Table of Contents:
Additive manufacturing (AM), also known as 3D printing, is a process for building complex structures layer by layer. This makes it possible to build geoemetries that could previously only be visualised as 3D models quickly and in a resource-saving manner, and therefore represents an alternative to traditional subtractive processes. Although AM will play a central role in Industry 5.0, it has to compete with considerable manufacturing deviations such as high surface roughness, porosity, shrinkage effects and layer adhesion errors. One way to tackle these is through process control, where thermal analysis plays a key role. Due to the complex and dynamic manufacturing process, precise knowledge of thermal properties such as thermal conductivity, heat capacity and the thermal stability of the material is crucial for successful defect-free processing.
Key Additive Manufacturing Processes
The AM workflow begins with a digital CAD-based 3D model, which is typically further processed in the stereolithography data format stl. This model is cut into layers, which the 3D printer builds up one by one using various techniques, including:
- Powder Bed Fusion (PBF): Techniques like Selective Laser Melting (SLM) and Electron Beam Melting (EBM) melt powdered materials to form solid layers.
- Material Extrusion (ME): For example, Fused Deposition Modeling (FDM) wherethermoplastic filaments are melted and deposited layer by layer.
- Binder Jetting (BJ): A liquid binder joins layers of powdered material.
- Material Jetting: Droplets of liquid material are cured layer by layer.
- Photopolymerization (PP): Stereolithography (SLA) A photopolymer resin is cured with a light source.
- Sheet Lamination (SL): Thin layers of material (e.g. metal or paper) are cut and glued or welded together
These methods vary in speed, material compatibility, and application, making them suitable for different industries and use cases.
Thermal Properties and Their Importance in AM
The thermal properties of materials are crucial to the success of AM processes. For example, the thermal conductivity and capacity of the powder material has a direct influence on the energy input in laser-based processes such as SLM. Knowledge of the temperature dependencies of the thermal properties allows appropriate thermal management and enhanced control over the melt pool and therefore better defect management. Advanced thermal analysis techniques enable precise material characterization under process conditions and help manufacturers to select the right materials and optimize process parameters.
Materials in Additive Manufacturing
AM accommodates a wide range of materials, including:
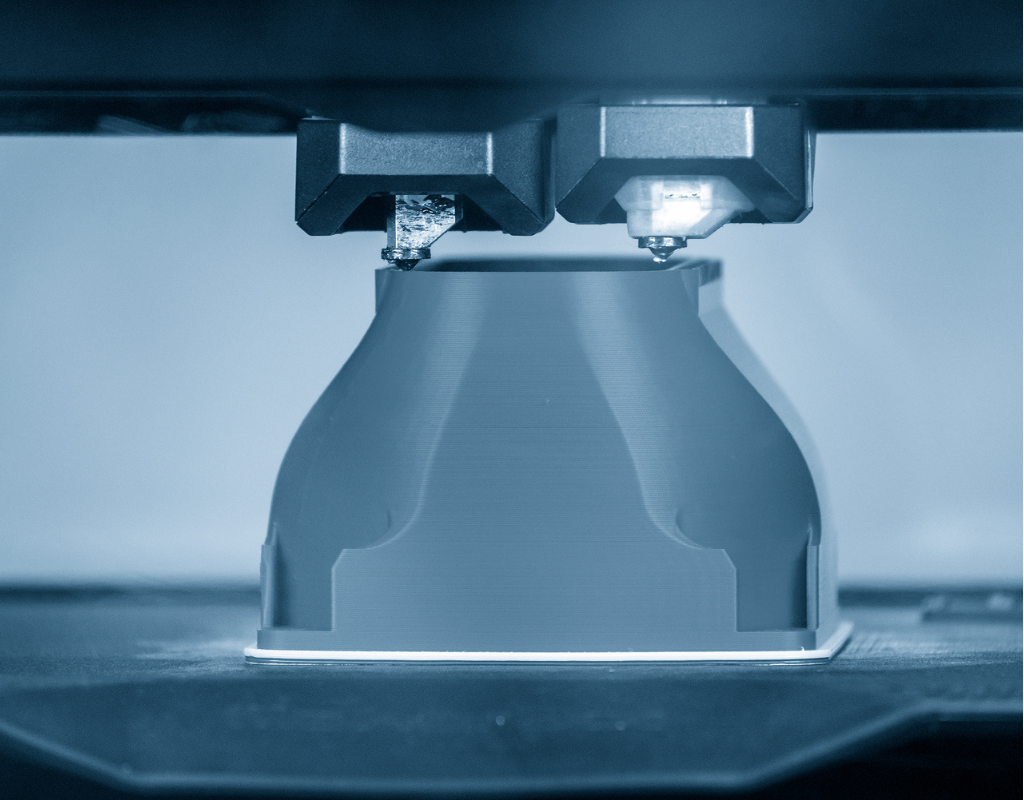
- Polymers: Typical representatives are PLA (ME), PA12 (PBF), epoxy resin (PP), PMMA (BJ), liquid photopolymers (MJ), PVC (SL)
- Metals: Metal alloys made of aluminium, medically compatible titanium alloys such as Ti64 and stainless steel are used in industry as well as in the aerospace industry.
