Table of Contents
High-density polyethylene (HDPE) vs. polyethylene (PE)
High-Density Polyethylene (HDPE) and Polyethylene (PE) are both types of Polyethylene, but they exhibit different properties due to variations in their manufacturing processes.
HDPE is a specific type within the Polyethylene family, distinguished by its high crystallinity, which results from a low proportion of side branching groups on the main polymer chains and the absence of any long side branches.
As a result, HDPE molecules can arrange themselves in an ordered, pseudo-crystalline structure, imparting unique mechanical properties to the material. On the other hand, Polyethylene is produced as a class of materials with various densities, and the degree and form of side branching on the polymer chain significantly influence its properties.
The differences in manufacturing lead to different densities and various commercial and scientific designations for Polyethylene, including HDPE.
The distinctions between HDPE and Polyethylene in terms of their physical properties are summarized in the table below:
PROPERTIES | HDPE VALUE (METRIC) | PE VALUE (METRIC) |
---|---|---|
Density: | 0.933–1.27 g/cm³ | 0.915–0.96 g/cm³ |
Shore D Hardness: | 55–69 | 42–56 |
Tensile Strength, Ultimate: | 15.2–45 MPa | 8.96–54 MPa |
Tensile Strength, Yield: | 2.69–200 MPa | 7.6–14 MPa |
These differences in density, hardness, and tensile strength illustrate the unique mechanical properties of HDPE compared to other polyethylene types.
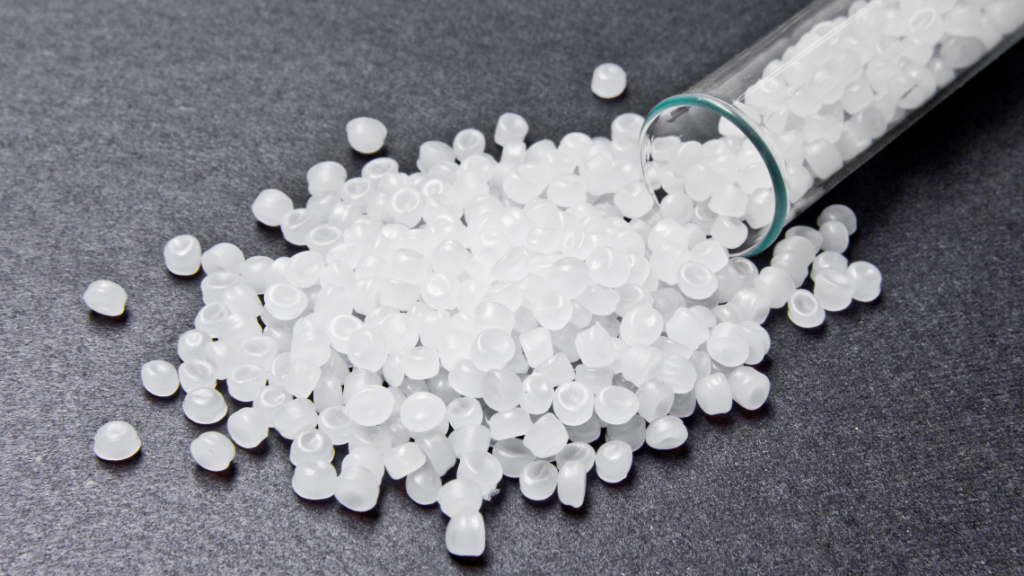
The crystallinity of HDPE
HDPE is a specific grade within the Polyethylene family and is characterized by its high crystallinity. This means that HDPE molecules are arranged in an ordered, crystalline structure, imparting unique mechanical properties to the material. To precisely quantify the crystallinity, one can use the special and patented Chip-DSC.
The high crystallinity of HDPE results in impressive chemical resistance and high tensile strength. These attributes stem from its specific molecular arrangement, providing the material not only with strength but also a degree of stiffness. As a result, HDPE is in demand for applications such as piping systems, packaging, and boat and canoe construction.
