Les plastiques sont présents dans tous les domaines de la vie : emballages, automobiles, textiles, outils, jouets, multimédia, etc.
L’avantage des matières plastiques est que leurs propriétés techniques, telles que l’élasticité, la dureté, la résistance à la température et aux produits chimiques, peuvent être modifiées de diverses manières en utilisant des matières premières, des procédés de fabrication et des additifs différents.
Les polymères les plus couramment utilisés polymères sont le polyéthylène (PE), le polypropylène (PP), le chlorure de polyvinyle (PVC), le polystyrène (PS), le polyuréthane (PUR) et le polyéthylène téréphtalate (PET).
Procédé d'impression 3D pour les polymères
Le moulage par injection, souvent également appelé moulage par injection ou processus de moulage par injection, est basé sur le moulage primaire. Dans ce processus, la machine de moulage par injection liquéfie le plastique, qui se présente sous forme de granulés, et l’injecte sous pression dans le moule correspondant. Dans ce moule, la matière se refroidit et revient à l’état solide. L’objet fini peut alors être démoulé et, si nécessaire, retravaillé. L’avantage de ce procédé est que les moules d’origine peuvent être réutilisés et que des volumes très importants peuvent être produits rapidement et à moindre coût.
Toutefois, la fabrication additive est de plus en plus utilisée pour produire des pièces en plastique. L’avantage est que les imprimantes 3D sont beaucoup plus petites que les machines de moulage par injection, qu’il n’est pas nécessaire de fabriquer et de remplacer des moules principaux et qu’aucun outil spécial n’est requis. La fabrication additive est particulièrement utile pour produire des pièces en petites quantités ou à géométrie plus complexe. Les procédés d’impression sont donc excellents pour la fabrication de prototypes et de modèles ou d’outils spéciaux.
