Table of Contents
Thermal Interface Materials (TIM’s) are used in electronics to ensure efficient heat dissipation and to prevent local temperature overloads. This ensures reliable and stable operation of electrical equipment and components.
What are Thermal Interface Materials?
With a thermal conductivity of only 0.0263 W/MK, air is the worst heat conductor ever. Air inclusions between components should therefore be avoided in order to prevent heat accumulation. Here TIM’s help to close gaps caused by unevenness, tolerances or roughness and ensure that no air gaps occur.
- Heat conducting pastes,
- Heat conductive adhesive,
- Graphite and aluminium foils,
- Foam and GEL films,
- One-sided and double-sided adhesive heat conducting foils,
- Phase Change Materials (PCM’s),
- Silicone-containing and silicone-free elastomers,
- Kapton and mica discs,
- Aluminium oxide materials
In many cases it is not easy to find the right intermediate material. However, a sufficiently well designed thermal management system is indispensable for optimum function and a long service life of electronic components.
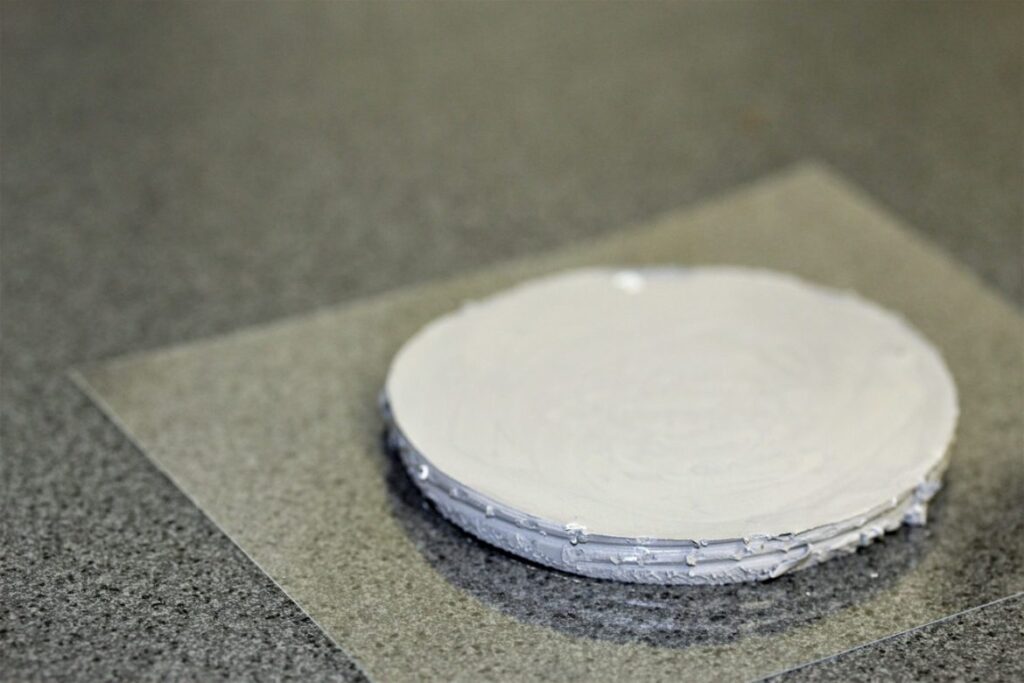
Gap Filler
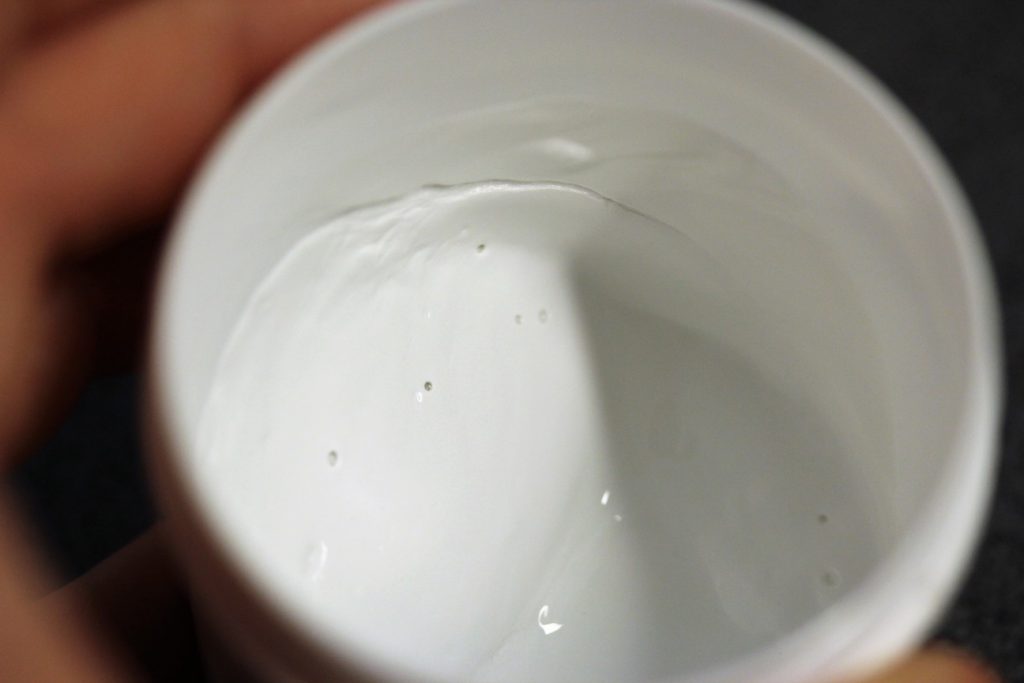
Paste
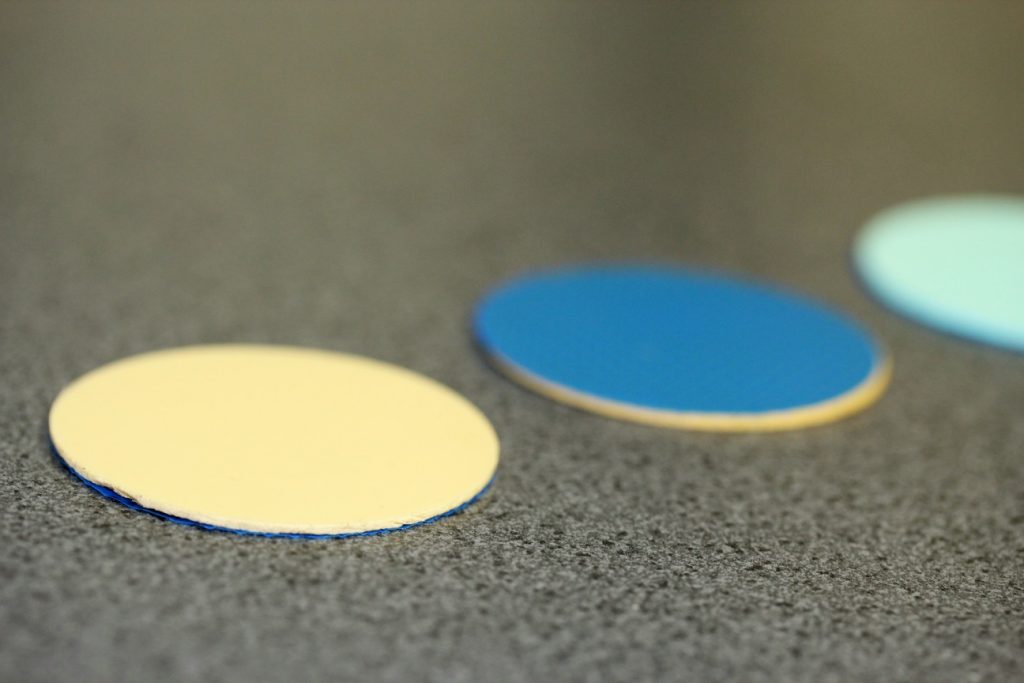
Pads
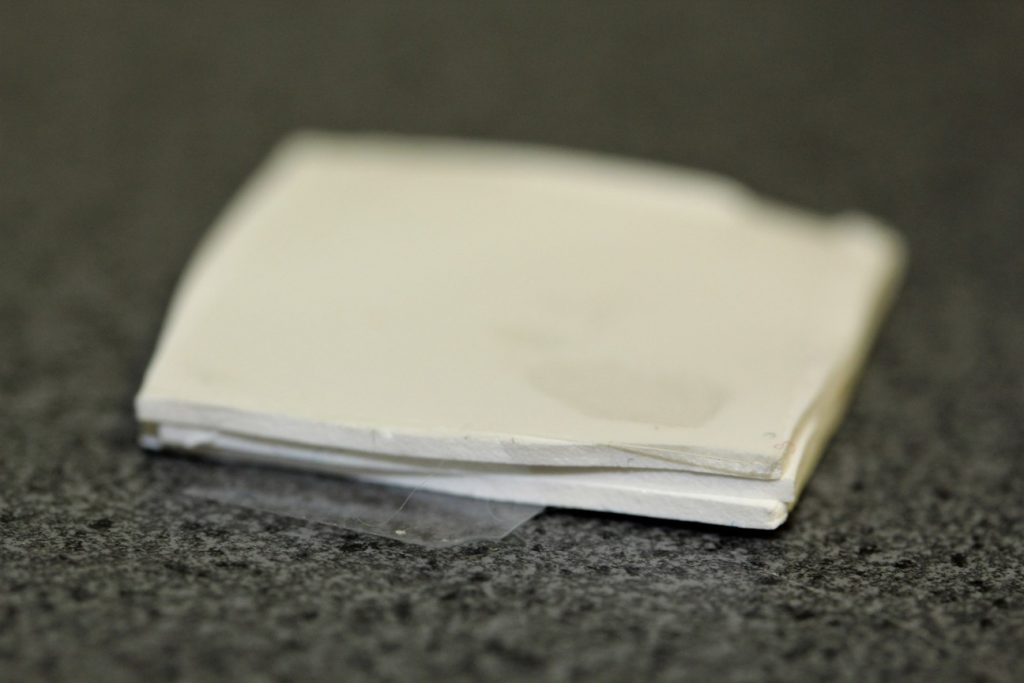
Which TIM’s are best suited for which application?
