Table of Contents
Thermal analysis of 3D printing ceramics
Ceramics are used in many areas of industry. As a rule, ceramics are first formed as green bodies from raw mass, before this “green body” is then treated and fired in a special way (so-called sintering) to harden it and bring it into its final form.
Depending on the industry, this can be simple tableware, decoration or sanitary ware, but also technical ceramics such as prostheses, or various technical components. A ceramic workpiece is usually fired in a kiln after initial mechanical processing. It is exposed to temperatures of between 900 °C and 1400 °C.
This is done by heating in a defined time interval at a steadily increasing temperature, but also at precisely defined isothermal intervals to control chemical reactions during firing of the ceramic and to control the degassing of water vapor, carbon dioxide and other admixtures. After the initial firing, a glaze is often added to the ceramic and then the piece is fired again to fully cure it.
The entire process takes several hours and is therefore not inconsiderably time-consuming. In addition, it cannot be guaranteed that the workpiece will come out of the kiln undamaged after firing; various errors (lack of material, incorrect firing process, etc.) can occur, which can lead to breakage or cracks in the ceramic.
A more modern and simpler solution for firing a wide variety of ceramic components is additive manufacturing. In the case of ceramics, this is often referred to as 3D printing. This is a manufacturing process in which material is applied layer by layer to create three-dimensional objects.
The build-up is usually computer-aided design (CAD) and one or more liquid or solid materials are used as the starting material according to specified dimensions and shapes. During the build-up by means of printing process, chemical curing or melting processes take place, often controlled by means of temperature or laser. It is even possible to use a 3D scanner for a model.
The advantage of the method over conventional firing processes is clear: By applying the ceramics in layers, it is possible to produce filigree and complex structures for which the risk of breakage during the firing process would be particularly high. In addition, enormous time savings are achieved, as an additively sintered or 3D-printed workpiece can be manufactured much more quickly due to the fact that the firing process in the furnace is not necessary.
