Table of Contents
Specific heat capacity (Cp)
Specific heat capacity (Cp), often referred to as specific heat, is a fundamental thermophysical property of a substance. It indicates the substance’s ability to store thermal energy and equals the amount of heat that must be added to one gram of the substance in order to raise its temperature by one Kelvin. This process should not result in a 1st order phase transition (e.g. melting), since, in this case, the Cp can be infinitely large and therefore cannot be measured.
The SI unit of the specific heat capacity is kilojoules per kilogram times Kelvin [J/g*K)].
In general, specific heat capacity can be differentiated as isobaric (Cp at constant pressure) and isochoric (CV, at constant volume) based on the heat input. While at constant volume the amount of heat is completely used to increase the temperature; at constant pressure, only part of the heat is required for the volume change. This must be taken into account when measuring gases and vapors.
With a large Cp value, a certain amount of heat only leads to a slight increase in temperature; if the value is small, the same amount of heat can cause a greater temperature increase. The specific heat capacity for solids and liquids is between 0.1 and 5 J/g*K.
substance | aluminum | glass | chocolate | cement | water (20 °C) | PET (crystalline, 20°C) |
---|---|---|---|---|---|---|
Cp in [J/g*K] | 0,896 | 0,6 bis 0,8 | 3,140 | 0,754 | 4,187 | 1,510 |
Tabelle 1: Cp values of some materials (Chemie.de)
As an important material property, Cp will be listed in specifications and data sheets; it is used to calculate thermodynamic quantities such as enthalpy and entropy. It also helps to assess materials and their applications in various industries.
Determining the specific heat capacity using DSC
As a thermodynamic variable, one way to measure Cp is to use differential scanning calorimetry (DSC). For this purpose, the sample and reference run through a dynamic temperature program in the DSC oven. The temperature difference that develops between the sample and reference is attributed to a heat flow after appropriate calibration.
Different measurement methods are available. With the direct method, Cp can be calculated directly from the heat flow divided by the heating rate and sample mass. The process is quick, but not very accurate. This is why the more precise sapphire method has become the standard in line with the DIN 51007 and ASTM E 1269 standards.
Sapphire method
This is a comparative method. Three measurements are carried out under identical conditions.
- The first is done with two empty crucibles to determine the blank curve.
- In the second step, a flat sapphire disk (α-aluminum oxide) with a known mass and specific heat capacity is measured as a reference; the second crucible remains empty.
- For the third measurement, the sapphire disk is exchanged for the sample with an unknown Cp and the program is run again
- The specific heat capacity curve of the sample can then be determined as a function of the temperature using the three measurement curves according to the following equation:
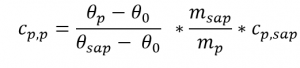
Where:
- Cp,p: specific heat capacity of the sample
- Cp,sap: specific heat capacity of the sapphire reference
- θp: heat flow of the sample
- θ0: heat flow of the blank curve
- θsap: heat flow of the sapphire reference
- msap: mass of the sapphire reference
- mp: mass of the sample
Considerations of errors during Cp measurement
When calculating Cp, make sure that the same crucibles are used for all three measurements. If this is not possible, the masses and Cp of the crucible must be known. These uncertainties must be taken into account when considering errors.
It should also be noted that the sensitivity of the measurement decreases with increasing temperature. The measured heat flow (DSC signal) of the sample is also subject to errors. This is caused by the thermal resistance between the sensor and the sample and is always smaller than the true heat flow. This error is increased by a pronounced temperature profile in the material during heating.
Excessive heating rates, large masses, and heat capacities as well as poor thermal contact between the sample, crucible, and sensor can all have a particularly negative effect. In addition, it should be ensured that the thermal conductivity and the specific heat capacity of the reference are in the area of the sample so that the same heat flows can result.
Temperature-modulated DSC
If reversing and non-reversing effects occur at the same time during a conventional DSC measurement, an overlap will occur in the DSC signal, preventing a clear evaluation of the results. The remedy is a temperature-modulated DSC, which can separate the superimposed effects from one another.
The heating rate is superimposed by sinusoidal temperature modulation. The result is two-part temperature control: a linear or constant part that interferes with a non-linear part with relatively rapid temperature changes. The procedure corresponds to the ASTM E2716 09 standard.
The advantage of this temperature-modulated measurement is that accuracies of up to 1 % can be achieved, even at high temperatures. A time-consuming test run is necessary to determine the specific heat capacity. It is worthwhile if Cp has to be measured during kinetic processes such as chemical reactions, crystallization, or evaporation. In addition, special evaluation software is required.
Influence of the crucible material
For DSC measurements, make sure that the crucible and sample are compatible. The crucible lid also influences the measurements.