Table of Contents
The origin of acrylonitrile butadiene styrene (ABS)
Acrylonitrile-Butadiene-Styrene, commonly known as ABS, is a copolymer and a central component in various industrial and commercial sectors. ABS is produced on a large scale through graft copolymerization, in which styrene and acrylonitrile are polymerized in the presence of polybutadiene.
This process leads to the formation of the terpolymer ABS. Alternatively, ABS can also be produced by mechanically blending styrene-acrylonitrile copolymer (SAN) with polybutadiene, resulting in what are known as ABS blend polymers. Transparent ABS, for example, is produced by adding polymethylmethacrylate (PMMA).
Approximately 50% of the ABS produced in Western Europe is consumed by the automotive and electrical industries, as ABS is well-suited for coating with metals and polymers and finds uses in various applications such as toys, automotive parts, and household appliances.
This thermoplastic exhibits remarkable versatility with moderate crystallinity, which defines its essential characteristics, including high impact resistance, toughness, and heat resistance. This unique composition of ABS allows it to transition from being robust to possessing a certain degree of flexibility.
PROPERTIES | ABS | POLYSTYRENE (PS) | POLYETHYLENE (PE) |
---|---|---|---|
Impact strength | High | Low | Low |
Heat resistance | Good | Bad | Bad |
Chemical resistance | Moderate | Bad | Good |
Surface hardness | High | Low | Low |
ABS offers several advantages over other polymers. Compared to polystyrene and polyethylene, it exhibits high impact resistance, making it suitable for applications requiring long-term durability.
Furthermore, ABS demonstrates good heat resistance, which is a valuable property for various engineering applications. Additionally, in comparison to polystyrene and polyethylene, ABS has higher surface hardness, resulting in improved scratch resistance and overall durability.
The crystallinity of ABS
ABS is characterized by a balanced mixture of amorphous and crystalline structures, resulting in an ordered yet flexible molecular arrangement.
The crystallinity of a material indicates the extent to which its molecules are arranged in an ordered, regular structure. In pure polymers, this order can often be very pronounced, leading to a high degree of crystallinity.
In contrast, ABS exhibits moderate crystallinity, allowing it to possess a combination of strength, toughness, and dimensional stability. This intermediate level of crystallinity is mainly attributed to the interaction of various monomers in the copolymer, each contributing different properties to the overall blend.
A Differential Scanning Calorimeter (DSC) enables precise analysis of the crystallinity of materials like ABS by tracking the heat energy absorbed or released by the material during controlled temperature changes. This method allows for the identification of characteristic transition points such as the melting temperature and softening point and supports the exploration of phase transitions within the material.
Let’s start with strength: ABS possesses impressive tensile and impact strength. This means that even if children drop them, step on them, or mechanically stress them in various ways, the building blocks do not easily break or splinter. This resistance to mechanical stress ensures that LEGO bricks are not only safe to use but also exceptionally durable.
The long-lasting color brilliance of ABS components, such as LEGO bricks, can be attributed to the stability of its polymer chains in the crystalline region. This structure impedes the diffusion of oxygen and UV light that could degrade color pigments.
The molecular configuration of ABS counters the photooxidation process, allowing the bricks to maintain their vibrant color over extended periods. This property is crucial for toys where colorfastness plays a significant role in visual perception and appeal.
Scientific studies indicate that the color stability of polymers can be further enhanced by incorporating antioxidants and UV stabilizers into the polymer matrix, slowing down the aging process.
Furthermore, dimensional stability of ABS plays a crucial role in LEGO bricks. Precise dimensions and fit are essential for assembling and disassembling the bricks.
ABS ensures that the bricks maintain their shape even after countless assembly and disassembly cycles and consistently fit together precisely. A LEGO brick must provide consistent clutch power to ensure that the creations children build remain stable and intact.
