Table of Contents
A dilatometer is a measuring device for recording the Thermal expansion of a material sample. The coefficients of thermal expansion (CTE = coefficient of thermal expansion) are calculated from the measurement results. This quantity of material indicates in the unit of measure [1 / K] the relative change of the length of the sample with a temperature change per Kelvin.
The values of the CTE are thus temperature-dependent and are for solid substances in the range of a few millionths per Kelvin. The expected absolute length changes of the samples are correspondingly low. For reliable results, therefore, a very accurate measuring device is required.
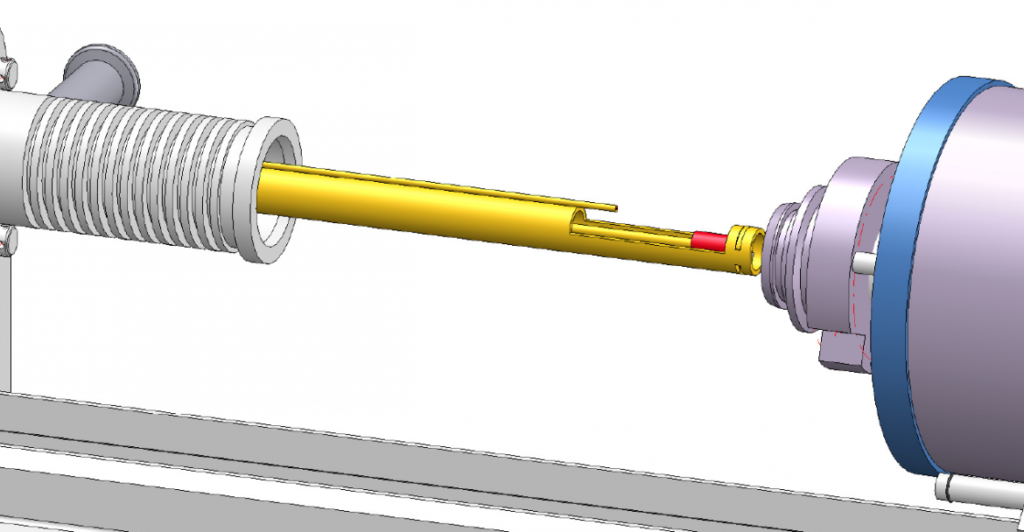
Types of dilatometer
The nature of the sample and the temperature range to be investigated determine the requirements that a sample holder must meet. For solid substances that maintain their state of aggregation in the intended temperature range, a pushrod dilatometer is very well suited.
The behavior of fabrics that are heated to the softening point or melting point can be determined optically using a heating microscope. Another experimental setup is based on the use of strain gauges, which are glued over the entire surface of the sample and evaluated via a resistance measuring bridge.
Function of the push rod dilatometer
The push rod dilatometer consists of an oven (right in the picture), the sample holder (in the center of the picture) and the unit for measuring data acquisition and evaluation (LVDT sensor on the left in the picture).
In a tube of quartz glass or ceramic, the sample is (red sample in the picture). It is firmly connected to a rod (thin yellow stamp, in front of the red sample), which transmits the change in length of the sample to the data acquisition.
There, the absolute change in length of the entire system is determined and converted to the CTE values of the material sample using the known data of the measuring system and the sample dimensions. Any temperature curves with different heating and cooling speeds as well as holding points can be realized via the oven.
As a result, the change in length of the sample is determined as a function of the temperature.
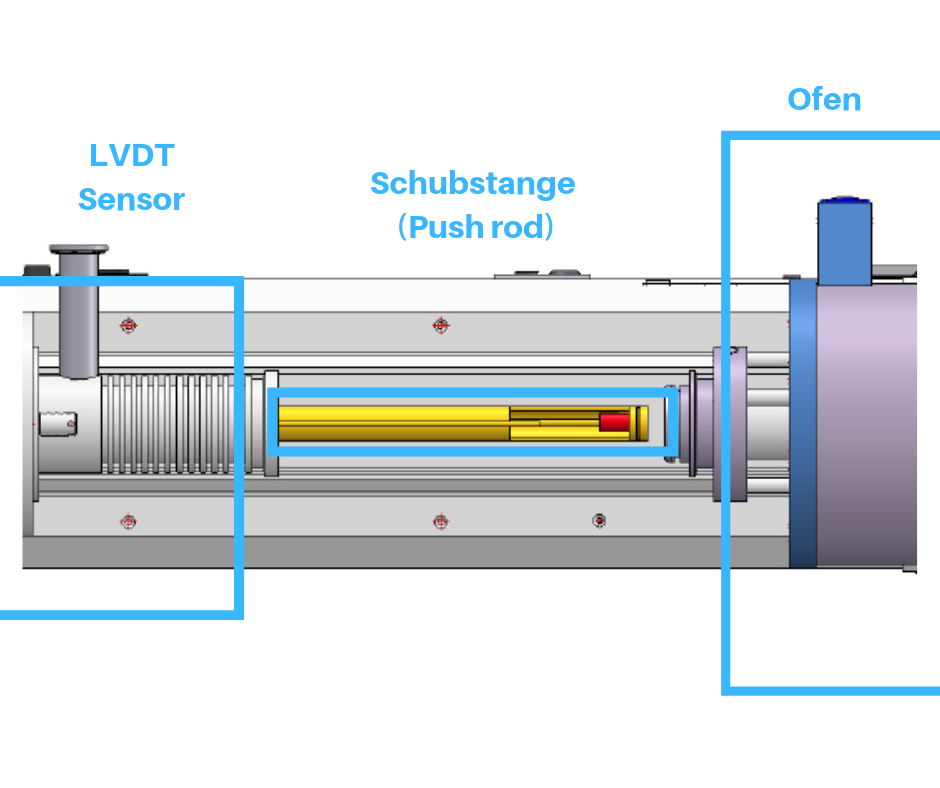
Applications for push rod dilatometer
The most important fields of application of the dilatometer are basic research in materials science and quality assurance. Above all, the thermal expansion coefficient, temperatures of phase transitions and sintering temperatures are recorded.
