Table of Contents
Materials that are processed in a liquid state of aggregation generally require a certain amount of time to cure. During this time, chemical and physical processes take place, leading to the hardening of the material. These processes are associated with the release or absorption of heat.
By recording the corresponding quantities of heat using differential scanning calorimetry (DSC), the course of the processes can be observed as a function of defined environmental conditions. The results provide information about optimum conditions for curing and allow conclusions to be drawn about the quality parameters of the material under investigation.
Curing of duroplasts and elastomers
Duromers or also duroplastics and elastomers are plastics that obtain their final strength by cross-linking macromolecules. Chemical bonds are formed at reactive groups.
The reactions start by raising the temperature and adding substances (hardeners) which form a bridge between the reactive groups.
Duromers form a close-meshed spatial network. They thus achieve a high degree of strength. The network of elastomers is wide-meshed. Its ball-shaped macromolecules can be pulled apart and return to their original state when the tensile force is removed. After complete cross-linking, the plastics are dimensionally stable. The process is called curing.
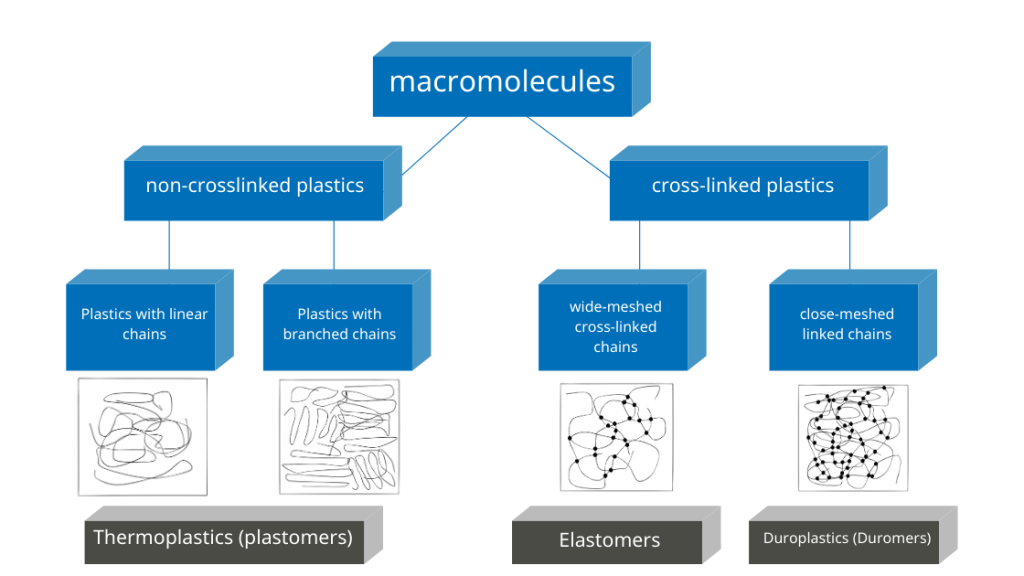
Examples of amorphous thermoplastics:
PS in toys, bobbins and films, PVC in containers, pipes, films, sound and heat insulation, tablecloths
Examples of semi-crystalline thermoplastics:
PE in containers, bottles, pipes, corrosion protection layers, PP in insulating films, pipes or adhesive tape
Examples of thermosets:
PF (phenolic resin) and UP (polyester resin) in heat-resistant and electrically insulated handles
Examples of elastomers:
polyurethane in resilient machine parts, sports fields, ski boots
During curing, a plastic passes through different phases. The starting material is usually in the form of a liquid solution. This means that the macromolecules are finely distributed in a solvent. At a minimum temperature that depends on the polymer system, cross-linking reactions begin in the solution, which results in a gel. The gel consists of the now insoluble, cross-linked components, the spaces between which enclose solvents. The mixture of sol and gel is initially rubber-elastic.
In thermoset systems, it reaches a glassy state with increasing cross-linking. Curing continues until the maximum degree of cure, at which point the sol is completely converted into a gel.
In elastomer systems, the gel retains its rubber-elastic state after complete cross-linking. The respective behavior is ultimately decisively determined by the glass transition temperature of the polymer system. In duromers it is above the curing temperature, in elastomers below. Above the glass transition temperature, the polymer is soft and the molecules are mobile, below it the material is rather solid and brittle.
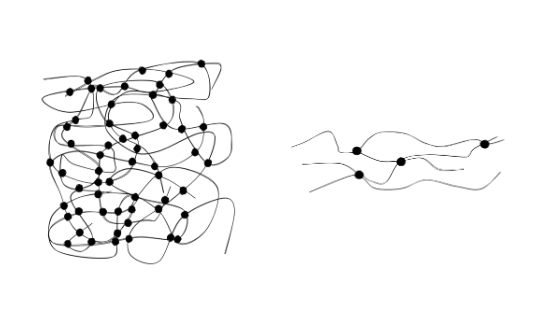
The curing level
The period of time during which curing takes place depends on the material properties of the polymer system and the temperature.
Below a system-dependent temperature limit, no significant cross-linking takes place. Although the sol becomes solid over a longer period of time, it can be liquefied again by heating.
Above this temperature limit, the crosslinking reactions start after a certain “rest period”. The “resting time” is shortened and the reaction rate increases as the temperature rises.
The cross-linking reaction is irreversible. How long the initial mixture can be processed depends on the resting time. This period is called pot life. It can be extended by adding inhibitors and shortened by adding catalysts.
The reaction rate determines how much time the polymer system needs until complete curing. The addition of inhibitors or catalysts can also be controlled by this time period. However, the temperature at which the crosslinking takes place has a significant influence. How far this has progressed is described by the degree of curing. It is the percentage of the mixture that has already cross-linked. The maximum degree of curing is reached when the entire sol has been converted into a gel.
The enthalpy of reaction
The cross-linking reaction is exothermic, i.e. it takes place under release of heat. Since the processes take place at constant pressure, only the heat amount that is not consumed by heat-related volume changes can be determined. This portion is the reaction enthalpy. It can be determined by thermal analysis for the reaction that has been completed.
By differential scanning calorimetry (DSC) can be determined, what heat quantity per time unit becomes free. This value corresponds to the reaction speed. The amount of heat released up to a certain point in time can be put into relation to the enthalpy of the reaction. This ratio is equal to the degree of curing.
The values obtained make it possible to determine the optimum curing temperature and degree of curing of samples, to determine the appropriate mixing ratio of sol and hardener and to assess the effectiveness of inhibitors and catalysts.