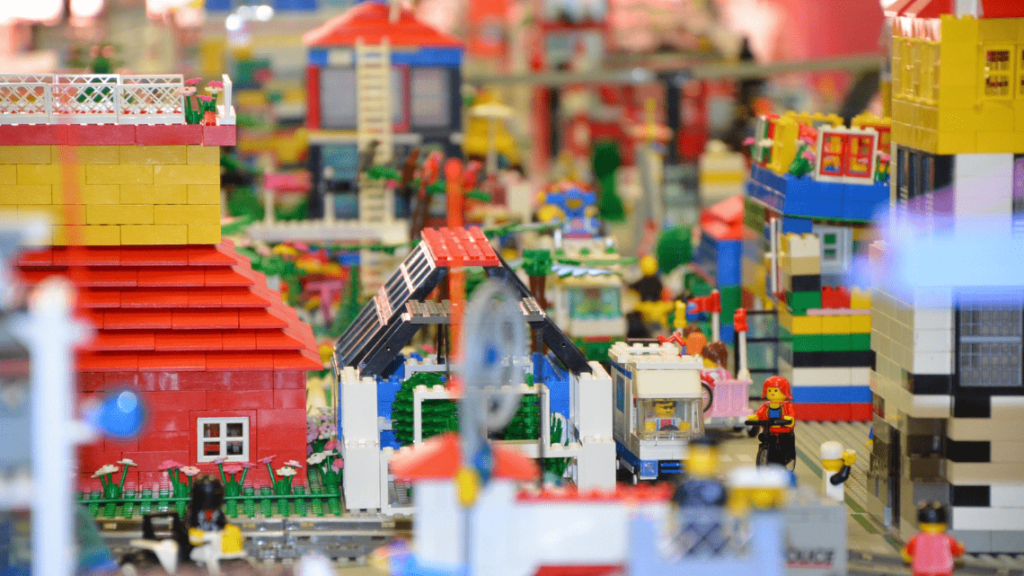
The melting point of acrylonitrile-butadiene-styrene
The melting point of ABS, typically ranging between 190°C and 220°C, allows it to be molded into heat-resistant, complex structures that are advantageous in the automotive industry. The melting temperature is usually measured using a Dynamic Differential Calorimeter.
The thermoplastic properties of ABS enable precise shaping through injection molding processes, resulting in components with high precision and detail. The molecular structure of ABS supports the retention of mechanical properties even after repeated heating and cooling, which is essential for the production cycles in automobile manufacturing.
Furthermore, the incorporation of additives such as UV stabilizers and impact modifiers provides the opportunity to selectively modify the material performance of ABS based on specific requirements. This ensures that ABS components like dashboards and bumpers maintain their functionality and aesthetic quality even under long-term exposure to various weather and operating conditions.
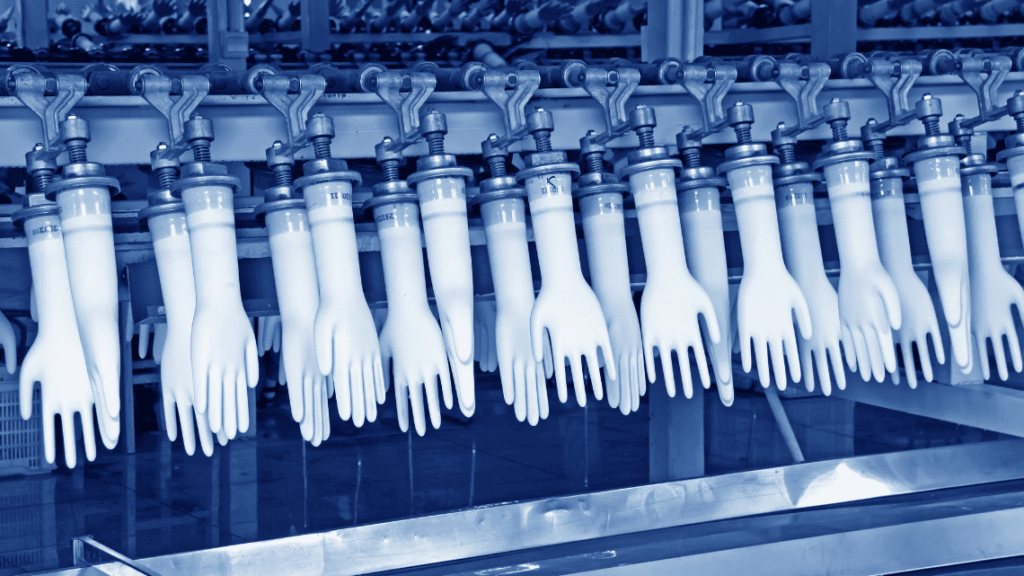
The thermal stability of ABS
The versatility and thermal stability of ABS are attributed to its molecular composition, which provides an effective balance between strength, toughness, and heat resistance.
