Description
To the point
The Linseis DIL L75 HP (DIL HP L70) high-pressure dilatometer opens up completely new areas of application in thermal analysis. The system can measure changes in length in a temperature range from RT to 1100/1400/1800°C and in a pressure range up to 100/150 bar. This makes the device the only high-pressure dilatometer available worldwide. A water vapor generator and complex gas controls are optionally available.
To obtain further information about your sample, you can of course couple the measuring device with a mass spectrometer (QMS) or FTIR system at any time to analyze the exhaust gases. This coupling is realized by means of specially integrated hardware and software concepts from LINSEIS. Several libraries are available for interpreting the results.
Unique Features
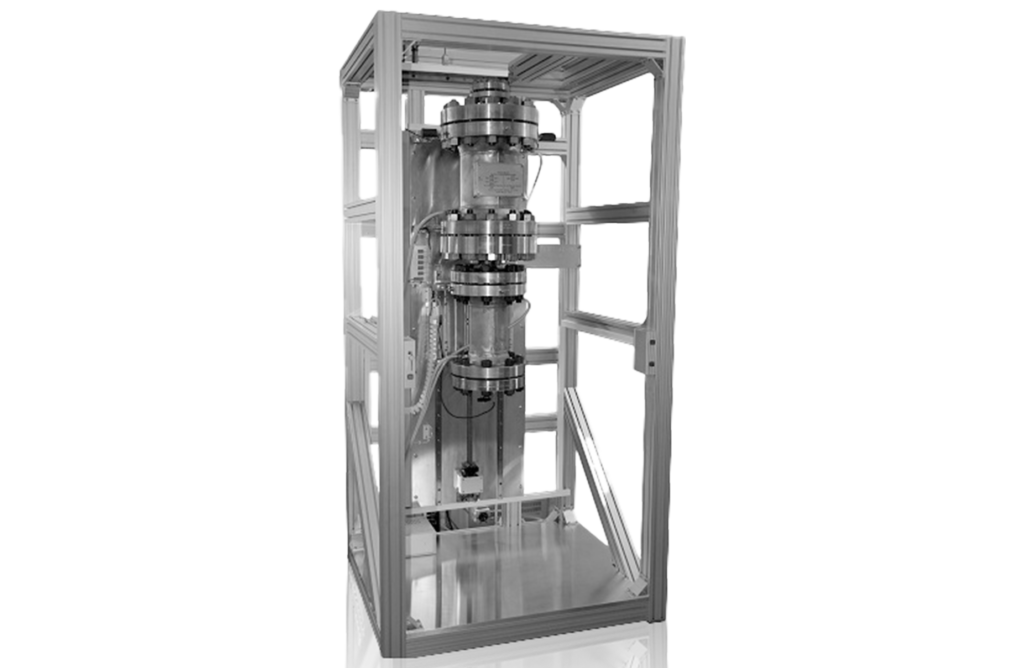
Measurement of length
changes at temperatures
from RT to 1800°C and
pressures up to 150 bar
Optional steam generator
and complex gas controls
Coupling with mass spectrometer
(QMS) or FTIR system for analyzing
the exhaust gases
Integrated hardware and software
concepts with extensive libraries
for interpreting results
Questions? We're just a call away!
+1 (609) 223 2070
+49 (0) 9287/880 0
Our service is available Monday to
Thursday from 8-16 o’clock
and Friday from 8-12 o’clock.
We are here for you!
Specifications
MODEL | DIL L75 HP/1 (DIL HP L70)* |
---|---|
Temperature range: | RT up to 1100°C |
Max. pressure: | max. 150 bar |
Vacuum: | 10E-4 mbar |
Sample holder: | fused silicia < 1100°C, Al2O3 < 1750°C |
Max. sample length: | 50 mm |
Sample diameter: | 7/12/20 mm |
Adjustable sample pressure: | up to 1000 mN |
Measuring range: | 500 / 5000 µm |
Resolution: | 0,125 nm |
Options: | Pressure controllable Gas Mixing System (MFC´s) |
Atmosphere: | inert, oxid.*, red., vac. |
*Specifications depend on the configurations |
MODEL | DIL L75 HP/2 (DIL HP L70)* |
---|---|
Temperature range: | RT bis 1400/1800°C |
Max. pressure: | max. 100 bar |
Vacuum: | 10E-4 mbar |
Sample holder: | fused silicia < 1100°C, Al2O3 < 1750°C |
Max. sample length: | 50 mm |
Sample diameter: | 7/12/20 mm |
Adjustable sample pressure: | up to 1000 mN |
Measuring range: | 500 / 5000 µm |
Resolution: | 0,125 nm |
Options: | Pressure controllable Gas Mixing System (MFC´s) |
Atmosphere: | inert, oxid.*, red., vac. |
*Specifications depend on the configurations |
Furnaces and accessories
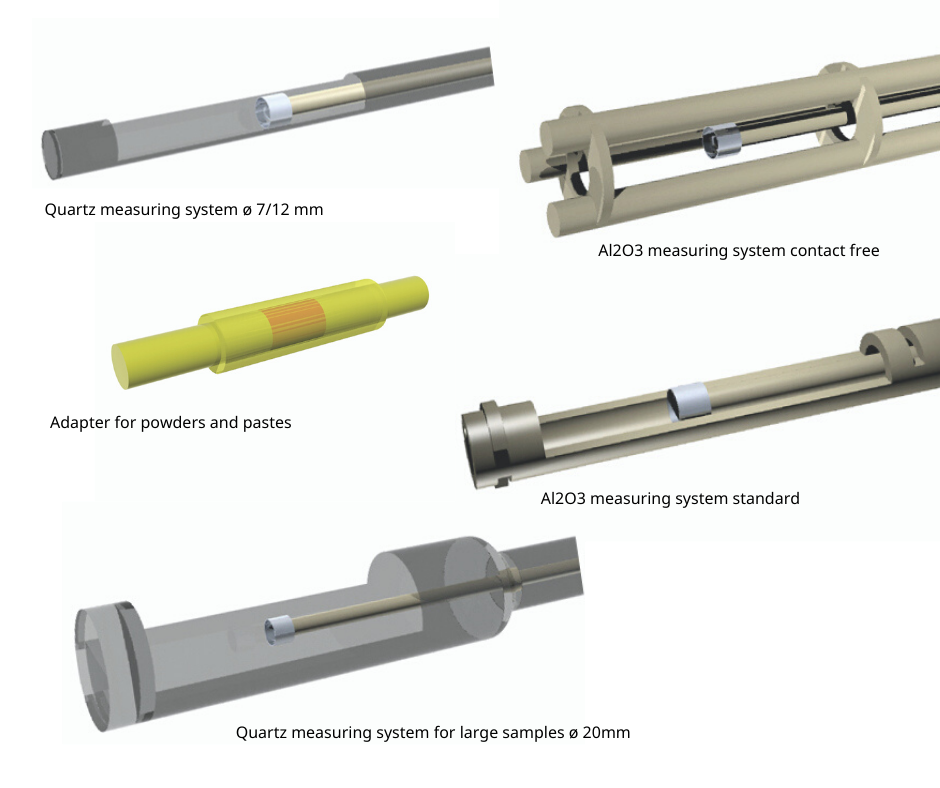
- Devices for sample preparation
- Various specimen holders (size, material)
- Caliper for manual or online input of sample length
- Various gas boxes: manual, semi-automatic and MFC controlled
- Rate-controlled sintering (RCS) software option
