Description
To the point
The gas safety system works automatically and supports you when working with hydrogen and other flammable or toxic gases. The sensors of the system detect leaks and can automatically purge the instrument.
The gas safety system is mainly used by our customers in thermobalances and dilatometers.
The system can be adjusted to different gases. We take these into account in the production of our system. On request it is also possible to use the system for other Linseis measuring instruments.
Unique Features
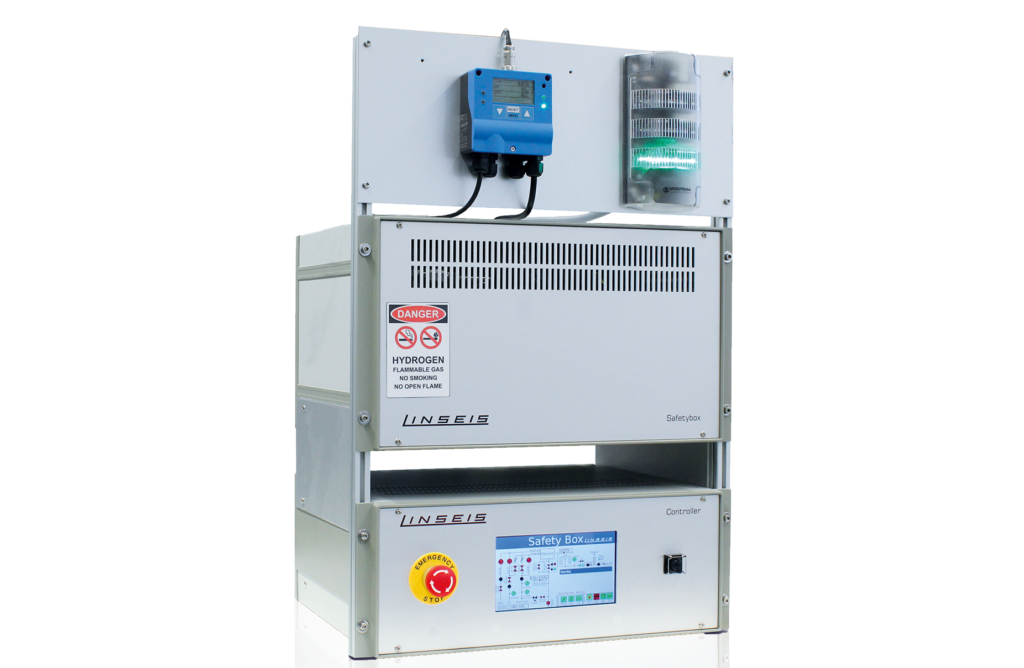
Automated gas atmosphere:
Fully automated preparation
including evacuation and purging.
Safety in the event of gas leaks:
sensors detect leaks and the
system flushes automatically.
Combustible and toxic gas monitoring:
Works with combustible and toxic gases
such as H2, CH4, CO, and CL2.
Independent operation:
Can react autonomously
without PC communication.
Emergency functions:
Integrated non-return valve
and UPS for automatic flushing
in the event of a power failure.
Questions? We're just a call away!
+1 (609) 223 2070
+49 (0) 9287/880 0
Our service is available Monday to
Thursday from 8-16 o’clock
and Friday from 8-12 o’clock.
We are here for you
How the system works
- Sensors are also placed aorund and above the device to detect possible leaks
- Sensors can be prepared for different gases (H2, CH4, CO, CL2 and others)
1. Prepare measurement
When switching on the safety system, first it will check wether the communication to the AD converter is working.
All analog values are additionally checked via comparators. The burn off unit is turned on in case the gas room monitor reports a safe condition.
2. Insert the sample
The safety device is now in standby mode. The furnace lift is now released for opening. When the sample is inserted the gas cycle can be started. The chamber will be purged. The operating pressure switch and relative pressure sensor are checked again. The vacuum pump is now vented. The chamber is first evacuated via the vacuum bypass with the backing pump.
3. System will be automatically purged in the event of:
- an empty gas cylinder
- an empty N2 cylinder (if the pressure drops below 4 bar threshold)
- one burner failing
- power outage
- furnace cooled down too quickly and there was no longer sufficient overpressure in the chamber
The chamber is then purged with inert gas for 3 minutes (this corresponds to approximately 10 times the chamber volume).
Functions at a glance
- completely automated preparation of gas atmosphere including evacuation
- purge gas inlet pressure is monitored if gas runs low – chamber will be fully purged before the gas runs out
- system comes with a UPS for automatically purging the system in case of a power outage
- integrated burn-off unit with two independent igniters (only for flammable gases) and electrical current monitoring
- flashback arrestor valve integrated into outlet path
- vacuum level is monitored trough two independent sensors during pumping to ensure low remaining oxygen levels
- chamber can be filled with programmable inert and sample-gas mixtures within a short time
- integrated 3-channel MFC with monitored set / is flow deviation for issuing an emergency purge if sample /auxilliary gas runs out
- system locks / unlocks lift / lower supply etc. independently from the main system
- system works independently from PC – in case of PC communication issues the safety system can react autonomously
- high precision safety valve maintains overpressure in the chamber – in case of a pressure drop an emergency purge is issued
- all parameters monitored for plausibility during operation
- gas outlet blockage detection
Well informed