Thermal expansion coefficient
The thermal expansion coefficient is an important parameter for the development of composites. For example, reinforced concrete can only be used in construction because steel and concrete have the same CTE value.
Temperature differences in materials lead to mechanical stresses. High temperature areas expand more than cooler areas. The avoidance or reduction of these stresses can be achieved through the development and use of materials with a very low coefficient of expansion.
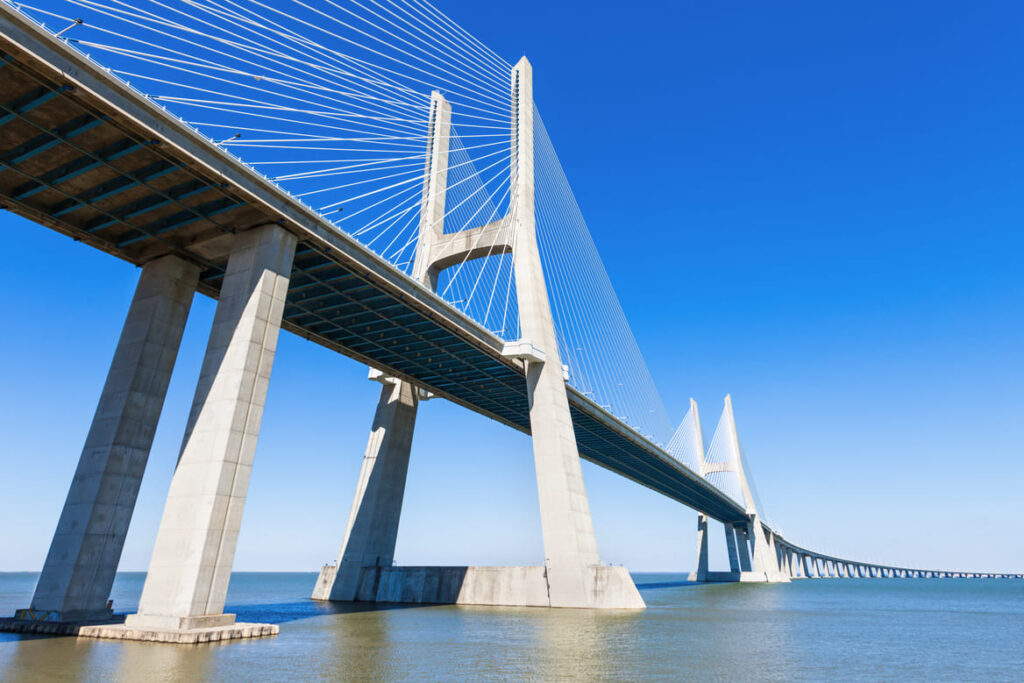
Phase transitions
The macroscopic properties of crystalline solids depend directly on the crystal structure itself.
However, most materials can be present in several modifications and therefore have, in addition to melting and evaporation temperature, also pressure- and temperature-dependent phase transitions in which the state of aggregation does not change.
