FDTR - Frequency-Domain Thermoreflectance
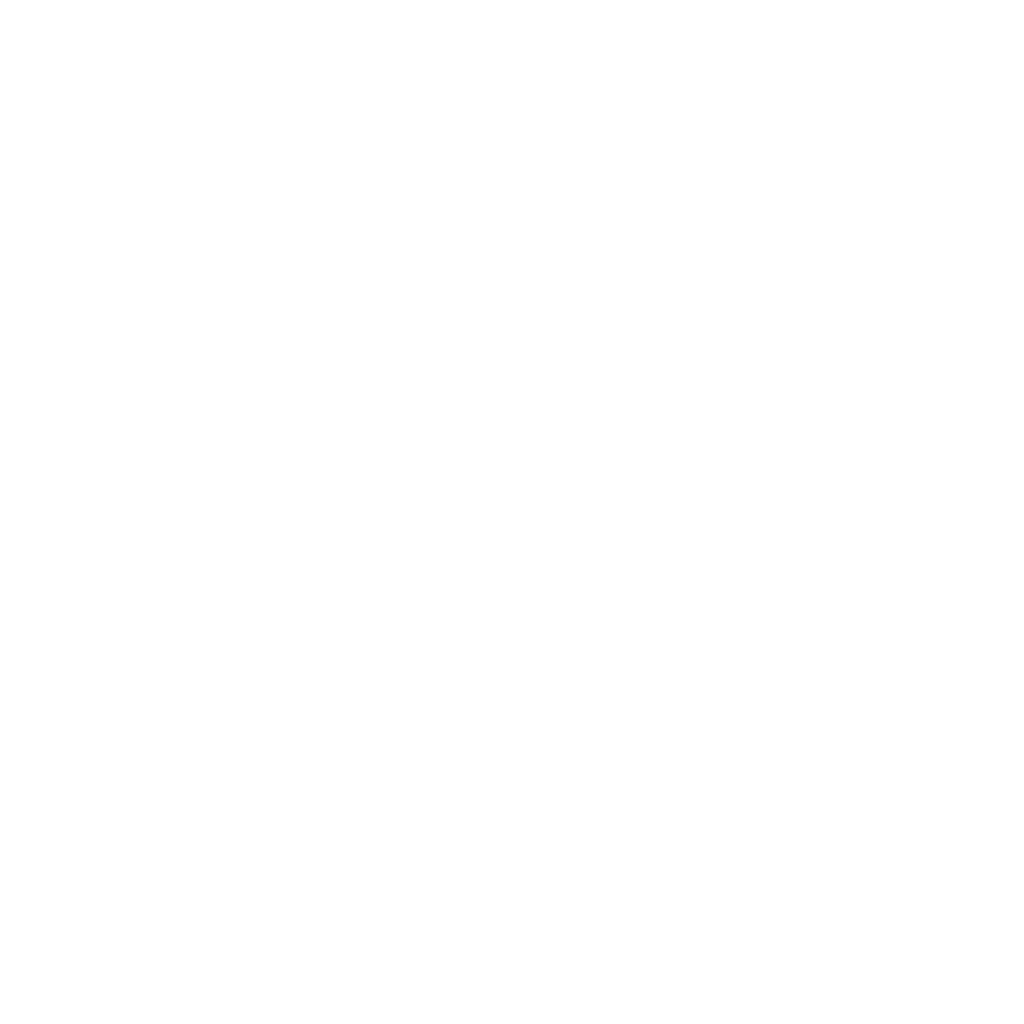
Understanding Frequency-Domain Thermoreflectance (FDTR) for Thin Film Characterization
The study of thermophysical properties and heat transfer optimization has become essential for modern industrial applications. Over the years, various methods have been developed to assess the thermal properties of materials, with the flash method emerging as one of the most common techniques. However, as industries increasingly rely on thin films for specialized applications, where the laser flash method tend to reach their limit soon.
Nevertheless, our Periodic Laser Heating technique finds you here in favor, but when the layers become thinner and thinner and cannot stand free a method with a multi-layer algorithm for nm thick thin films more sophisticated methods like Frequency-Domain Thermoreflectance (FDTR) are being utilized to meet the demand for accurate thermal characterization.
The Growing Importance of Thin Films
Thin films, which range from a few nanometers (nm) to micrometers (μm) in thickness, are critical in industries such as semiconductor manufacturing, LED technology, and thermoelectric materials. These films are typically deposited on a substrate to provide specific functionalities. Since their thermal properties differ significantly from bulk materials, accurate thermal management requires precise data on their thermophysical properties, such as thermal conductivity, thermal diffusivity, and thermal interface conductance.
What is Frequency-Domain Thermoreflectance (FDTR)?