Compared to all material-removing processes such as cutting, turning and drilling, 3D printing has the advantage of eliminating the additional machining step after the original mold. In most cases, the process is also more energy efficient, especially if the material only needs to be built up once in the required size and mass. It is also advantageous that different materials can be processed in a single machine.
Originally, the process of 3D printing was first applied and developed in the polymer industry, as plastics are easy to melt and handle and do not require sintering or curing. By heating just above the softening point and rapidly cooling the printed filament, structures could be created in real time. However, the process has rapidly evolved to print not only various polymers, but now metals and ceramics as well, making 3D printing a versatile option for manufacturing.
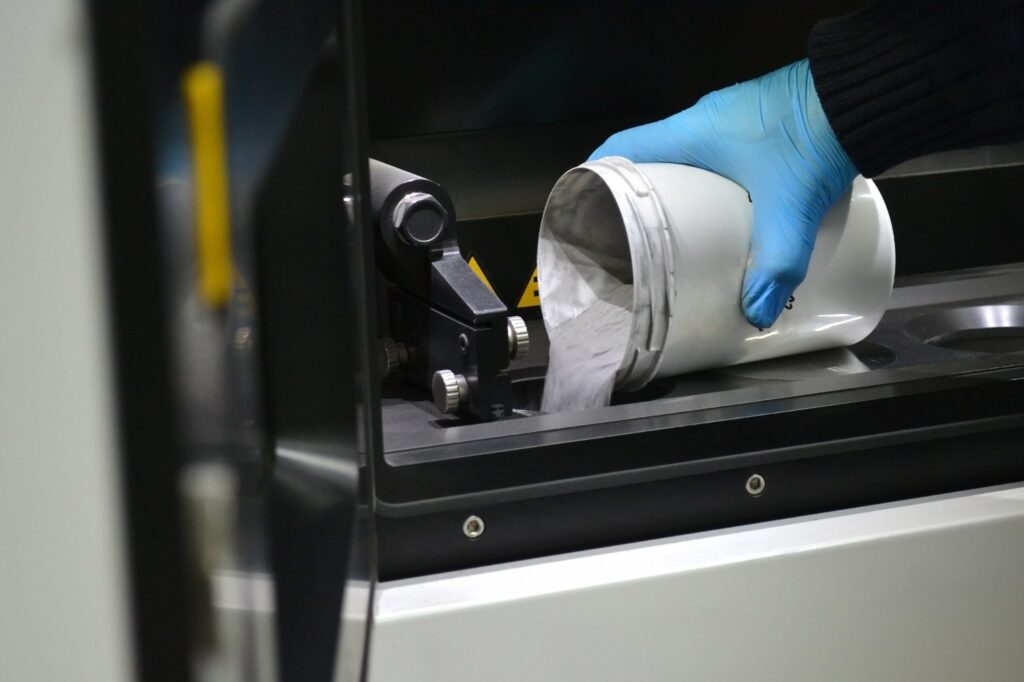
Typical materials now used for 3D printing include plastics, ceramics, metals or carbon compounds such as graphite. The most important techniques here are laser beam melting and electron beam melting for metals, laser sintering for polymers, ceramics and metals, stereolithography and digital light processing for liquid resins, and polyjet modeling and fused layer modeling for plastics and resins.
The manufacturing processes of additive manufacturing can be divided into seven main categories and are now also described in detail in some standards(DIN EN ISO/ASTM 52900, formerly ASTM F2792):
- Binder output
- Material output
- Powder bed fusion
- Material extrusion
- Vat photopolymerization
- Targeted energy deposition
- Sheet lamination
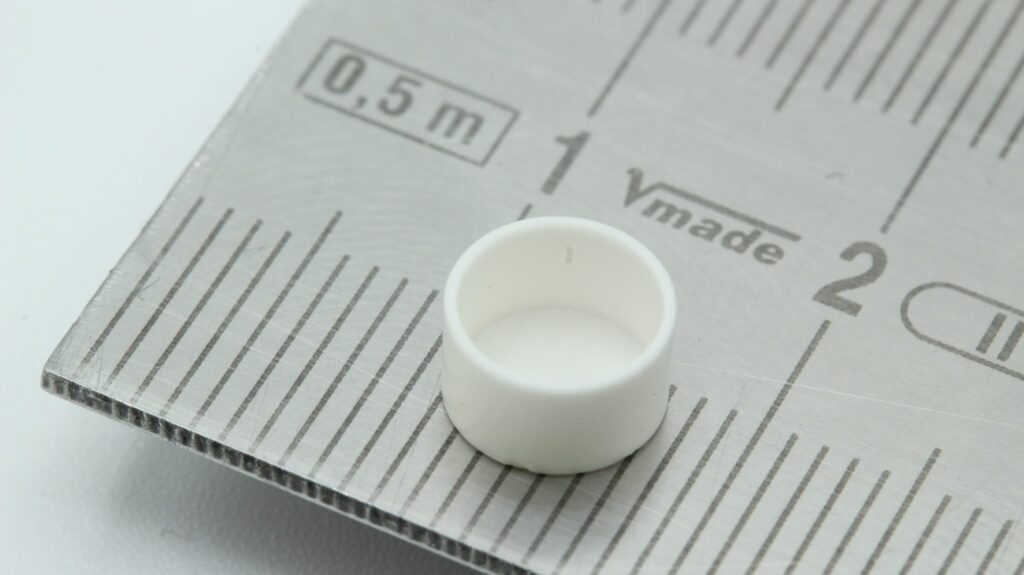
The main difference between them is how the layers are applied to create the parts and what materials are used. The most important factors in choosing the machine and 3D printing process are speed (depending on the size of the object) and cost (for material and machine). Materials in general: metal, ceramic, plastic.
The main field of application of additive manufacturing technology is still research and, above all, product development or prototype construction in industry. It is ideally suited for the production of models, prototypes, tools or specific products, as no special tools are required and the conversion from drawing to model can be realized very quickly.