Not every material is suitable as a universal material for all applications in electronics. In order to find the perfect TIM, developers in the field of materials research must consider a wide variety of material properties such as thermal resistance, thermal conductivity, thermal impedance, mechanical tolerances of the contact pairing, temperature range, environmental compatibility and many others.
Which material is most suitable depends on the application. The three main types of TIM’s are thermal conductive films, thermal conductive pastes and thermal conductive adhesives. These differ, among other things, in their use, layer thickness, electrical insulation and thermal conductivity.
Heat conducting phases
Heat conducting pastes are often used to generate heat transfer layers, for example between a heat sink and an electronic component. These are usually applied in very small layer thicknesses of maximum approx. 50 µm. Larger component distances cannot thus be bridged. In practice, excessive amounts of paste are often used. However, too sparing application is often more critical as it may not compensate for all air inclusions.
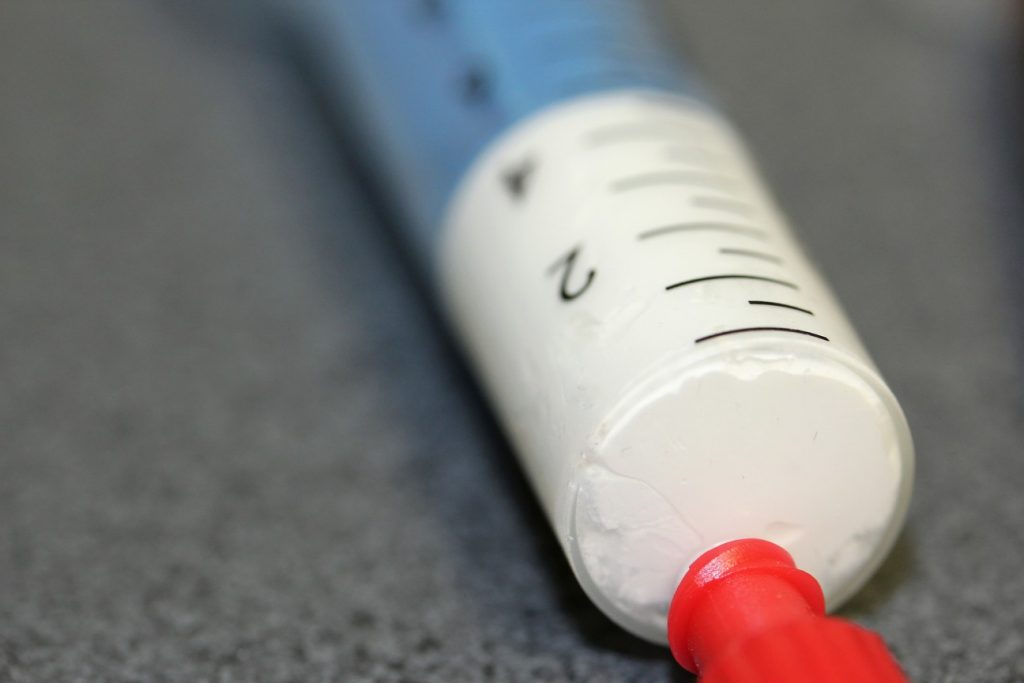
Phase Change Materials
Phase change materials are a further development of conventional thermal pastes. As plate material these TIM’s have a continuous layer thickness, which allows a clean direct mounting on the heat sink. In addition, PCMs are characterized by their phase change temperature. At a temperature of 45 to 55 °C, the consistency of these materials changes from solid to soft. As a result, they flow into all spaces between the components to which they are applied. If the temperature falls below the phase change temperature again, the respective medium returns to its initial state without the connection to the contact points breaking off.