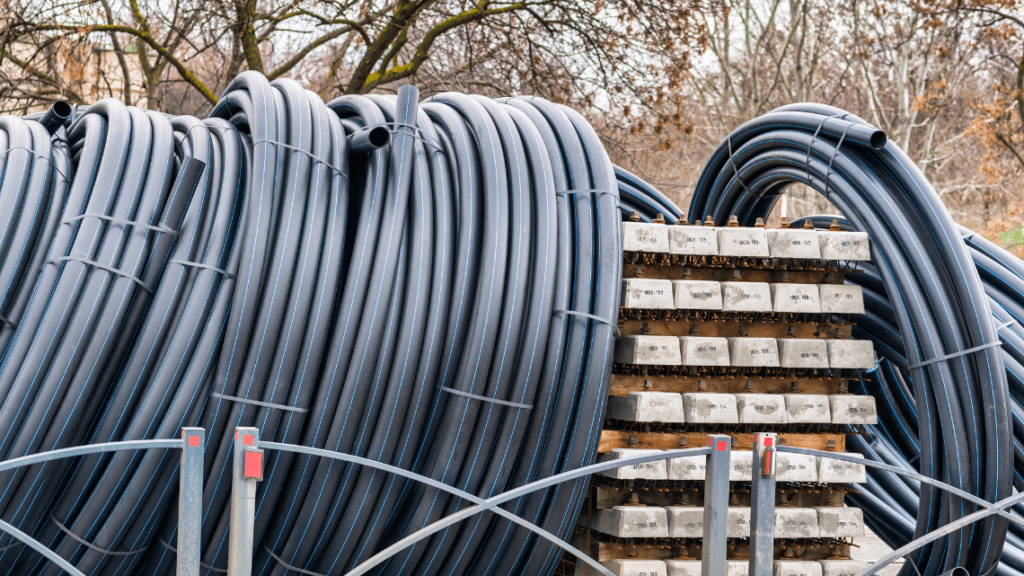
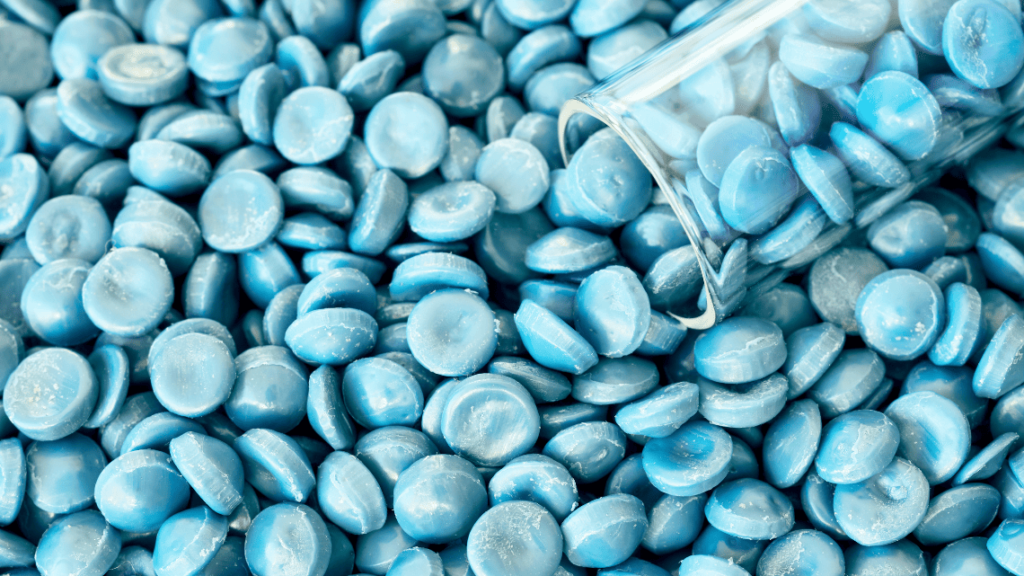
The melting point of high-density polyethylene
A central physical characteristic of HDPE is its melting point, which typically falls in the range of 120°C to 180°C.