- Various rotary and turbomolecular pumps
- Possibility of operation under 100% H2
- LN2 cooling
- Choice of different dilatometer measuring systems
Software
Making values visible and comparable
The powerful LINSEIS thermal analysis software, which is based on Microsoft® Windows®, performs the most important function in the preparation, execution and evaluation of thermoanalytical experiments, in addition to the hardware used. With this software package, Linseis offers a comprehensive solution for programming all device-specific settings and control functions, as well as for data storage and evaluation. The package was developed by our in-house software specialists and application experts and has been tested and used over many years.
Dilatometer functions
- Glass transition and softening point determination
- Automatic softening point switch-off, freely adjustable (system protection)
- Display of absolute or relative shrinkage or expansion
- Display and calculation of technical / physical expansion coefficients
- Rate-controlled sintering (software option)
- Sintering process evaluation
- Density determination
- Automatic evaluation routines
- System correction (temperature, zero curve, etc.)
- Automatic zero point adjustment
- Automatic punch contact pressure control
General functions
- Automatic and manual scaling
- Display of axes freely selectable (e.g. temperature (x-axis) versus delta L (y-axis))
- Mathematical calculations (e.g. first and second derivative)
- Storage of complete evaluations
- Multitasking function
- Multi-user function
- Zoom option for different curve sections
- Any number of curves can be loaded on top of each other for comparison
- Online help menu
- Free labeling
- EXCEL® and ASCII export of measurement data
- Data smoothing
- Zero curves are calculated
- Cursor function
- Statistical curve evaluation (mean value curve with confidence interval)
- Tabular printout of data and expansion coefficients
- Calculation of Alpha Phys, Alpha Tech, relative expansion L/L0
- Curve arithmetic, addition, subtraction, multiplication
Applications
Application example: Zirconia ceramic – Thermal expansion / RCS / sintering
In production processes of high-tech ceramics, a simulation of sinter processes is of high interest. It is very important to know the ideal sinter rate and -temperature. Besides simulation, measurement and experimental optimization of sinter conditions is a frequently used technique. When using the optional software package RCS (Rate Controlled Sintering) it is possible to program controlled sintering with a dilatometer as per PALMOUR III theory. The following application shows the sintering process of ZrO2 green body, a typical ceramic raw material.