Frequency-Domain Thermoreflectance (FDTR) is an advanced, non-contact technique used to measure the thermal properties of thin films in the frequency domain. It is especially useful for characterizing materials with complex thermal behaviors, such as those used in microelectronics, semiconductors, and thermal barrier coatings. FDTR leverages the thermoreflectance effect, where a material’s reflectivity changes as its surface temperature varies. This change in reflectivity is monitored to deduce thermal properties such as thermal conductivity and thermal diffusivity.
FDTR is a contactless technique used to characterize the thermal properties of thin films in the frequency domain. The core principle of FDTR is based on the thermoreflectance effect, which allows researchers to detect changes in a material’s reflectivity as it is heated. This method involves the use of two lasers: a pump laser that heats the material and a probe laser that monitors the surface temperature by measuring reflectivity changes.
The central concept of FDTR is the modulation of a material’s surface temperature using a harmonically modulated laser (the pump) and detecting the thermal response using a second laser (the probe). This process is carried out without physical contact, making it ideal for fragile or sensitive samples. The thermal excitation of the sample and the subsequent measurement of its surface response are conducted in the frequency domain, where the analysis focuses on the time lag or more precisely the phase lag, between the periodic heating and the material’s thermal response.
The light sources are a:
- Pump Laser: This is a continuous wave laser, often with a wavelength around 405 nm, which serves to heat the sample. The pump laser’s intensity is modulated sinusoidally at varying frequencies to introduce periodic heating into the material. By adjusting the modulation frequency can different thermal transport lengths can be probed, allowing researchers to analyze heat diffusion at distinct depths within the material.
- Probe Laser: The probe laser, usually at 532 nm, monitors the temperature of the sample’s surface by measuring changes in reflectivity that occur due to the heating caused by the pump laser. This reflectivity change is directly related to the temperature of the sample, as materials generally exhibit a temperature-dependent reflectance. The probe laser’s signal is carefully analyzed to measure the phase shift between the thermal excitation from the pump laser and the reflectivity change, which is detected using a lock-in amplifier.
Lock-In Amplifier and Phase Measurement
The lock-in amplifier plays a crucial role in FDTR. It extracts the phase information between the pump laser’s heating cycle and the probe laser’s reflectivity signal.
By measuring this phase lag, which is the delay between when the sample is heated and when the reflectivity changes in response, researchers can gain precise information about how heat propagates through the material.
The phase lag is sensitive to the material’s thermal properties, and it varies with the modulation frequency of the pump laser, making FDTR a frequency-domain method.
Role of the Metallic Transducer
To enhance the measurement sensitivity, a thin metallic transducer layer, commonly made of gold or aluminum, is deposited on the surface of the sample. This layer serves two primary purposes:
- Increased Temperature Sensitivity: Metals like gold have a high temperature coefficient of reflectance (dR/dT), meaning their reflectivity changes significantly with temperature. This amplifies the detectable signal, improving the accuracy of the thermal measurement.
- Control of Optical Penetration Depth: The transducer layer limits the optical penetration depth of the laser into the material, ensuring that the reflectivity change is measured predominantly from the surface. This makes the data more representative of the thermal properties of thin films or near-surface layers, as opposed to deeper regions of the material.
Frequency Dependence and Thermal Property Extraction
By varying the modulation frequency of the pump laser, FDTR can probe different thermal transport regimes. At high frequencies, the thermal diffusion length is short, so the measured heat transfer is confined to near the surface of the sample.
At low frequencies, the heat diffuses deeper into the material, allowing for a more comprehensive analysis of the bulk thermal properties. By fitting the phase lag data to thermal models, it is possible to extract parameters such as:
Where:
- μ is the thermal penetration depth
- α is the thermal diffusivity of the material
- ω is the modulation frequency of the pump laser.
– Thermal Conductivity: How well the material conducts heat.
– Thermal Diffusivity: How quickly heat spreads through the material.
– Interface Thermal Conductance: The thermal resistance at the boundary between different layers or materials.
