Description
To the point
The Linseis LSR platform can be used to characterize thermoelectric materials almost completely, both in the form of solid materials and thin films.
In the basic LSR-3 (LSR L31) version, both the Seebeck coefficient and the electrical conductivity (electrical resistance) of solid materials can be measured fully automatically and simultaneously up to a maximum temperature of 1500°C.
The basic version can be combined with various options to extend the range of applications.
For example, the low temperature option allows fully automatic measurement using LN2 cooling down to -100°C and the use of a special thin film adapter for measuring films and thin layers.
An optional camera allows the determination of electrical conductivity with the highest accuracy and the use of the high-resistance option significantly extends the measuring range in order to characterize samples with poor electrical conductivity.
As the thermal conductivity is required in addition to the Seebeck coefficient and the electrical conductivity in order to calculate the dimensionless figure of merit ZT, it is usually necessary to use another measuring device, such as a LaserFlash, to determine it.
To solve this problem, either an additional LaserFlash can be integrated into the Linseis LSR platform (see LZT meter) or a special adapter can be used, which allows the measurement of solid materials using the Harman method.
This is a direct ZT determination which, in combination with the two original measurements, allows conclusions to be drawn about the thermal conductivity.
An LSR platform with integrated Harman method is referred to as LSR-4 due to its significant added value.
By means of an optional extension of the measuring electronics, the ZT value for modules (TEG) can also be determined in the LSR-4 platform using the same measuring principle in the form of impedance spectroscopy.
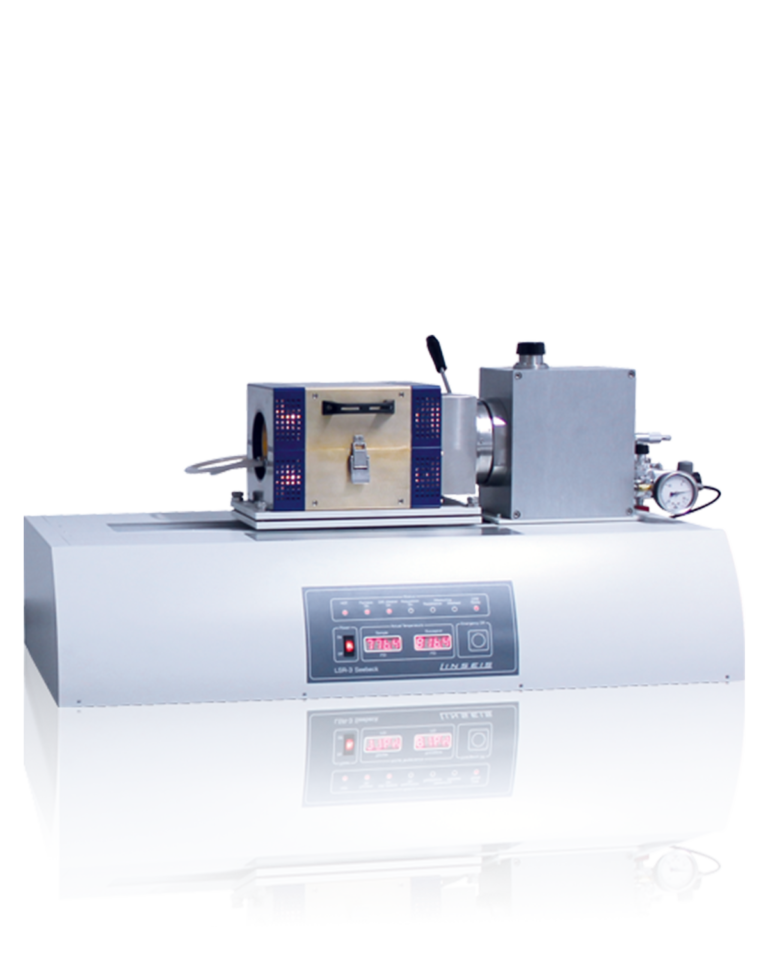
Principle of Seebeck-Coefficient measurement
A cylindrical, square or rectangular sample is positioned vertically between two electrodes.