The determination of ABS’s thermal stability can be efficiently carried out using devices such as the STA L82 or a Chip-DSC (DSC). These devices enable a detailed analysis of the thermal characteristics of materials, including the assessment of their behavior during thermal decomposition.
Its adaptability allows for the production of a variety of shapes, from rigid to slightly elastic structures. These properties make it ideal for enclosures of electrical appliances that need to be resistant to both physical impacts and high temperatures. The thermal stability of ABS, complemented by specific additives, ensures that it maintains its structural integrity and functionality even during extended operation and under variable environmental conditions.
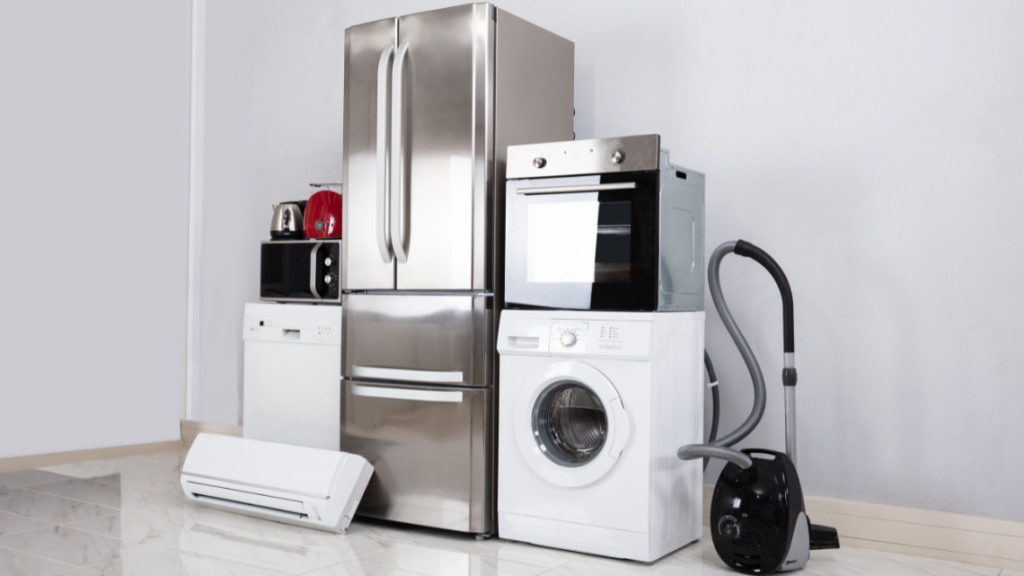
The glass transition temperature of acrylonitrile-butadiene-styrene
The Glass Transition Temperature (Tg) of ABS is approximately 105°C and is a critical parameter that determines its behavior under thermal stress.
The Tg can be determined using several methods, including Thermomechanical Analysis (TMA) and Dynamic Differential Calorimetry (DSC). Instruments such as the DIL L75 or a TMA are capable of evaluating and measuring the mechanical properties of a material, including strength and deformability.
Below the Tg, ABS maintains its rigid, glass-like structure, while above this temperature, it transitions into a rubbery, more flexible state. This property is particularly relevant for applications in electrical enclosures where materials are required to withstand thermal fluctuations without significant deformation or loss of strength.
The proximity of Tg to the operating temperature in many applications means that ABS retains its mechanical properties under normal operating conditions, making it an optimal material for electronic components that require a combination of mechanical stability and thermal resistance.