Surface finish and selection of a TIM
In order to be able to use thermal pastes or adhesives, the surfaces should be almost ideal in terms of tolerance. If this cannot be guaranteed or if the handling of these materials is too complicated, films are usually used. This allows air gaps of up to 5 millimeters to be compensated. However, the thermal resistance of these TIM’s is higher due to their greater strength.
Fields of application of thermal interface materials
The multitude of thermal interface materials produced in a wide variety of processes illustrates a change in best design practice. Increasingly, air cooling in electronics is disappearing in favor of more and more heat sinks and a connection of hot components to metal housings and other heat dissipating surfaces.
This change also benefits the often desired miniaturization of components. A higher component density reduces the air volume available for cooling and at the same time prevents the remaining air from circulating. Therefore, in systems where cooling ventilators were originally used for forced air cooling, a fanless design is usually preferred today.
TIM’s in everyday life
TIM’s are now used in a wide variety of applications, for example in automotive electronics, in the computer, memory and gaming sector, in optoelectronics and in the aerospace industry. In addition, they enable excellent heat management in electronics packaging, household appliances, lighting technology, medical technology and industrial automation.
High-precision measurements are the basis for optimized heat management
optimized heat management
Due to the countless possible fields of application and the immense variety of materials, Thermal Interface Materials pose great challenges for materials research. Thermal management in the field of electronics is extremely complex and requires precise knowledge of the material properties of the applied TIMs.
These specifics can be determined with the Thermal Interface Material Tester, which measures the thermal impedance of thermal interface materials such as thermal fluids, thermal pastes, elastic thermal conductors and phase change materials and determines their probable thermal conductivity.
With this knowledge it is possible to perfect the cooperation of components and interface materials and to develop an optimal thermal management for complex electronic applications.
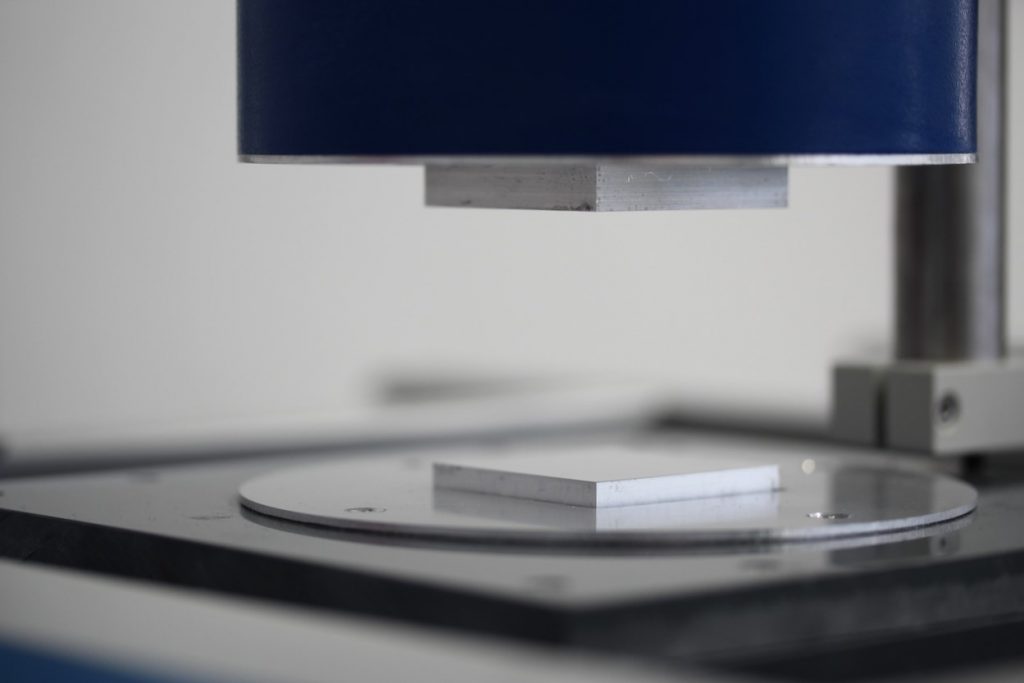