The lower electrode block and optionally also the upper electrode block (to invert the temperature gradient) contain a heating coil (secondary heater).
The entire measuring arrangement is located in an oven, which heats the sample to a specific temperature for the measurement.
When this temperature is reached, the secondary heater in the lower electrode generates a predefined temperature gradient along the sample.
Two laterally contacting thermocouples T1 and T2 now measure the temperature difference (ΔT = T2 – T1) between the hot and cold contact on the sample.
In addition, one of the two thermocouple leads is used to measure the electromotive force dE (or thermoelectric voltage Vth).
A unique spring mechanism enables the best possible electrical contact between the thermocouples and the probe and therefore highly accurate measurements.
The Seebeck coefficient can then be easily calculated from the measurement data obtained using the following formula:
Measuring principle electrical conductivity
A DC four-wire measurement is used to determine the specific electrical resistance or electrical conductivity of the samples.
This allows parasitic influences such as contact or wire resistance to be suppressed and measurement accuracy to be significantly increased.
For the measurement in thermal equilibrium (ΔT = 0K), a constant direct current (IDC) is impressed into the sample using the two electrodes.
Due to the electrodes and sample dimensions, an almost ideal one-dimensional current flow within the sample can be assumed.
The resulting voltage drop (VΩ) over a section of the length “t” of the sample is measured again using one of the two thermocouple wires.
The specific resistance and electrical conductivity can be calculated using the following formulas based on the measurement data and the thermocouple spacing “t”.
Principle of a Harman measurement
The Harman method makes it possible to calculate the thermoelectric figure of merit ZT of a material from the measurement of the temporal voltage curve of a sample when direct current (DC) is applied.
For the measurement, a current is impressed into a thermoelectric sample via two needle contacts.
Due to the Peltier effect, one of the two junctions is heated or cooled locally.
As a result, the adiabatic boundary conditions produce a characteristic temperature profile over the sample.
If the ratio is formed from the measurement of the initial voltage drop (ohmic part without temperature gradient) and the measurement of the stationary voltage drop (including thermoelectric voltage), the dimensionless figure of merit ZT (and from this also the thermal conductivity lambda) can be calculated.
The fundamental advantages of the Harman method compared to calculating ZT from individual measurements are that only a single measuring device is required, only a single sample needs to be prepared and the resulting measurement error for ZT is significantly smaller due to the direct measurement.
The disadvantage, however, is that the measurement method can only be used for good thermoelectric materials and up to a maximum of 400°C.
Adapter for thin films and foils
Due to their unique properties compared to solid materials, interest in nanostructured samples, such as thin films or nanowires, has increased significantly in recent years.
To meet the requirements of today’s research, LINSEIS has developed two different sample holders for free-standing films and foils or coatings on a substrate for the LSR platform.
Thanks to the unique design of the sample holders, a variety of differently prepared samples can be characterized with the LSR in terms of coating thickness and manufacturing method.
