 병)를 만들 수 있습니다. 이로 인해 재료에 발생하는 인장 응력은 결정화로 이어집니다.
솔루션에서 재결정화
용액에서 폴리머의 고분자는 고르게 분포되어 있습니다. 과포화가 유도되면, 즉 용액 내 고분자의 농도가 용액의 각 온도에서 최대 용해도 이상으로 증가하면 고분자는 고체 상태로 침착됩니다. 이 과정에서 고분자들은 스스로 재배열되어 결정 구조를 형성할 수 있습니다.
결정화를 위한 전제 조건은 결정 성장에 필요한 최적의 온도와 시간을 유지하는 것입니다. 응축 핵을 추가하여(용액에 ‘접종’) 재결정을 지원하고 제어할 수 있습니다.