Other areas of application are primarily medical technology, where specially adapted prostheses and implants (especially also in dentistry) have to be made, often individually customized. But more unusual fields of application, such as sculpture and art, also use additive manufacturing to produce sculptures. Meanwhile, 3D printers can also be used in private use, as the processes and printers have now reached production maturity and are available to the public at relatively low cost. In the household, plastic products in particular, such as toys, spare parts or small holders, can be produced easily and without much prior knowledge.
For ceramics, the following methods are used for 3D printing:
- Powder bed fusion processes, such as selective laser sintering (SLS). This process can generally be used to print polymers, ceramic powders or metals. It involves melting the material powder with a high-energy laser to create completely dense materials layer by layer. A thin layer of the powder is placed on a tray using a nozzle. A laser then begins to sinter the powder locally, creating the first layer. A variation of this is 3D inkjet printing. Here, a binder is printed onto a layer of powder (plaster or resin) in the cross-section of the part using an inkjet-like process. An advantage of powder bed fusion techniques is that the excess powder serves as a support for the printed object.
- Fused Deposition Modeling (FDM) or Fused Filament Fabrication (FFF) processes small patrices of the desired ceramic.
- To make this work, a specific binder is used in the filament, usually a special plastic that holds the ceramic powder together. The filament is then heated to such an extent that it liquefies and can be printed, just like a conventional plastic filament. The ceramic grains here have a diameter of about 1-2 µm.
- Thus, they come directly out of the nozzle when printing with the plastic and you can print the desired layers directly.
- Only the plastic, which holds the powder together and transports it, melts during this process and thus serves as a binder. The end result is a printed mold, but it is still essentially the ceramic powder rather than a solid ceramic body.
- This is not yet the final product; it is a green compact that must first be reworked.
- Finally, a special process removes some of the plastic. This is followed by the sintering process, in which the workpiece is exposed to high temperatures and chemical substances in a special furnace.
- During this process, the ceramic parts combine and the plastic is completely removed. Thus, FDM is ultimately very similar to the original ceramic firing process, since one only saves one firing step, but still has to carry out the second.
- To make this work, a specific binder is used in the filament, usually a special plastic that holds the ceramic powder together. The filament is then heated to such an extent that it liquefies and can be printed, just like a conventional plastic filament. The ceramic grains here have a diameter of about 1-2 µm.
The right conditions for the material to be used in a 3D printer depend on the temperature behavior such as the melting temperature and how the material expands under temperature or what thermal conductivity is present. It therefore makes sense to extensively test the thermal properties of the materials used for 3D printing. The following devices are relevant for these investigations:
- Classic dilatometry (DIL) can be used to extensively investigate the thermal linear expansion and sintering behavior of solids and powders. This means that dilatometry is now a standard procedure in ceramic production.
- In addition, various methods for investigating thermal conductivity are useful in order to simulate and control the temperature distribution and conduction in the workpiece. The most common methods here are flash techniques such as the laser flash method (LFA), in which the temperature and thermal conductivity of solids or powders can usually be measured using a high-energy flash of light. There are also hot-wire methods such as the Transient Hot Bridge (THB), which can provide reliable heat transfer values relatively quickly at room temperature. The Trans-Interface Material Tester (TIM), a variation of the guarded-hot-plate method, is also suitable for pastes and powders and can primarily measure different bulk densities and the resulting changes in thermal transport properties.
.
Once a component is manufactured, it is important to determine the thermal and mechanical property requirements of the component and develop them with a design specifically tailored to the process. This is usually true regardless of the manufacturing process used to make the component. However, in the case of additively manufactured components, it is particularly necessary to check the mechanical properties, as these may be different from those of a cast or fired object due to the layer structure. Particularly in the case of ceramics, the workpiece shrinks massively after sintering or additive deposition, and there may be various sources of defects that lead to material failure. Here, too, a dilatometer is usually used, and in some circumstances even thermomechanical analysis (TMA), which is capable of accurately recording the mechanical material properties by means of bending, tensile and compression tests.