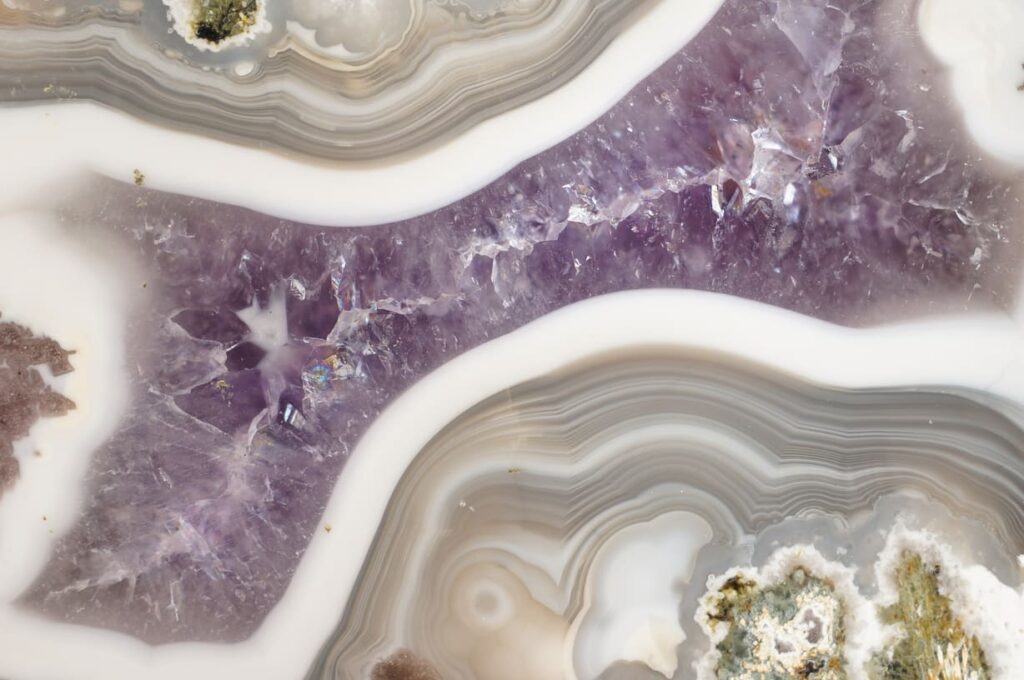
However, the phase transition from one crystal structure to another, as well as the crystallization process itself, is often clearly visible in the change in the coefficient of expansion-temperature curve, and thus can be imaged very well by dilatometer measurement.
Even rapid phase transitions or those that require a defined contact pressure, such as the conversion of martensite, ferrite or austenite in steels, can be well mapped with the correspondingly modified dilatometer.
Sintering temperatures
During sintering, powdered ceramic or metallic materials are preformed into a green body and then baked together at precisely set temperatures and pressures. In practice, this process is known, for example, in the porcelain industry. The powdery mixture of kaolin (porcelain clay, porcelain clay), feldspar and quartz is sintered in the firing process and thus made waterproof.
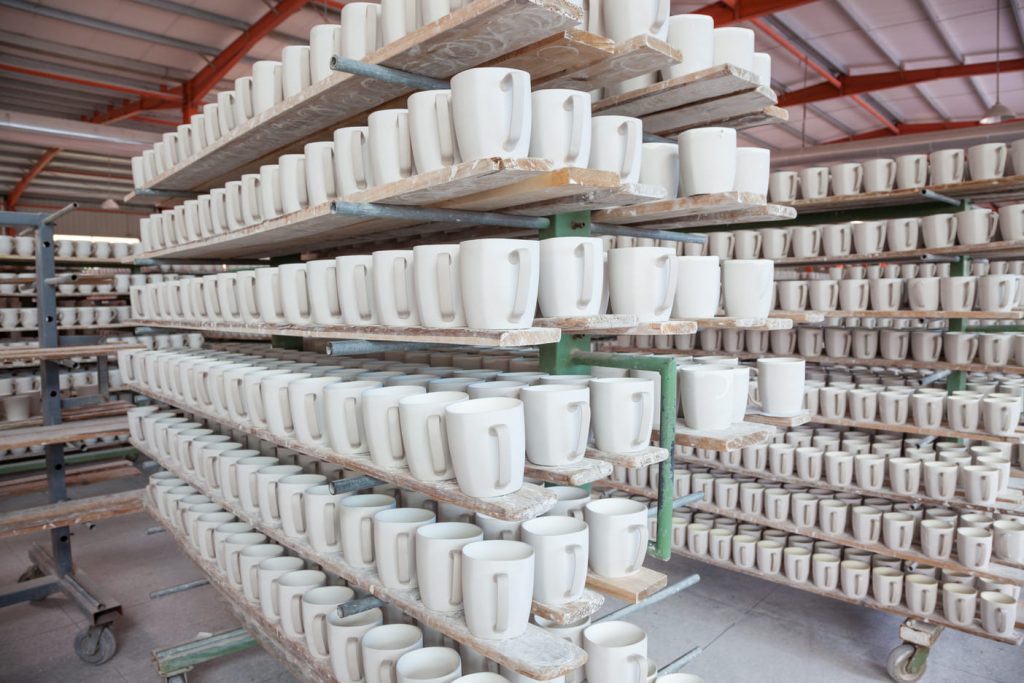