Table of Contents
Metallurgy is a science as old as civilization itself. Yet despite its ancient roots, it remains a field at the forefront of innovation, especially when it comes to phase transformations. These fascinating processes are at the heart of materials science and are crucial for the development of new metals and alloys with tailored properties.
What are Phase Transformations?
Phase transformations are changes in the state of matter that occur under certain thermodynamic conditions. In metallurgy, we speak of the transformation from one crystalline state to another, fundamentally altering the physical properties of the metal.
Thermodynamics and Kinetics: The Driving Forces
Thermodynamics gives us insight into the energy relationships that drive a phase transformation. The Gibbs phase rule is a central concept that describes how many phases can coexist under given conditions. Kinetics, on the other hand, deals with the rate at which these transformations occur and the mechanisms behind them.
The Diversity of Phase Transformations
Phase transformations in metals are as diverse as the elements of the periodic table that go into alloys. These transformations are not only fascinating for science but also of crucial importance for practice. Here are some of the most remarkable transformations that play a role in metallurgy:
Eutectic Transformations:
- These occur when a liquid solution cools and transforms into two or more solid phases simultaneously. The classic example is the eutectic system of iron-carbon, which leads to a fine mixture of ferrite and cementite – a structure known as pearlite and the basis for many steel properties.
Peritectic Transformations:
- Here, a solid phase reacts with a melt to form a new solid phase. This type of transformation is crucial for the production of certain types of alloys where control of the microstructure is of utmost importance for the final properties of the material.
Martensitic Transformations:
- One of the most fascinating transformations is the martensitic one, which occurs without diffusion. It is a diffusionless transformation triggered by rapid cooling (quenching) of austenite, leading to a hard and brittle, distorted crystal structure. This transformation is fundamental for the production of hardened steel.
Bainitic Transformation:
- Bainite is a fine-needle-like microstructure that forms at temperatures between those for pearlite and martensite. It combines high strength with some toughness and is particularly found in high-strength steels.
Precipitation Hardening:
- This transformation occurs when very fine particles of a new phase precipitate from a supersaturated solid solution. These particles impede the movement of dislocations, thereby increasing the strength and hardness of the material.
Recrystallization:
- After severe deformation, new, stress-free grains can form in a metal, leading to a softer and more ductile structure. This process is crucial for the production of metals with specific mechanical properties.
Order-Disorder Transformations:
- In some alloys, atoms can be randomly distributed at high temperatures, but assume an ordered structure at lower temperatures. This transformation can affect the electrical and magnetic properties of the material.
Each of these transformations has its own characteristic temperature ranges and kinetics and is influenced by the composition of the alloy, heat treatment, and processing conditions. The art of metallurgy lies in mastering these variables to develop materials with tailored properties for specific applications.
Measurement and Analysis: A Look Inside Metals
Modern metallurgy relies on advanced measurement and analysis methods to uncover the secrets hidden in the depths of metal structures. These techniques allow us to observe and understand the subtle changes that occur during phase transformations.
Metallography:
- Metallography is a classic technique where metal samples are carefully prepared and examined under a microscope. By etching the surface with specific chemicals, different phases and grains are made visible, allowing conclusions about the microstructure and thus the mechanical properties of the material.
X-ray Diffraction (XRD):
- XRD is a powerful technique that reveals the crystalline structure of metals. It is based on the diffraction of X-rays by the atomic planes in the material and provides detailed information about phase composition and orientation, as well as lattice deformations.
Differential Scanning Calorimetry (DSC):
- DSC measures the heat absorbed or released when a sample is heated or cooled. This method is particularly useful for identifying exothermic and endothermic reactions during phase transformations.
Quenching Dilatometer:
- A quenching dilatometer is a specialized instrument that measures the length change of a sample during rapid cooling. It is crucial for investigating martensitic transformation and other phase transitions that occur under non-isothermal conditions. With its help, metallurgists can determine the critical cooling rates required to produce specific microstructures.
Deformation Dilatometer:
- The deformation dilatometer extends the analytical capabilities by measuring the length change under simulated deformation conditions. It can record the effects of strain and temperature on the microstructure in real-time, which is essential for the development of deformation processes and the optimization of material behavior under load conditions.
TTT and CCT Diagrams: The Maps of Metal Transformations
TTT Diagrams: Navigational Aids in Time-Temperature Space
Time-Temperature-Transformation (TTT) diagrams are like a treasure map for metallurgists, pointing the way to the valuable properties of metals.