In this experiment, the sinter rate was defined by RCS software and was programmed to be kept constant. The red curve shows the temperature of the sample and therefore the heating rate. The blue and green curves show the change of length, the purple curve is the derivative of the length change. The sample was heated linear in a L75 horizontal dilatometer. After 50 min, the sinter process started at around 900°C. The RCS software increased the heating rate to obtain a linear sintering until the sinter rate lowered significantly at around 60 min. The software then lowers the heating rate and the sample length finally reached a plateau at around 180 min where the final density of the now burned ZrO2 given.
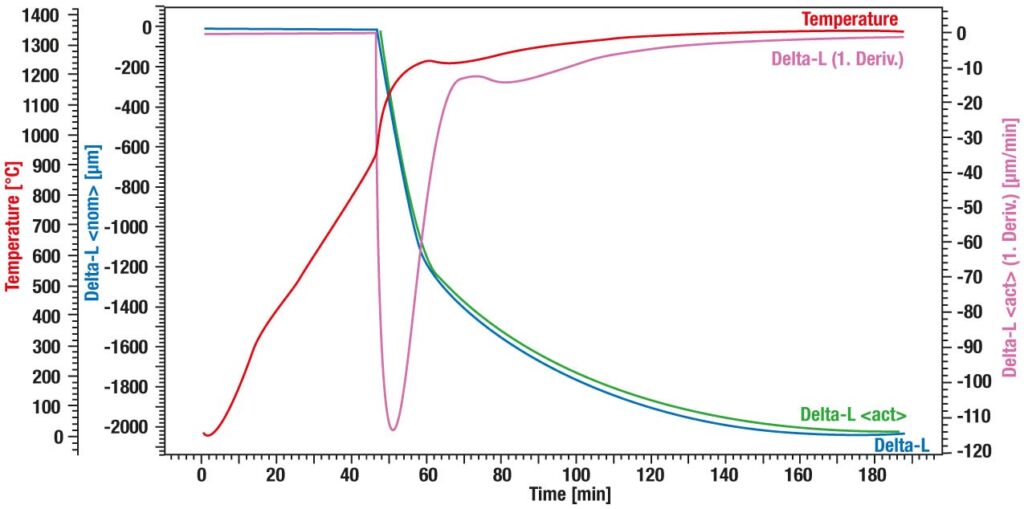
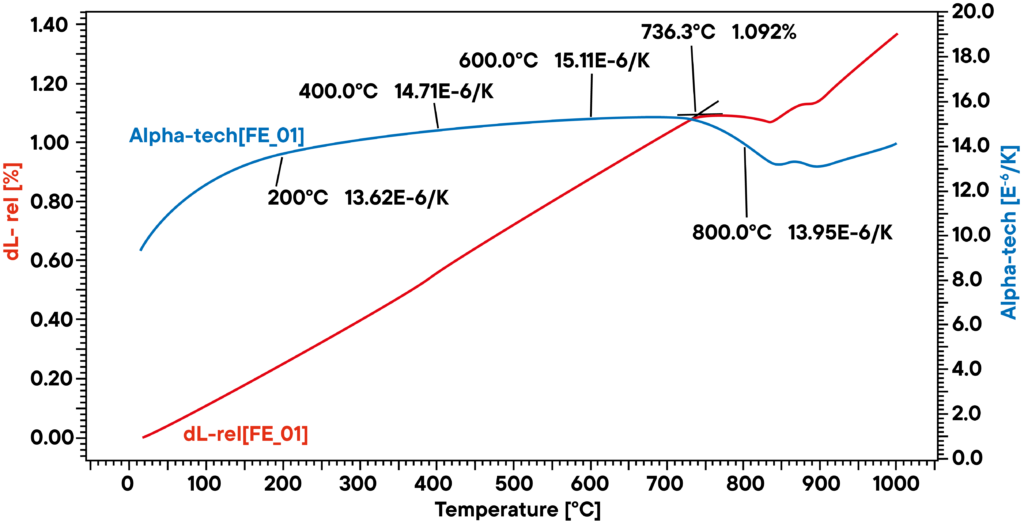
Application example: Pure Iron – Thermal expansion / curie point
Iron is one of the most used construction materials one of the most existing metals in the world. All steels are mainly consisting of iron which means most vehicles and buildings are more or less made of iron. The mechanical properties of iron are what makes it an ideal material for all these purposes. It is considerable hard, stable, easy to handle and can be forged in open fire. Most steels contain various other metals and carbon in different amounts, providing many properties like color, hardness grade, chemical resistance and many more. Naturally, iron is one of the best-known materials and analysis of iron and steels is more or less one of the most frequent applications in thermal analysis.
This measurement illustrates the linear thermal expansion (rel. ΔL – red curve) and the coefficient of thermal expansion CTE (blue curve) of the iron sample under argon atmosphere. The heating rate was 5 K/min. Above 736.3°C (maximum of CTE) shrinkage is detected, which is due to a phase change effect, also known as the Curie-point. The difference of measured and literature value can be attributed to contamination of the sample and small traces of other elements that were contained.