Time-domain thermoreflectance (TDTR)
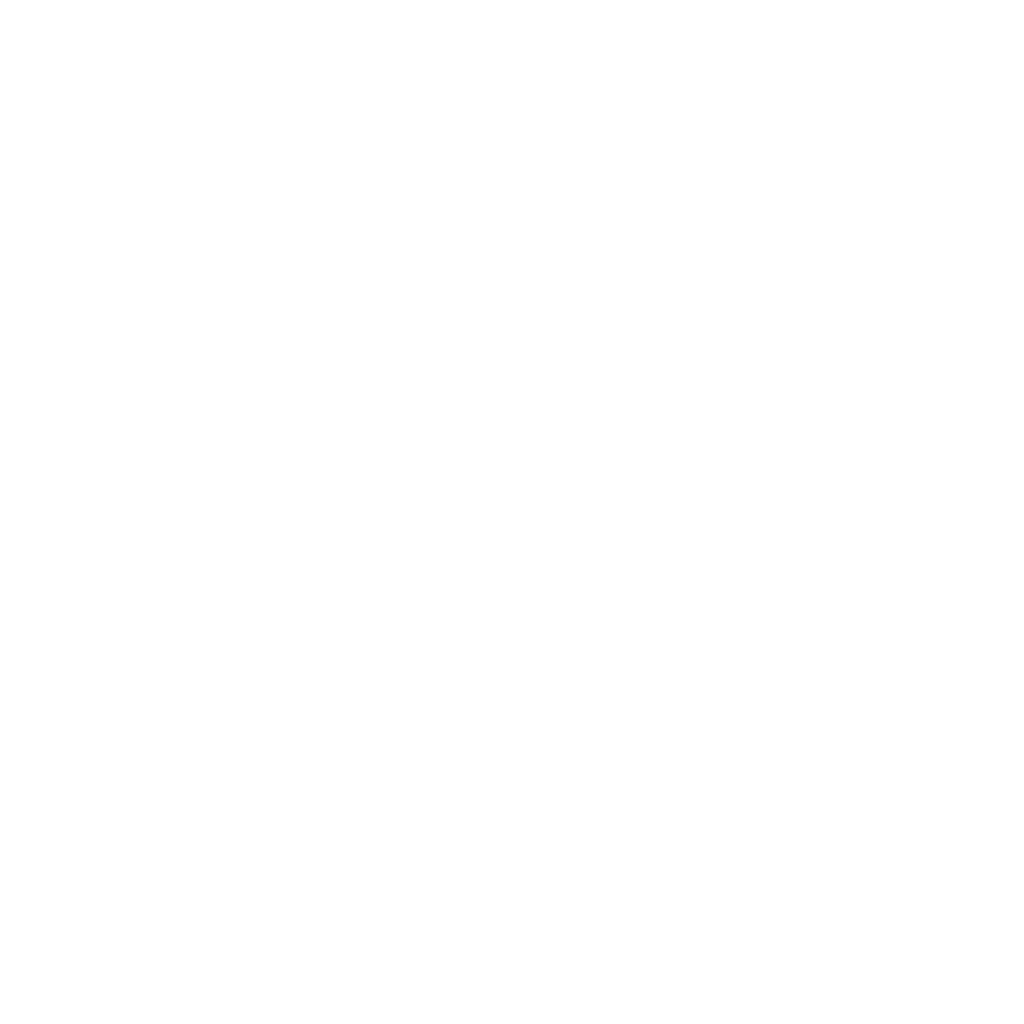
Time-domain thermoreflectance (TDTR)
During the past decade, Time-Domain Thermoreflectance has emerged as a powerful, general-purpose tool for the measurement of the thermal transport properties of materials. TDTR is applicable to materials with a wide range of properties and sample geometries. High throughput mapping of thermal conductivity as a function of position is enabled by focusing the laser spots and high signal-to-noise ratio.
Applications of thermal conductivity mapping include the analysis of metallurgical phase diagrams, and characterization of thermal barriers and coatings for nuclear fuels.
Experimental setup for TDTR thermal diffusivity measurements including pump and probe laser source
Since TDTR is an optical, non-contact method, it can be directly applied to samples in optical cryostats or high temperature microscope stages; and samples exposed to other extreme conditions such as the high pressure environment of a diamond anvil cell.
The approach requires the deposition of a metal film transducer on the sample of interest, for heating of the transducer by a pump optical pulse, and measurement of the changes in reflectivity of the transducer for thermometry.
The data analysis is performed using the analytical solution of the diffusion equation in cylindrical coordinates. The determination of thermal transport properties by TDTR is typically accomplished by adjusting free parameters in a thermal model, in order to obtain the best fit between the predicted and measured thermal response of the sample.
The free parameters are the unknown thermal transport properties, e.g., the thermal conductivity of a thin. The use of single objective lens and integration of the pump and probe beams into an optical imaging system have made the alignment and focusing of the pump and probe beams fast and convenient.
Using TDTR in daily practice, it requires that the surface of the sample is smooth enough so that any undesired modulation of diffuse scattering does not produce a significant contribution to the desired signal produced by the thermoreflectance of the metal film transducer.
TDTR is mostly sensitivity to the thermal conductivity in the through-thickness direction, i.e., heat transport in the direction anti-parallel to the surface normal. For thermally anisotropic materials such as superlattices, textured polycrystalline films, and anisotropic crystals, knowledge of the in-plane thermal conductivity is also desired and can be measured using another approach, e.g. a suspended hotwire approach.
The most common implementation of TDTR uses a ND:YAG or Ti:sapphire laser oscillator as the light source. The laser oscillator produces an optical pulse to locally heat the transducing layer and thus the underlaying sample layer. The probe path uses a continuous wave (CW) laser to detect the local temperature rise. Depending on the utilized material of the transducing layer (e.g. Au, Al or Pt), the wave length of the probe laser has to be selected (~473 nm to 532 nm or 785 nm to 808 nm).
The term “thermoreflectance” refers to the fact that the probe measures changes in the temperature of the sample through the dependence of the optical reflectivity R of a metal film transducer on temperature, T; dR/dT is the coefficient of thermoreflectance.
Raw data of the thermal diffusivity measurement of two SiO2 thin films with varying thickness, measured with the Linseis TF-LFA
Which properties are determined?
TDTR is used to characterize the thermal transport properties of materials, mostly thin films and coatings, as well as for the investigation of thermal interfaces. It has been applied across the entire range of thermal conductivity from diamond and high thermal conductivity metals to the ultralow thermal conductivity of fullerene derivatives. Essentially the same method can be applied to bulk materials, thin layers, and individual interfaces.