Thermal penetration depth whole sample
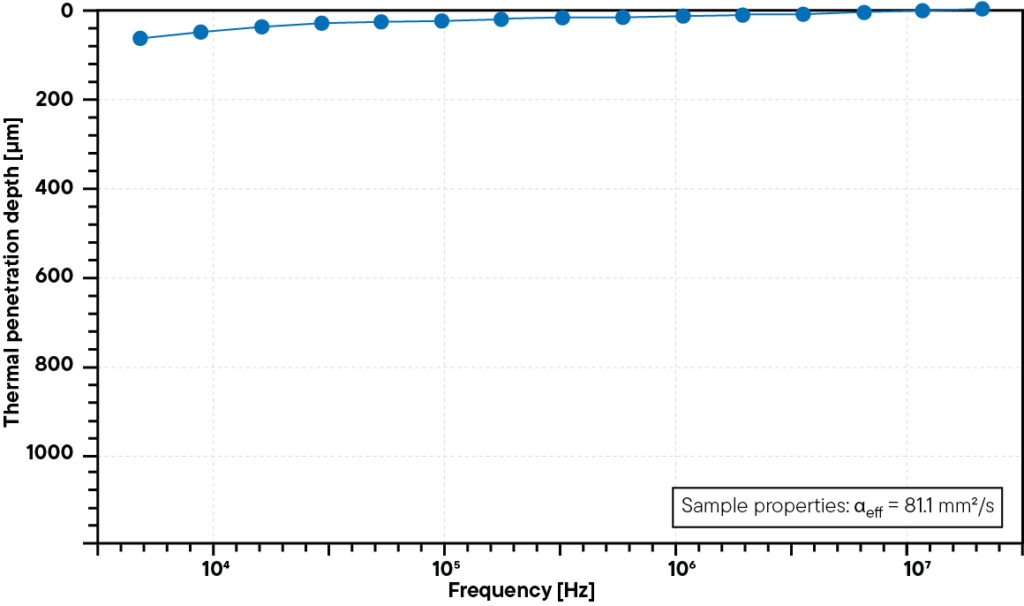
Thermal penetration depth detail view on the surface
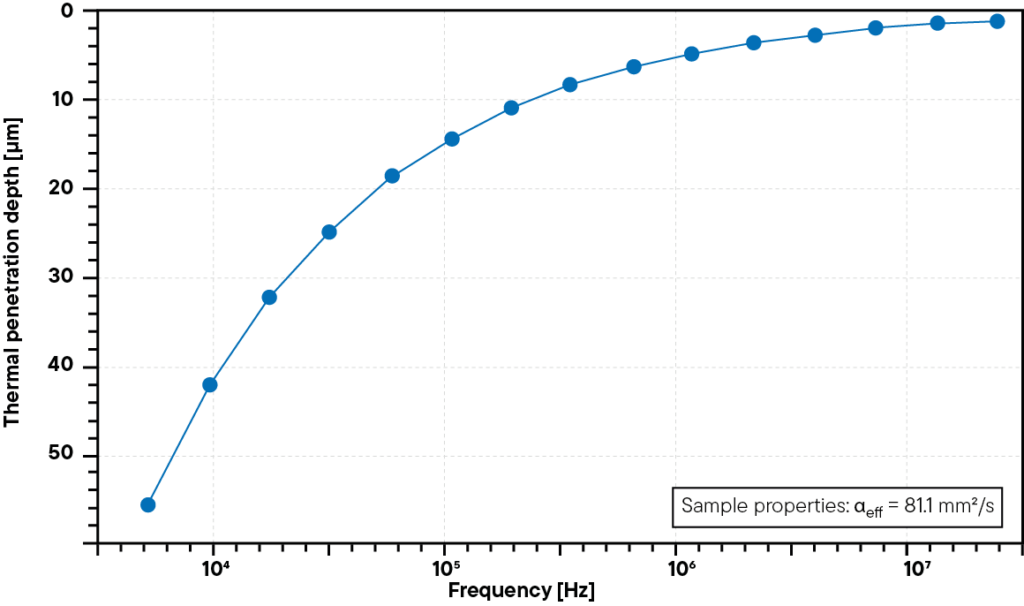
Advantages of FDTR over Time-Domain Thermoreflectance (TDTR)
While Time-Domain Thermoreflectance (TDTR) shares similar principles with FDTR (both pump probe laser experiments, can yield the same results, etc.), FDTR offers several advantages, making it the superior method for many applications:
- Simplified Sample Setup: In TDTR, the pump and probe lasers are not initially co-aligned, which necessitates constant adjustments to account for changes in the sample’s reflection. In contrast, our FDTR system both lasers are perfectly aligned, eliminating the need for frequent adjustments and streamlining the sample setup and enhancing the usability.
- Stable Measurements: In TDTR, slight changes in reflection when altering the sample require recalibration of the probe laser, which can complicate the process. FDTR avoids this issue, providing consistent and reliable data without the need for constant fine-tuning. The stability of the measurement process is enhanced due to the fact that the lasers remain aligned in FDTR. This reduces the probability of errors occurring as a result of minor variations in laser positioning or sample orientation.
- Broader measuring range: Our FDTR outperforms even nano-pulsed TDTR setups with a broader measuring range. Thinner samples layers and thin films with higher thermal conductivity can be measured.
- No need for assumptions: Our comprehensive evaluation algorithm allows you to measure thin films without any assumptions. All you need to know is the sample thickness.