- Ceramics: Materials like zirconia and alumina are ideal for bioactive and high-temperature components.
- Biomaterials: Hydrogels and collagen are paving the way for breakthroughs in medical applications.
- Composites: Advanced fiber-reinforced polymers are gaining popularity for structural applications.
Up to now, the high degree of freedom of the additive process has been restricted by the limited availability of materials. By incorporating fillers and additives, attempts are being made to constantly expand the product range and develop new applications that require further thermal analyses of partially new material mixtures.
Applications Across Industries
The versatility of AM extends across industries, from aerospace and automotive to healthcare and construction. For example:
- Aerospace: Lightweight, complex geometries improve fuel efficiency and performance.
- Healthcare: Custom implants and prosthetics enhance patient outcomes.
- Construction: Large-scale 3D printing of concrete is revolutionizing sustainable building practices.
Thermal analysis ensures these applications meet rigorous demands, such as operating in extreme temperatures or under mechanical stress.
Advantages and Future Potential
AM offers several advantages over traditional manufacturing:
- Complex Geometries: Enables intricate designs unachievable with conventional methods.
- Rapid Prototyping: Fast creation of prototypes from 3D models
- Material Efficiency: Reduces waste by using only the required material.
- Customization: Facilitates tailored solutions, particularly in healthcare.
- Cost-Efficiency for Small Series: Economical for low-volume production.
Future advances in materials science and process automation, such as AI-supported optimisation, will exploit the potential of AM and make the manufacturing process ready for Industry 5.0. Thermal analysis as a pre- and post-process will remain a constant cornerstone and make an important contribution to the development of new materials and processes.
Scientific Perspectives
Recent research highlights the integration of computer modelling and thermal analysis [7] to simulate and predict heat distribution in real time through digital twins to optimise process control and energy consumption. The permanent integration of thermal analysis into the manufacturing process as an in-situ or in-process measurement technique represents an essential step in the further development of process understanding.
- https://mitsloan.mit.edu/ideas-made-to-matter/additive-manufacturing-explained
- https://2onelab.com/de/lernen/blog/was-ist-additive-fertigung/
- https://www.3ddruck-transmit.de
- https://www.ingenieur.de/technik/fachbereiche/3d-druck/was-ist-additive-fertigung-definition-anwendung-potenzial/
- https://additive.industrie.de/werkstoffe-fuer-die-additive-fertigung/
- https://www.haw-landshut.de/aktuelles/beitrag/additive-fertigung-zu-studieren-waere-mein-traum
- https://www.materials.fraunhofer.de/de/strategische-initativen/materialien-fuer-die-additive-fertigung-.html
- https://www.chemietechnik.de/energie-utilities/materialien-fuer-die-additive-fertigung-im-ueberblick-393.html
- https://boehl-kunststofftechnik.com/additive-fertigung
- https://www.iph-hannover.de/de/dienstleistungen/fertigungsverfahren/additive-fertigung/