Entre-temps, les imprimantes 3D ont atteint la maturité de production et peuvent également être utilisées de manière relativement peu coûteuse à des fins privées. Cela signifie donc que la fabrication additive de pièces en plastique est utilisée dans de très nombreux domaines, tels que l’industrie, la recherche, la construction, l’art, l’industrie et également à la maison.
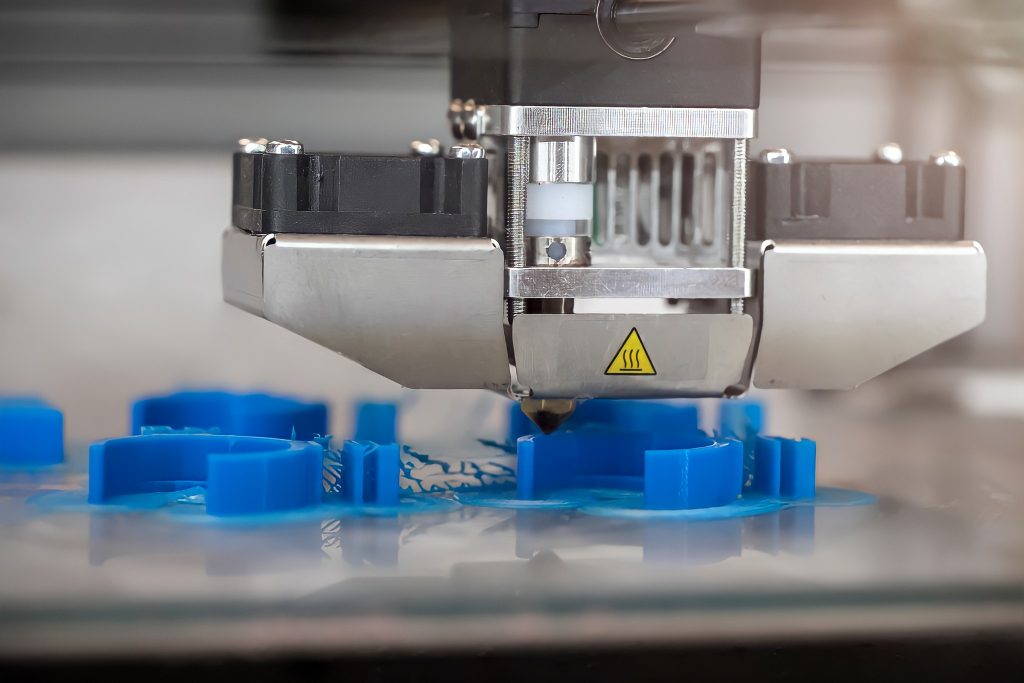
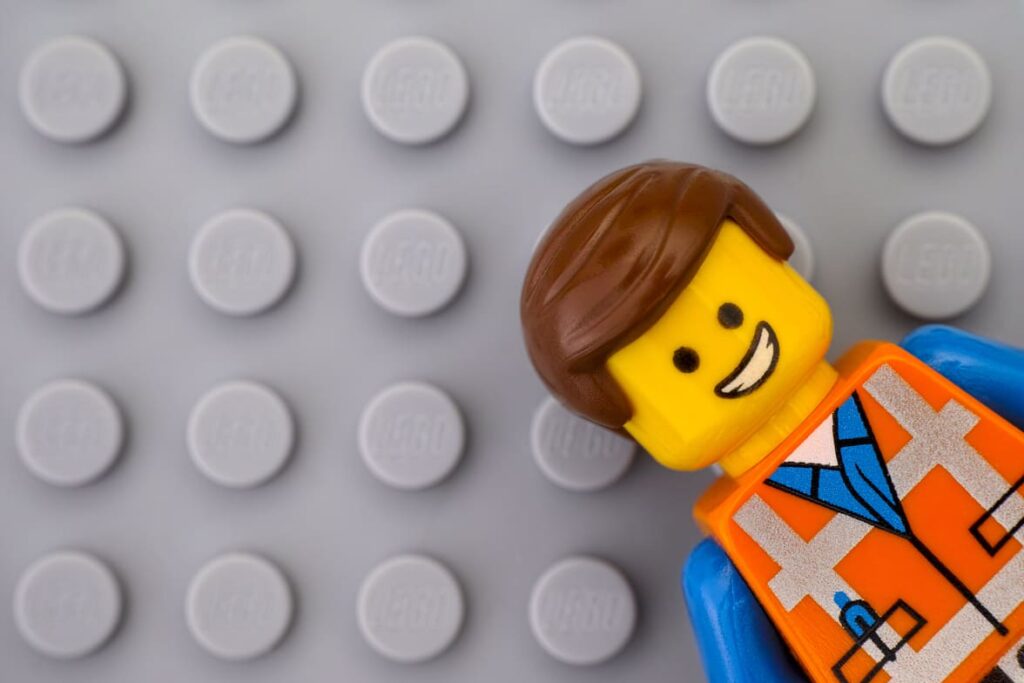
Modélisation par dépôt en fusion (FDM)/Fabrication par filament en fusion (FFF)
Parmi les procédés d’impression 3D de polymères les plus couramment utilisés figure l’extrusion de matériaux, comme la modélisation par dépôt fondu (FDM) ou la fabrication par filament fondu (FFF). Dans ce processus, un filament d’un matériau thermoplastique solide est fondu en le forçant à travers une filière d’extrusion chauffée. Le matériau est ensuite placé sur le lit d’impression selon la trajectoire spécifiée par le modèle, sur lequel le filament se refroidit pour former une couche. Ce processus est répété couche par couche jusqu’à ce que le composant soit entièrement fabriqué. Les filaments thermoplastiques sont généralement fabriqués en PLA, ABS, PET ou PETG.
Photopolymérisation
Un autre procédé courant est la photopolymérisation en bain (photopolymérisation en cuve), dans laquelle une source lumineuse polymérise sélectivement une résine photopolymère dans une cuve. Cette méthode comprend la stéréolithographie (SLA) et le traitement numérique de la lumière (DLP). La principale différence entre les deux est la source de lumière : la SLA utilise des points laser et la DLP un projecteur de lumière.