A common method for determining the melting point is the use of a Dynamic Differential Calorimeter, also known as DSC.
This makes the material well-suited for various industrial manufacturing methods. A prime example is the extrusion process for producing bottles and containers. During this process, HDPE is heated to approximately 150°C to 160°C, close to its melting point, making it malleable. It is then blown into a mold and cooled, assuming its final shape.
Thanks to this specific temperature range, HDPE maintains high robustness and tightness during this processing – properties that are particularly essential for packaging cleaning agents or motor oils.
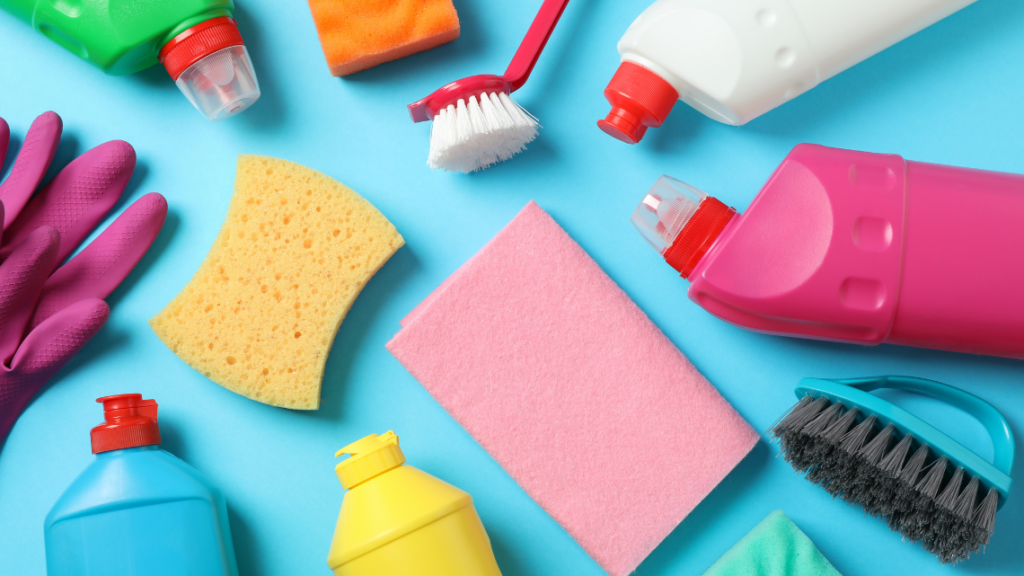
The robustness and glass transition temperature of HDPE
The robustness of HDPE at high temperatures opens up possibilities for applications where the material is exposed to extreme thermal conditions without losing its structure or functionality.
A prime example is geothermal piping systems. In these systems, hot geothermal heat circulates from the underground, reaching temperatures ranging from 50°C to 370°C, depending on depth and region, to heat buildings or generate electricity. HDPE pipes are present in this environment as they withstand hot liquids without losing their shape or breaking.
This thermal resilience also makes HDPE the top choice for other applications, such as radiant floor heating systems where warm water flows through the pipes, providing comfortable room temperatures.
The glass transition temperature (Tg) of High-Density Polyethylene (HDPE) typically falls between approximately -100°C and -130°C. This low Tg means that HDPE remains in a rigid and hard state at temperatures below this range.
The glass transition temperature is the temperature at which an amorphous polymer transitions from a hard, glassy state to a soft, rubbery state, or vice versa.
In the case of HDPE, this transition occurs at very low temperatures, reflecting its high rigidity and brittleness in the glassy state. The Chip-DSC can also precisely determine the temperature at which the glass transition occurs.
