Table des matières
Les matériaux qui sont travaillés à l’état liquide ont généralement besoin d’un certain temps pour durcir.
Au cours de cette période, des processus chimiques et physiques se produisent, conduisant au durcissement du matériau.
Ces processus sont associés au dégagement ou à l’absorption de chaleur.
En enregistrant les quantités de chaleur correspondantes à l’aide de la calorimétrie à balayage différentiel (DSC) il est possible d’observer le déroulement des processus en fonction de conditions expérimentales définies. Les résultats donnent des informations sur les conditions optimales de durcissement et permettent de tirer des conclusions sur les paramètres de qualité du matériau étudié.
Durcissement des duroplastes et des élastomères
Les duromères, ou également les duroplastiques et les élastomères, sont des polymères qui obtiennent leur résistance finale par réticulation des macromolécules.
Des liaisons chimiques sont formées au niveau des groupes fonctionnels.
On ammorce ses réactions par une augmentation de la température ou l’ajout de produits (durcisseurs) qui forment un pontage entre les groupes réactifs.
Les duromères forment un réseau spatial à mailles serrées.
Ils atteignent ainsi un haut degré de résistance.
Le réseau des élastomères est à mailles larges.
Ses macromolécules en forme de billes peuvent être écartées et revenir à leur état initial lorsque la force de traction est supprimée. Après réticulation complète, les polymères sont stables sur le plan dimensionnel.
Ce processus s’appelle le durcissement.
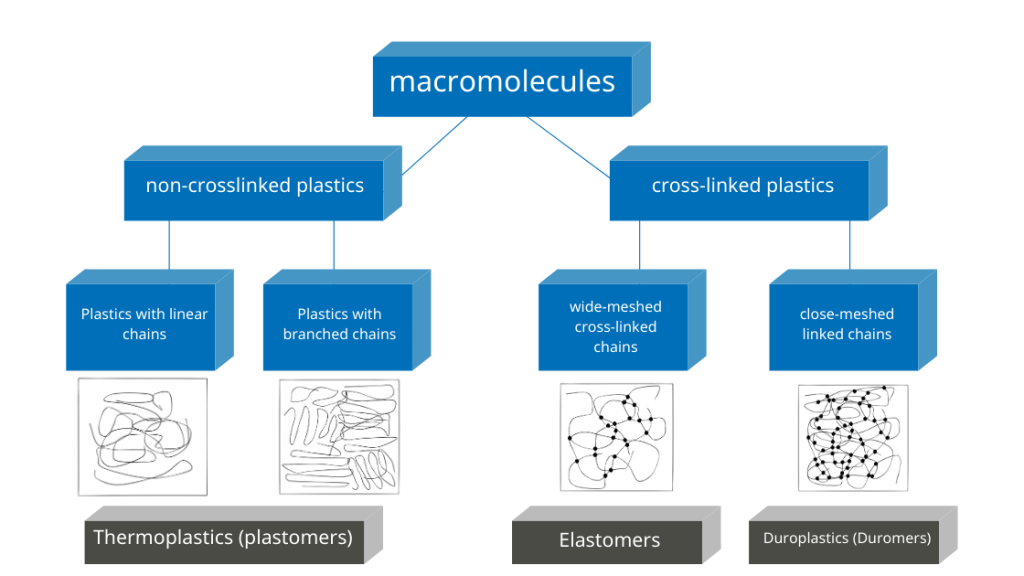
Exemples de thermoplastiques amorphes :
Polystyrène (PS) dans les jouets, les bobines et les films, PVC dans les conteneurs, les tuyaux, les films, l’isolation acoustique et thermique, les nappes.
Exemples de thermoplastiques semi-cristallins :
Polyéthylène (PE) dans les récipients, les bouteilles, les tuyaux, les couches de protection contre la corrosion, Polypropylène (PP) dans les films isolants, les tuyaux ou les rubans adhésifs.
Exemples de thermodurcissables :
PF (résine phénolique) et UP (résine polyester) en poignées résistantes à la chaleur et électriquement isolants.
Exemples d'élastomères :
Polyuréthane (PU) dans les pièces élastiques de machines, les surfaces des terrains de sport, les chaussures de ski.