D’autres procédés peuvent être envisagés pour la fabrication additive de matières plastiques, comme la fusion sur lit de poudre, qui comprend le frittage sélectif par laser (SLS).
Dans ce processus, une source d’énergie thermique (laser) fait fondre les particules de poudre dans la zone de construction, puis une nouvelle couche de poudre est appliquée et le processus est répété. L’avantage de ce procédé est que la poudre non utilisée autour du composant soutient la structure et peut ensuite être réutilisée. On utilise ici de la poudre thermoplastique, comme le nylon.
Les photopolymères ou les cires sont souvent utilisés pour la projection de matériaux à jet libre. L’imprimante dépose sélectivement des gouttelettes de matériau sur le lit d’impression ou sur la couche précédente, qui sont ensuite durcies. Ce procédé permet d’utiliser simultanément différents matériaux pour un même objet. Ceci est particulièrement avantageux pour les composants complexes qui nécessitent une structure de support.
En fonction des exigences des composants à imprimer, différents polymères peuvent être envisagés, qui se distinguent par leurs propriétés optiques, mécaniques et thermiques ainsi que par le degré de difficulté de l’impression.
Les matériaux les plus couramment utilisés pour l’impression 3D sont le PLA (acide polylactique), un plastique biodégradable fabriqué à partir de dérivés d’amidon de maïs et facile à imprimer, et l’ABS (acrylonitrile butadiène styrène) à base de pétrole.
Ce dernier est très robuste et durable et est utilisé, par exemple, pour les intérieurs de véhicules ou les jouets.
En outre, le PET, le PETG (PET combiné au glycol), le nylon, le polypropylène (PP) ou même le PMMA (également connu sous le nom de verre acrylique, plexiglas) sont également utilisés.
Ces matériaux peuvent être modifiés dans leur apparence et leurs propriétés avec des additifs tels que des métaux, des céramiques, du carbone ou du bois, de sorte que, par exemple, des filaments conducteurs d’électricité ou magnétiques peuvent être développés pour l’impression 3D pour des applications spéciales.
Un autre groupe de polymères utilisés est celui des photopolymères, ou résines, qui sont durcis couche par couche par la lumière UV.
Les problèmes d’impression comprennent le colmatage des goulots d’extrusion, les fissures, le gauchissement ou la déformation de la pièce et les problèmes d’adhérence entre les couches.
Pour éviter ces problèmes, il est important de connaître les propriétés du matériau à utiliser.
En particulier, la température de transition vitreuse et la température de fusion sont importantes.
La température du lit d’impression doit être inférieure à la température de transition vitreuse afin de ne pas perturber le processus d’impression.
La température d’extrusion doit être bien supérieure au point de fusion afin que le polymère soit liquide et qu’une impression correcte puisse être assurée.
L’étude des propriétés thermiques est une étape inévitable pour ajuster les paramètres de l’impression 3D afin d’éviter les erreurs et les problèmes.
Par exemple, le point vitreux et les points de fusion et de cristallisation peuvent être déterminés à l’aide du calorimètre différentiel à balayage (DSC).
L’analyse à l’aide d’un dilatomètre (DIL) est également utile, car tant le point vitreux que le coefficient de dilatation thermique (CTE) peuvent être déterminés et la déformation pendant le chauffage et le refroidissement peut être étudiée.
En outre, il est important d’enregistrer les propriétés thermiques et mécaniques du composant fini, car elles peuvent être très différentes de celles du matériau brut.
En particulier, la conductivité thermique d’un corps imprimé en 3D peut être très différente de celle d’une pièce fabriquée de manière conventionnelle en raison de la structure en couches, qui introduit des résistances thermiques de contact supplémentaires, et de l’introduction de cavités.
La méthode du flash laser (LFA)La méthode du pont chaud transitoire (THB) et le testeur testeur de matériaux d’interface thermique (TIM) sont adaptés à cette analyse.