Available accessories
Sample holder for disk shaped samples
Thermoelements and Camera-Option
Standard thermocouples: for maximum precision
Jacketed thermocouples: for demanding samples
Type K/S/C thermocouples:
- Type K for low temperature measurements
- Type S for high temperature measurements
- Type C for all samples that react with platinum
Camera option
- Camera option for probe distance measurements
- enables high-precision resistance measurements
- including software package
Unique features
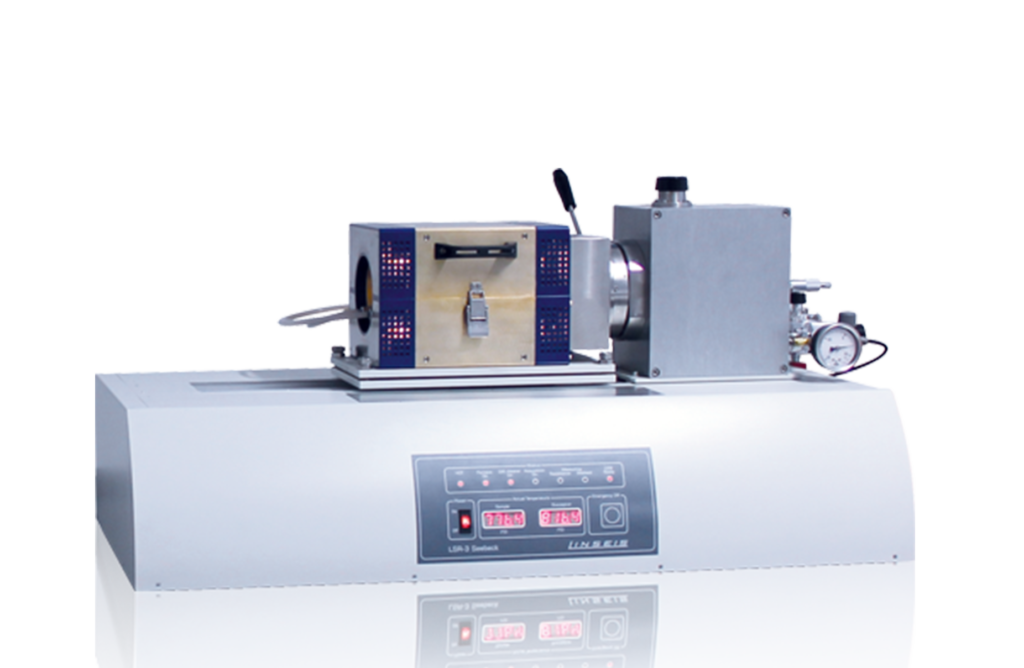
Measurements in the temperature
range from -100°C to 1500°C using
interchangeable ovens
Direct ZT measurement using the Harman
method and impedance spectroscopy
High-speed infrared oven
for excellent temperature
control and higher sample
throughput
Large selection of thermocouples and camera
option for precise resistance measurements
Questions? We're just a call away!
+1 (609) 223 2070
+49 (0) 9287/880 0
Our service is available Monday to
Thursday from 8 am to 4 pm
and Friday from 8 am to 12 pm.
We are here for you!
Specifications
Hard Facts
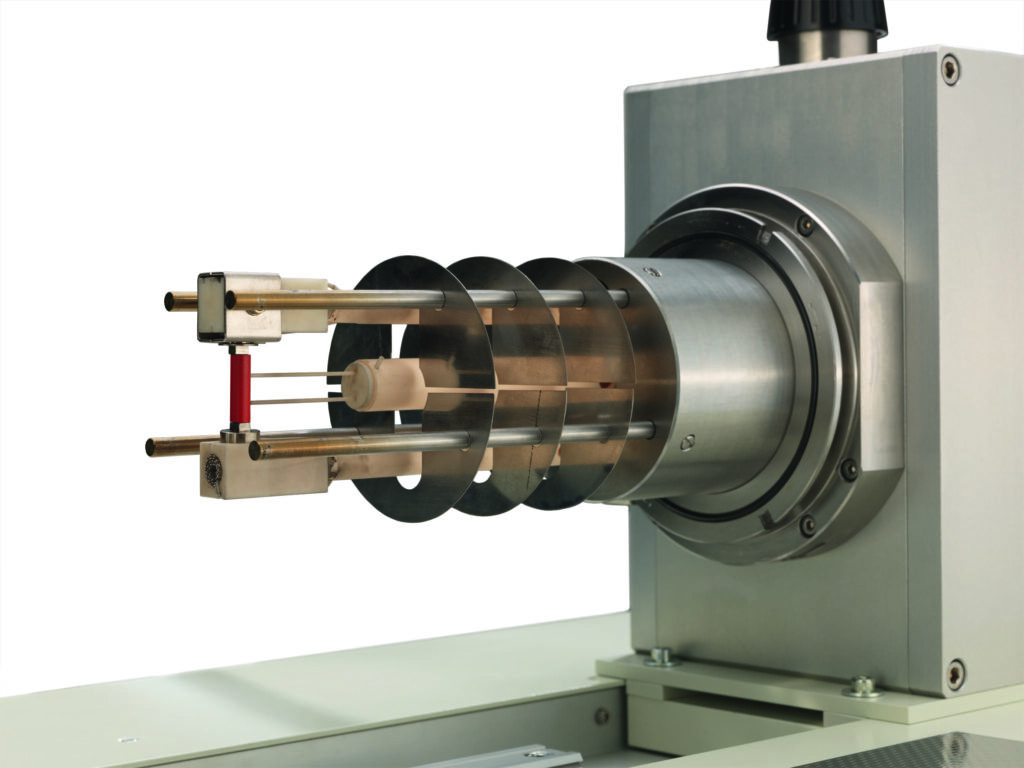
Special features
- Almost ideal, 1-dimensional heat flow through the sample
- High-ohm option and variably positionable thermocouples, even the most demanding samples can be reliably measured.
- Measurements in the temperature range from -100°C to 1500°C are possible using interchangeable furnaces
- Direct ZT measurement on legs (Harman method) and modules (impedance spectroscopy)
- Thermal conductivity measurement using the Harman method
- High-speed infrared oven for excellent temperature control during measurement and higher sample throughput
- Large selection of available thermocouples (temperature range, sheathed, free-standing)
- Camera option for high-precision resistivity measurements
MODEL | LSR-3 (LSR L31) |
---|---|
Temperature range: | Infrared oven: RT up to 800°C/1100°C Resistance oven: RT up to 1500°C Low temperature oven: -100°C to 500°C |