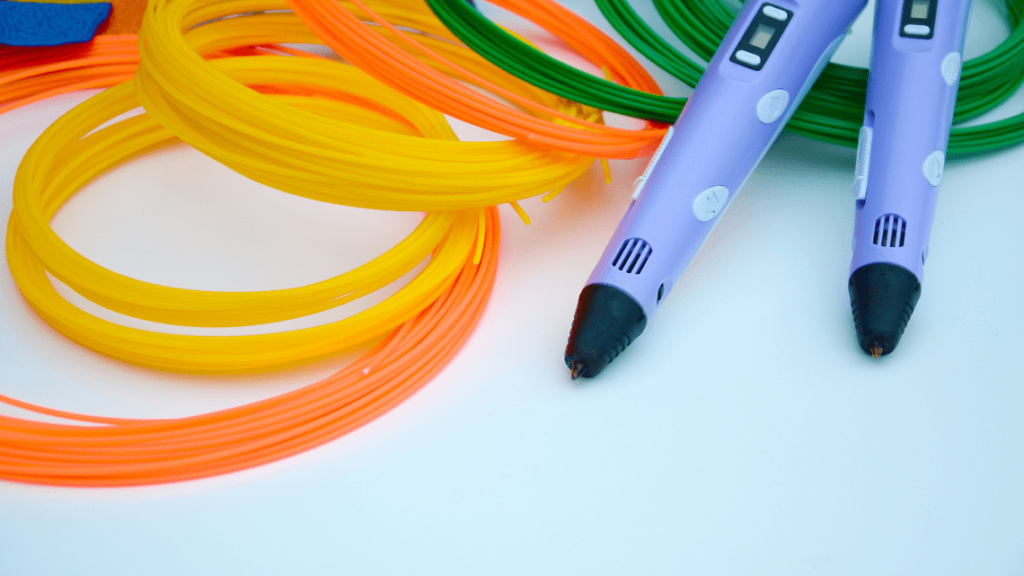
Different types of ABS
With regard to the different types of ABS, differences in crystallinity and the additives added ensure a range with different physical properties.
For example:
- Toys:
Often made from a type of ABS known for its colorfastness and mechanical strength.
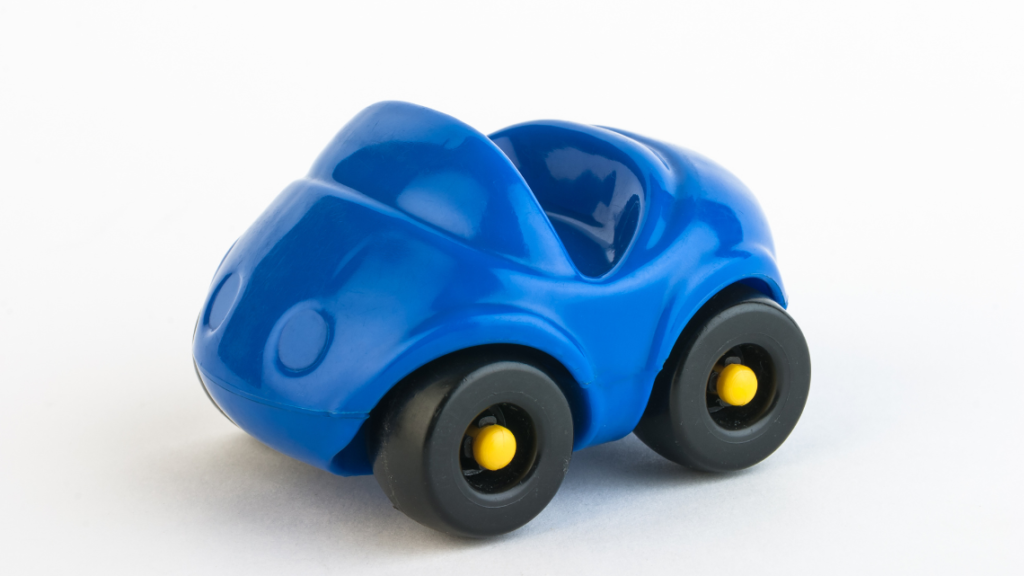
- Pipes and Fittings:
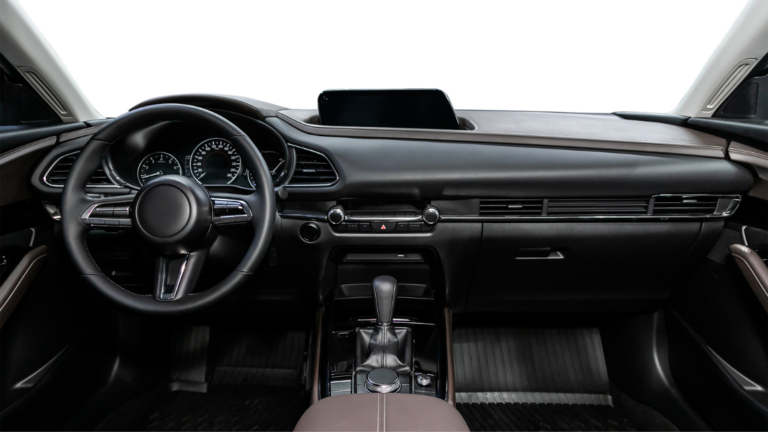
- ABS, known for its chemical resistance and durability, is often used.