The Tg of HDPE is significantly lower than that of other polymers, making it suitable for applications requiring behavior at low temperatures. Knowledge of the Tg of HDPE is crucial for applications where mechanical properties and performance at different temperatures play a vital role.
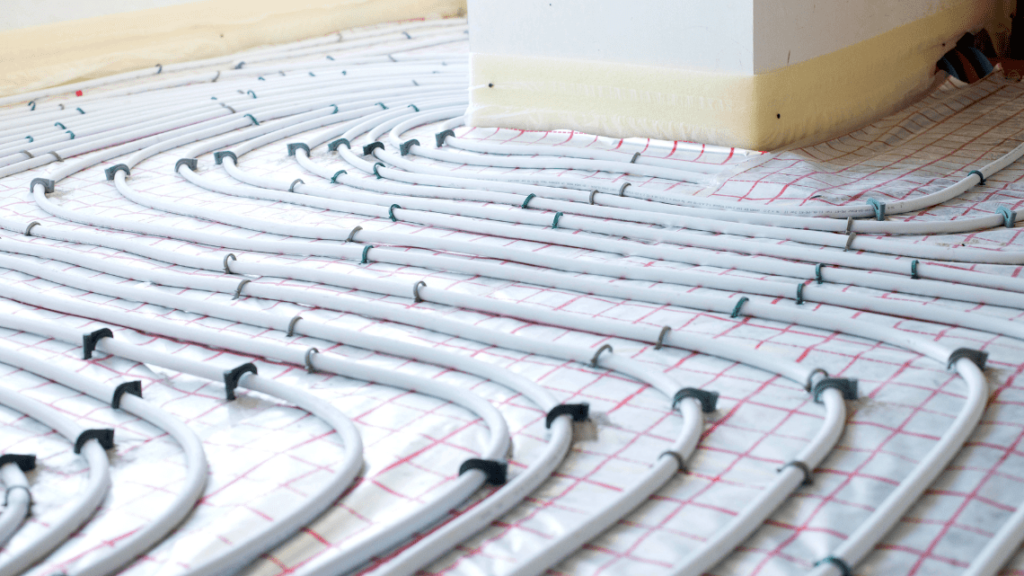
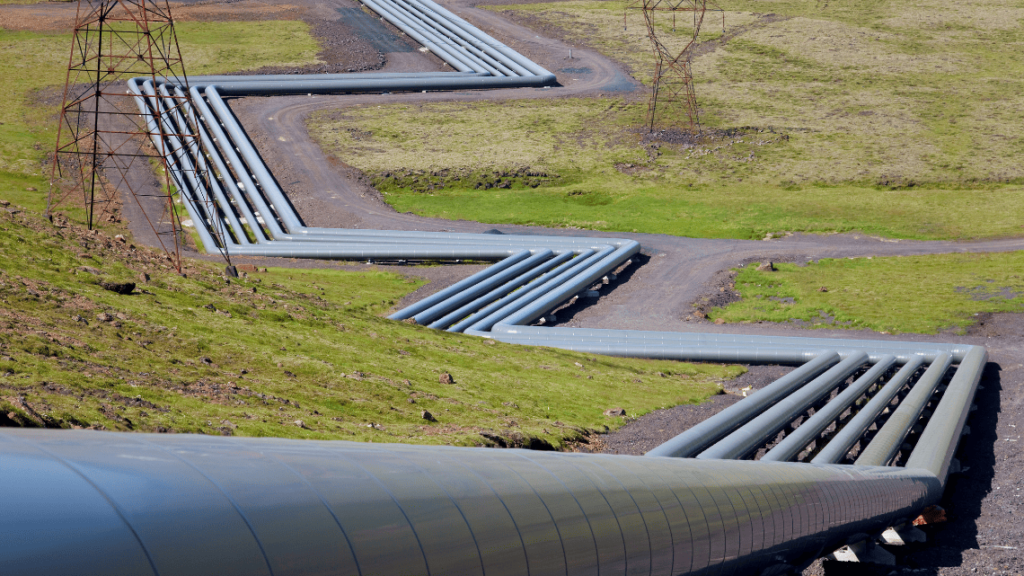
Different types of HDPE
There are various grades of HDPE, depending on molecular weight and branching. The numbers following HDPE, such as “500,” “300,” or “1000,” typically represent the molecular weight in thousands.