Measurement method: | Seebeck coefficient: Static DC method / Slope method Electrical resistance: four-point measurement |
Atmosphere: | Inert, reducing, oxidizing, vacuum Helium gas with low pressure recommended |
Sample holder: | Vertical clamping between two electrodes Optional adapter for films and thin layers |
Sample size (cylinder or rectangle): | 2 to 5 mm base area and max. 23 mm long up to a diameter of 6 mm and a length of max. 23 mm long |
Sample size round (disc shape): | 10, 12.7, 25.4 mm |
Measuring distance of the thermocouples: | 4, 6, 8 mm |
Water cooling: | required |
Measuring range Seebeck coefficient: | 1µV/K to 5000 µV/K (static direct current method) Accuracy ±7% / repeatability ±3.5% |
Measuring range Electrical conductivity: | 0.01 to 2×10 5 S/cm Accuracy ±10% / repeatability ±5% |
Current source: | Low drift current source from 0 to 160 mA (optional 220 mA) |
Electrode material: | Nickel (-100 to 500°C) / Platinum (-100 to +1500°C) |
Thermocouples: | Type K/S/C |
* 5% for LSR including camera option |
Addon | LSR-4 Upgrade |
DC Harman method: | Direct ZT measurement on thermoelectric legs |
AC impedance spectroscopy: | Direct ZT measurement on thermoelectric modules (TEG/Peltier module) |
Temperature range: | -100 to +400°C RT to +400°C |
Sample holder: | Needle contacts for adiabatic measuring conditions |
Sample size: | 2 to 5 mm in rectangle and max. 23 mm long up to 6 mm in diameter and max. 23 mm long Modules up to 50mm x 50mm |
Data sheet
Software
Making values visible and comparable
The powerful LINSEIS thermal analysis software, which is based on Microsoft® Windows®, performs the most important function in the preparation, execution and evaluation of thermoanalytical experiments, in addition to the hardware used.
With this software package, Linseis offers a comprehensive solution for programming all device-specific settings and control functions, as well as for data storage and evaluation.