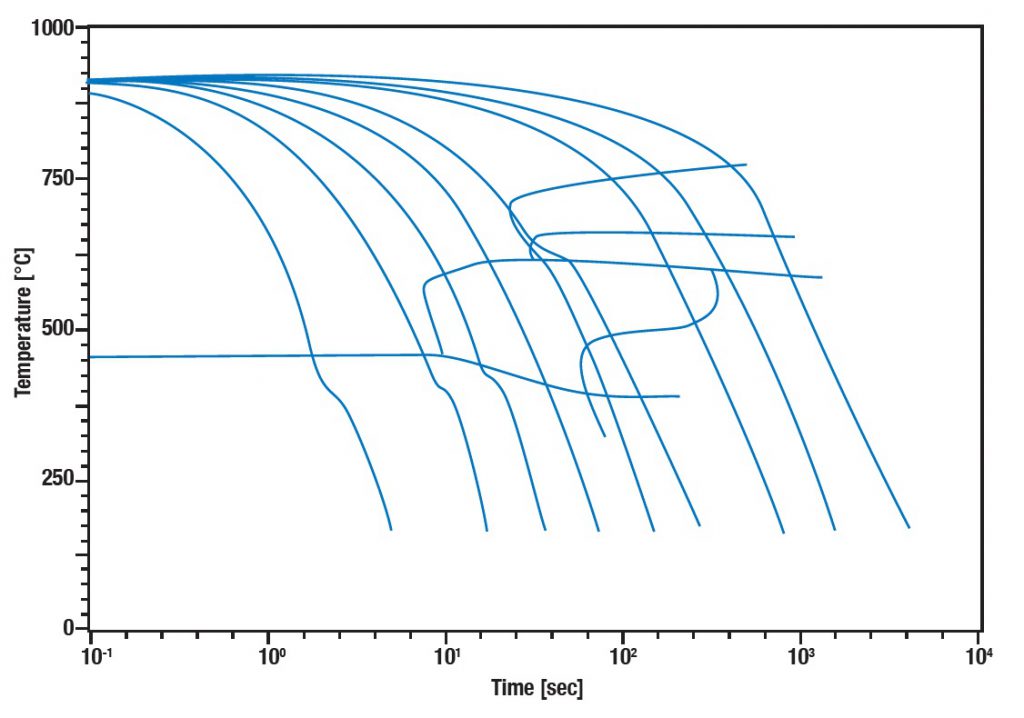
They illustrate how long it takes for a specific phase transformation to begin and complete at a constant temperature. These “transformation isotherms” are crucial for understanding how quickly one must cool a metal to avoid unwanted phases or achieve desired microstructures.
A TTT diagram is typically divided into three main areas:
- Upper left corner:
- Here you find the transformation to pearlite, which occurs at relatively slow cooling rates.
- The “nose” of the diagram:
- This is the most critical area where the transformation to bainite occurs most rapidly.
- Lower right area:
- Here the martensitic transformation is represented, which occurs at very fast cooling rates.
The exact shape and position of the “nose” depend on the chemical composition of the steel and other factors such as grain size. Interpreting a TTT diagram allows for precise control of heat treatment processes to achieve desired properties such as hardness, toughness, and strength.
CCT Diagrams: Continuous Cooling for the Real World
While TTT diagrams apply to isothermal conditions, Continuous Cooling Transformation (CCT) diagrams better represent the reality of industrial heat treatment. They show what happens when an alloy is continuously cooled, which is the case in most practical applications.
CCT diagrams are particularly useful for understanding the effect of cooling rates on microstructure and the resulting mechanical properties. They can look very different from the corresponding TTT diagrams for the same steel composition, as the time for diffusion processes during continuous cooling is limited.
The Practical Significance
Knowledge and application of TTT and CCT diagrams are essential for the development of heat treatment processes. They enable the optimization of processes such as hardening, tempering, and normalizing.
With their help, metallurgists can adjust the heat treatment to avoid the formation of unwanted phases like coarse pearlite or too much martensite and instead produce a fine distribution of bainite or a desired amount of martensite to achieve the perfect balance between strength and toughness.
Quenching and forming dilatometers play a key role in creating CCT diagrams, as they can simulate cooling curves under real conditions. They are indispensable tools for the research and development of new steel alloys and heat treatment processes.
Overall, TTT and CCT diagrams are indispensable tools in a metallurgist’s toolbox. They provide a scientific basis for understanding and controlling phase transformations and are thus crucial for the production of metals with tailored properties for demanding applications.
Phase transformations are not just an academic interest. They are crucial for the production of everything from automotive parts to surgical instruments. The ability to control these transformations is key to the quality and performance of the final product.
The constant search for better, more cost-effective, and environmentally friendly materials drives research in metallurgy forward. Innovative technologies such as additive manufacturing open up new ways to utilize and control phase transformations.
Phase transformations are a central theme in metallurgy, bridging the gap between the atomic world and the macroscopic world of engineering materials. Through a deep understanding of these processes, metallurgists can push the boundaries of what is possible with metals, thus laying the groundwork for the next generation of materials and technologies.