Au cours de la polymérisation, une matière plastique passe par différentes phases.
Le matériau de départ se présente généralement sous la forme d’une solution liquide.
Cela signifie que les macromolécules sont finement réparties dans un solvant.
À une température minimale qui dépend du système de polymères, les réactions de réticulation commencent dans la solution, ce qui donne lieu à un gel.
Le gel est constitué des composants réticulés, désormais insolubles avec des mailles contenants les molécules du solvant.
Le mélange de sol et de gel est initialement élastique.
Dans les systèmes thermodurcissables, il atteint un état vitreux pendant la progression de la réticulation.
La polymérisation se poursuit jusqu’au degré maximal de polymérisation, moment où le sol est complètement transformé en gel.
Dans les systèmes élastomères, le gel conserve son état élastique après la réticulation complète.
Le comportement résultant est finalement déterminé de manière décisive par la température de transition vitreuse du système polymère.
Pour les duromères, cette température est supérieure à la température de polymérisation, pour les élastomères, elle est inférieure.
Au-dessus de la température de transition vitreuse, le polymère est mou et les molécules sont mobiles, en dessous, le matériau est plutôt solide et cassant.
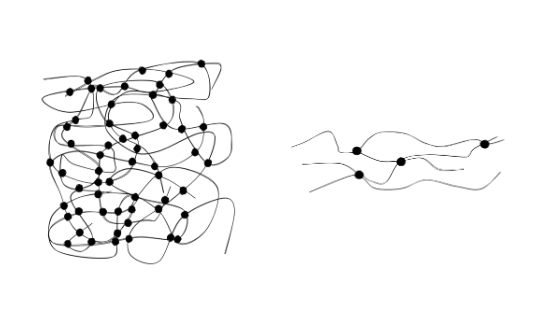
Le niveau de durcissement
La durée du durcissement dépend de la composition du système polymère et de la température.
En dessous d’une limite de température dépendant du système, aucune réticulation significative n’a lieu.
Bien que le sol devienne solide après un certain temps, il peut être liquéfié à nouveau en le chauffant.
Au-delà de cette limite de température, les réactions de réticulation commencent après un certain « temps d’attente ».
Le « temps d’attente » est raccourci et la vitesse de réaction augmente au fur et à mesure que la température augmente.
La réaction de réticulation est irréversible.
La durée pendant qu’on peut travailler le mélange initial dépend du temps d’attente. Cette période est appelée durée de vie en pot.
Elle peut être prolongée par l’ajout d’inhibiteurs et raccourcie par l’ajout de catalyseurs.
La vitesse de réaction détermine le temps dont le système polymère a besoin pour durcir complètement.
L’ajout d’inhibiteurs ou de catalyseurs peut également avoir une influence sur cette période de temps.
Cependant, la température de réticulation a une influence significative.
L’avancement de la réticulation est exprimé par le degré de réticulation.
Il s’agit du pourcentage du mélange qui a déjà été réticulé.
Le degré de durcissement maximal est atteint lorsque la totalité du sol s’est transformée en gel.
L'enthalpie de réaction
La réaction de réticulation est exothermique, c’est-à-dire qu’elle se produit sous l’effet d’un dégagement de chaleur.
Étant donné que les processus se déroulent à pression constante, seule la quantité de chaleur qui n’est pas consommée par les changements de volume peut être déterminée.
Cette partie est l’enthalpie de réaction.
Elle peut être déterminée par analyse thermique pour la réaction complètée.
La calorimétrie différentielle à balayage (DSC) permet de déterminer la quantité de chaleur libérée par unité de temps.
Cette valeur correspond à la vitesse de réaction.
La quantité de chaleur libérée jusqu’à un certain moment peut être mise en relation avec l’enthalpie de la réaction. Ce rapport est égal au degré de durcissement.
Les valeurs obtenues permettent de déterminer la température optimale de durcissement et le degré de durcissement des échantillons, de déterminer le rapport de mélange approprié entre le sol et le durcisseur et d’évaluer l’efficacité des inhibiteurs et des catalyseurs.