The package was developed by our in-house software specialists and application experts and has been tried and tested over many years.
General properties
- Automatic evaluation of the Seebeck coefficient and electrical conductivity
- Automatic control of sample contacting
- Create automatic measurement programs
- Creating temperature profiles and temperature gradients for the Seebeck measurement
- Automatic evaluation of Harman measurements (optional)
- Real-time color display
- Automatic and manual scaling
- Display of the axes freely selectable (e.g. temperature
e.g. temperature (x-axis) against delta L (y-axis)) - Mathematical calculations (e.g. first and second derivatives)
- Database for archiving all measurements and evaluations
- Multitasking (different programs can be used at the same time)
- Multi-user option (user accounts)
- Zoom options for curve sections
- Any number of curves can be loaded on top of each other for comparison
- Online Help Menu
- Free labeling of the curves
- Simplified export functions (CTRL C)
- EXCEL® and ASCII export of measurement data
- Zero curves can be calculated
- Statistical curve evaluation (mean value curve with confidence interval)
- Tabular printout of the data
Applications
Application example: Constantan (high temperature reference)
In contrast to the Bi2Te3 reference sample (SRM 3451)™ provided by NIST, which can only be used in a limited temperature range up to 390K, our alternative constantan reference sample can be used as a high temperature reference up to 800°C.