- Computer Accessories:
A more flexible ABS is often used for its durability and dimensional stability.
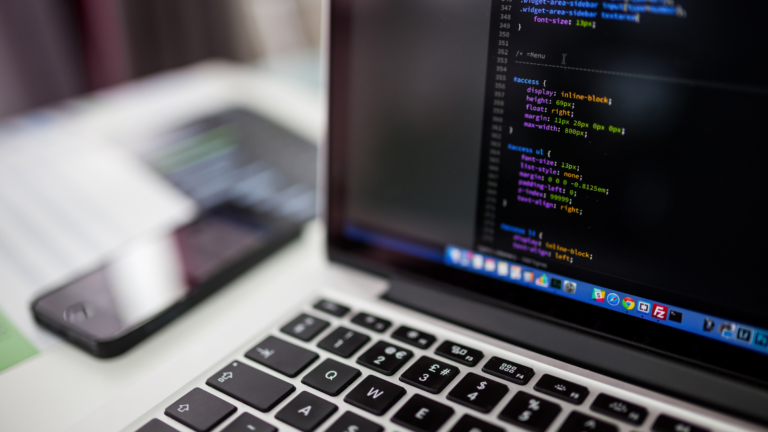
Application: Characterization of Polymers Using an Acrylonitrile-Butadiene-Styrene Sample
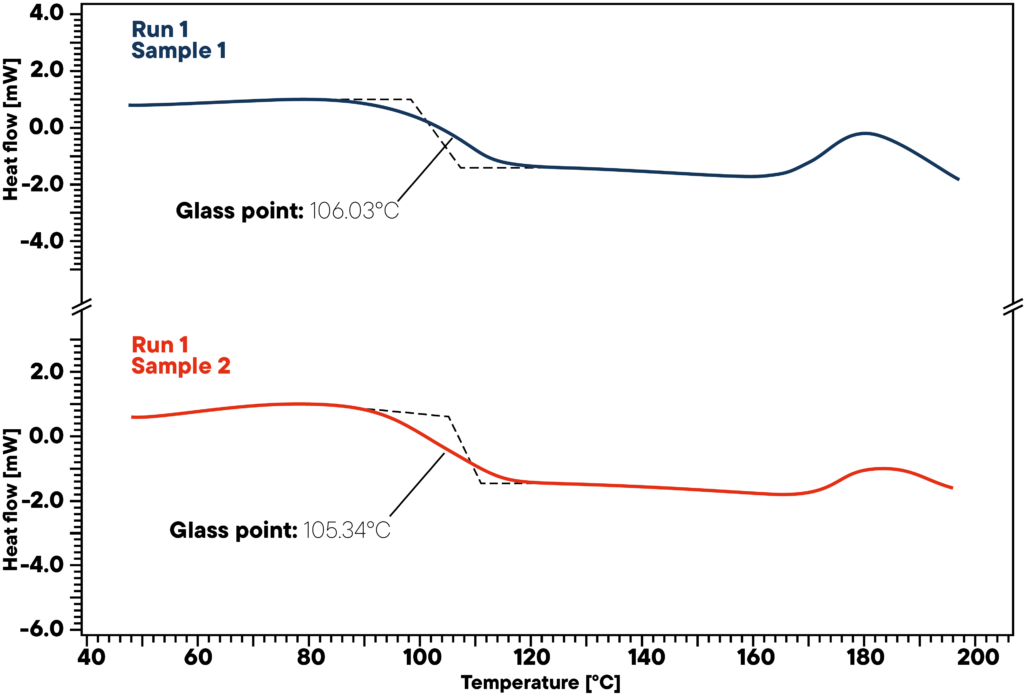
In thermal analysis, it is often characterized by its glass transition at ~100°C. The glass transition temperature is influenced by the amount of monomers used. Detecting Tg is therefore a good way to assess the quality of the raw materials.
In this example, two different ABS samples were measured using Chip-DSC 1 with a heating rate of 25 K/min. Both curves show the first heating cycle, and in both cases, the typical glass transition of ABS at approximately 100°C is evident.