This means that HDPE 500 has an average molecular weight of approximately 500,000, HDPE 300 around 300,000, and HDPE 1000 roughly 1,000,000.
A higher molecular weight can result in increased strength, toughness, and chemical resistance, depending on the specific formulation and manufacturing method.
Some of the common grades include:
- HDPE 500:
- This type, with a molecular weight around 500,000, is known for its high impact resistance and is commonly used in canoe and boat construction. Due to its resistance to saltwater corrosion and robust nature, boats and canoes made from HDPE 500 are durable and require minimal maintenance.
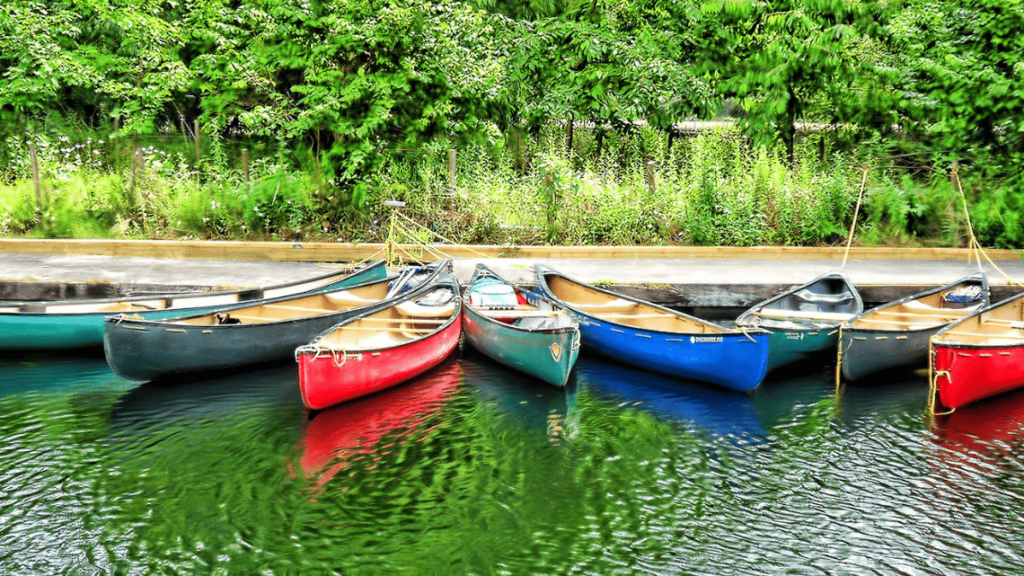
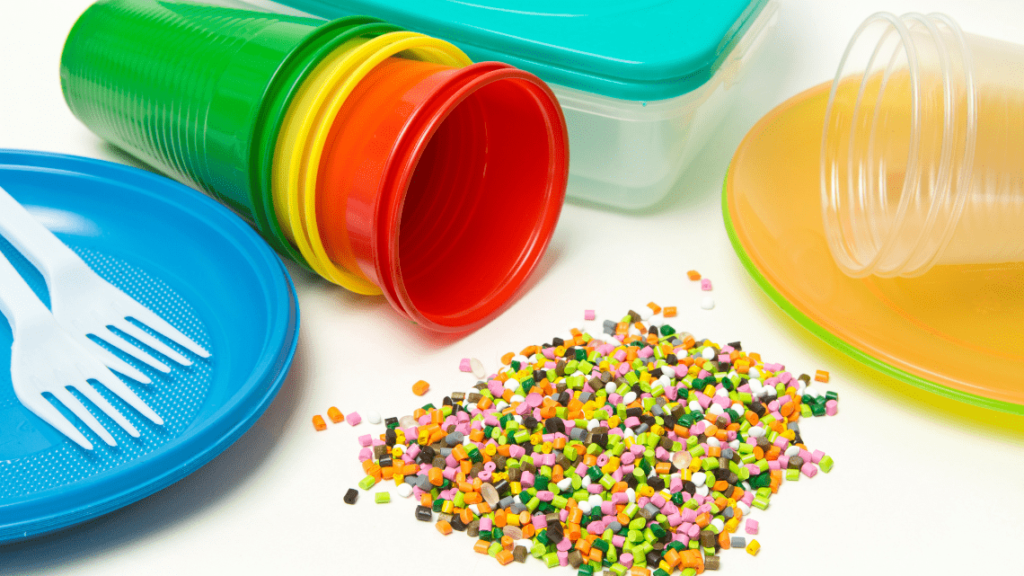
- HDPE 300:
- This type, with a molecular weight around 300,000, is commonly used for food packaging. Its resistance to chemicals and low water absorption ensure that food remains fresh and contamination is avoided. Additionally, HDPE 300 is FDA-compliant, meaning it is safe for food contact.