The following measurement shows a typical curve, which is well within the specified tolerances.
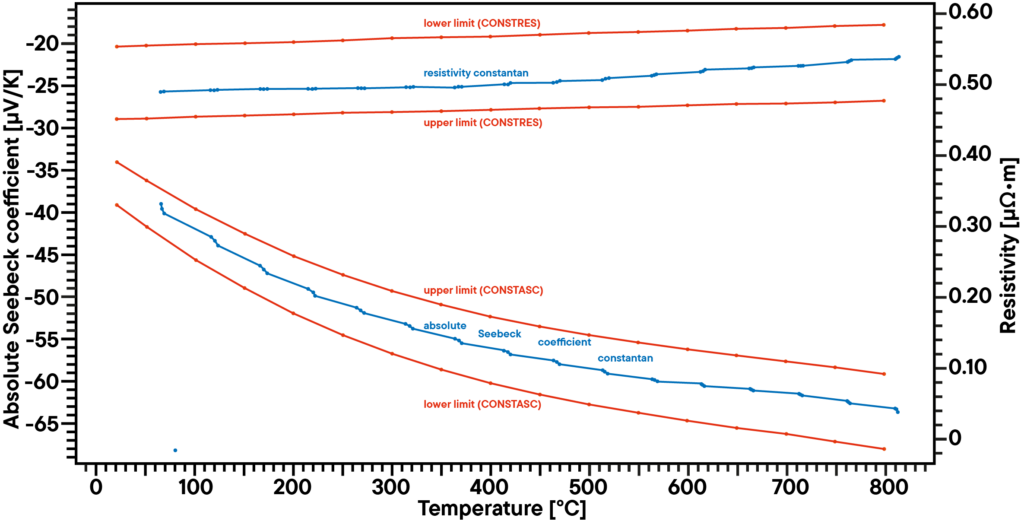
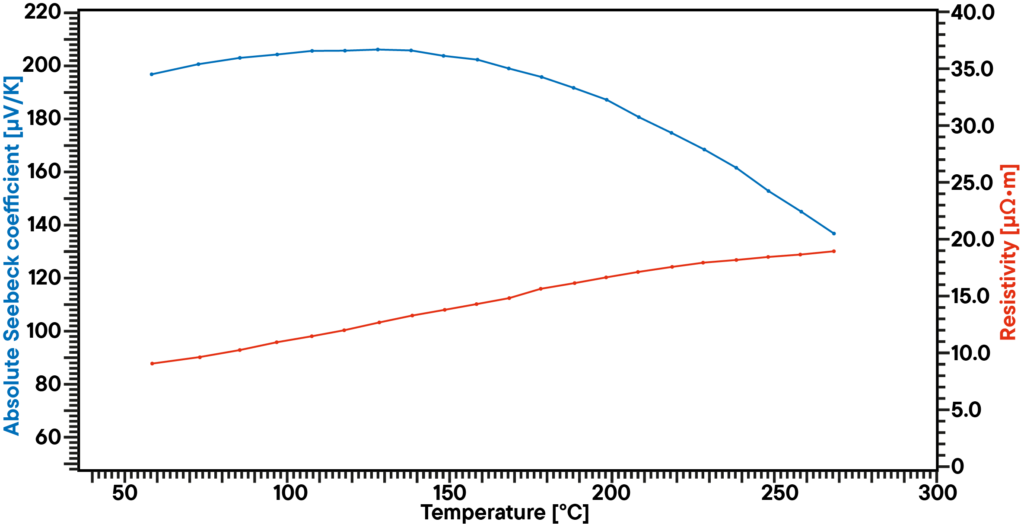
Application example: SiGe alloy
Silicon-germanium alloys are high-temperature stable thermoelectric materials that are usually used under the most demanding environmental conditions, such as in space missions or at high temperatures in energy recovery from waste heat.
However, the following measurement was carried out to test the low-temperature behavior of a newly developed alloy.
Application example: ZT measurement of the NIST Bi2Te3 reference (Harman method)
The following figure shows the measurement of the NIST (SRM 3451)™ Bi2Te3 reference sample, measured using the Harman method for a direct ZT measurement in our LINSEIS LSR platform.
The NIST (SRM 3451)™ Bi2Te3 Bismuth telluride reference material has been analyzed using the Harman method in combination with our LINSEIS LSR platform. The measurement clearly shows the typical voltage distribution at a single temperature measurement point. In this case, the ZT “figure of merit” value at room temperature can be simply calculated by setting the ohmic voltage drop and the thermoelectric voltage drop in relation. ZT was found to be 0.50 at room temperature.
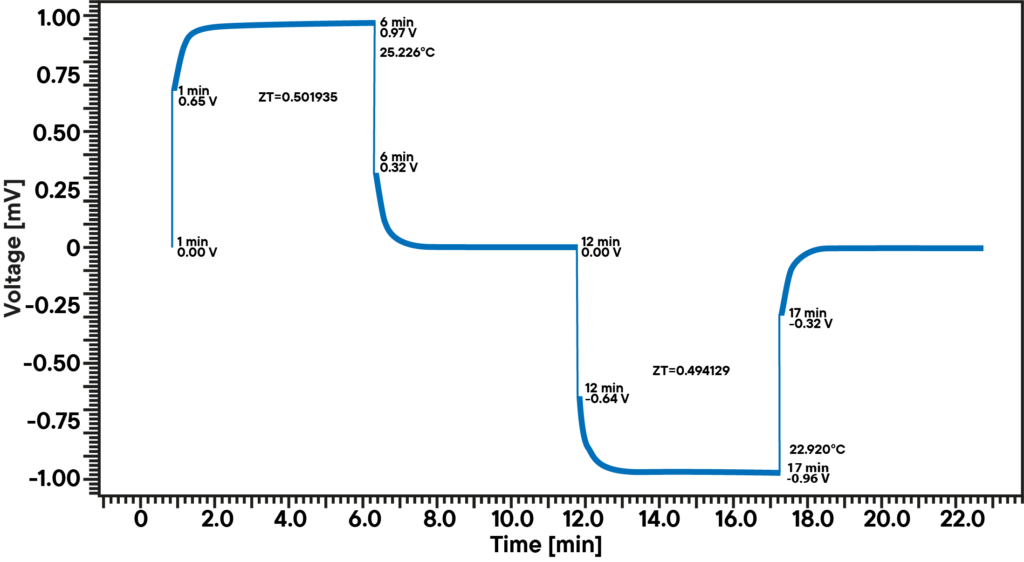
Well informed