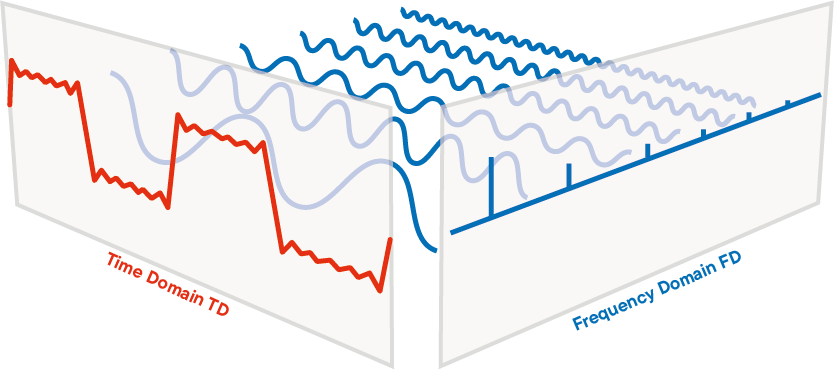
Applications of FDTR
Overall, thin film thermal conductivity has a wide range of applications in many fields, and ongoing research in this area is critical for the development of new and improved materials and devices for various applications. Such as Semiconductors, thermoelectric devices, Microelectronics, Energy conversion and storage, Aerospace, Biomedical devices or optical coatings.
- Semiconductory industry: During the manufacturing process, heat is generated as a result of various fabrication steps, and it is important to dissipate this heat to prevent damage to the devices being manufactured. Materials with high thermal conductivity, such as silicon and diamond, are used in various stages of the manufacturing process to help dissipate heat and maintain device quality.
- Thermoelectric devices: The thermal conductivity of the low-conductivity material is a critical factor in determining the efficiency of thermoelectric devices. This is because a low thermal conductivity material reduces the amount of heat that is transferred across the device, which enhances the temperature difference and improves the efficiency of the device. Conversely, a high thermal conductivity material would allow more heat to be transferred across the device, which would reduce the temperature difference and decrease the efficiency of the device. In addition, the thermal conductivity of the thermoelectric materials also affects the maximum operating temperature of the device. High thermal conductivity can cause the materials to heat up quickly, leading to thermal runaway and device failure.
- Microelectronics: Thin film thermal conductivity is important for improving the thermal management of microelectronic devices. In this field, thin films are used as heat spreaders and thermal interface materials, helping to dissipate heat from hot spots on a microchip.
- Energy conversion and storage: Thin films are used in various energy conversion and storage devices, including solar cells, thermoelectric generators, and batteries. In these applications, the thermal conductivity of the thin films affects the efficiency of the device.
- Aerospace: Thin film thermal conductivity is critical in aerospace applications, where lightweight and efficient thermal management is required. Thin film coatings are used on spacecraft components, such as heat shields and thermal insulation.
- Optoelectronics: Optoelectronics is a branch of electronics that deals with the study of the interaction between light and electronic devices. It involves the use of semiconductor materials to convert light into electrical signals or vice versa. Optoelectronic devices include light-emitting diodes (LEDs), photodiodes, solar cells, and optocouplers. LEDs are semiconductor devices that emit light when a current is passed through them, while photodiodes are semiconductor devices that produce an electrical current when exposed to light. Solar cells are optoelectronic devices that convert sunlight into electrical energy. Optocouplers are used to transfer signals between circuits that are electrically isolated from each other.
Application example: CVD Diamond – Thermal conductivity
Measurement of the thermal properties of CVD diamond. The x-axis displays the logarithmically scaled frequency in Hertz, while the y-axis represents the phase shift between the excitation by the pump laser and the probe laser. Where 𝝀 is the thermal conductivity, 𝜶 is the thermal diffusivity, e is the thermal effusivity and TBC is the thermal boundary conductance between the transducer layer (gold) and the sample (diamond). It determines how well a combination of materials is able to exchange heat with each other.
Conclusion
As the demand for high-performance thin films continues to grow across various industries, FDTR has emerged as a leading method for accurately characterizing their thermal properties. Its contactless nature, simplified setup, and superior stability make it the preferred choice over traditional methods like TDTR. By leveraging advanced laser systems and the principles of thermoreflectance, FDTR enables precise thermal measurements, which is critical for the development of cutting-edge technologies. In a world where accurate thermal predictions can make or break the performance of advanced materials, FDTR offers the insights needed to push industrial applications forward.
FDTR’s non-destructive nature, high sensitivity, and capability to operate over a wide range make it a powerful tool in the field of thermal metrology. It provides a detailed understanding of how heat moves through materials, which is crucial for optimizing thermal management in various industries, including electronics, energy, and materials science.