- HDPE 1000:
- With a molecular weight around 1,000,000, this type is commonly used in industrial applications due to its high abrasion resistance and resistance to chemical influences. An example is the production of sliding bearings or wear strips in conveyor systems, as these parts are subjected to constant friction.
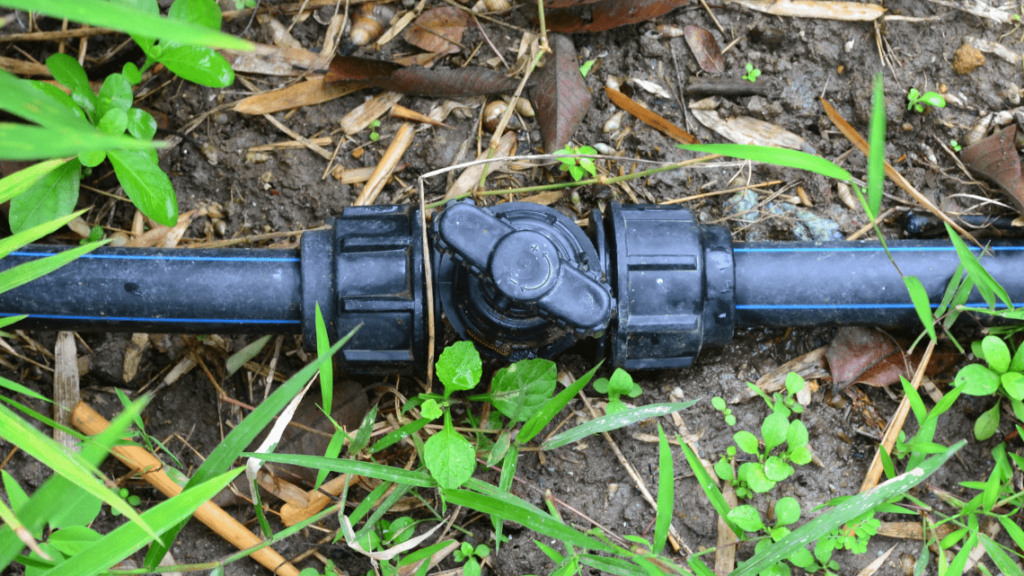
Depending on the specific requirements of an application, whether it’s resistance to UV radiation, mechanical strength, or suitability for food contact, a particular grade of HDPE can be selected to achieve the best results. This underscores the versatility and adaptability of HDPE in various industrial and commercial sectors.
Advantages of using high-density polyethylene
- Chemical Consistency
- Food-safe
- UV-Consistency
- Humidity resistance
- Durability and light weight
- Recyclability
- Versatility