Table of Contents
Metals are used in various industrial sectors for a wide range of purposes almost everywhere. Apart from construction and vehicle manufacturing, metals are also used as conductors and semiconductors, coatings, electronic components, or housing parts in electrical engineering. Especially here, in the automotive, medical, as well as aerospace sectors, the applications are often very specific and require small, precisely fitting structures. In order to realize these, increasingly modern manufacturing methods have been developed in the past, each offering higher precision at lower costs and also lower material consumption. Particularly, the so-called 3D printing processes represent a significant step forward in this regard.
3D printing process with metals
Direct Laser Metal Sintering
Among the methods of 3D printing with metals, Direct Laser Metal Sintering (DMLS), also known as Laser Power Bed Fusion (LPBF), is particularly prominent, based on powder bed fusion technology. In this process, metal powder is provided and selectively melted by an energy source, usually a laser, to create a 3D structure.
In CLAD (laser cladding or cladding, also DED – direct energy deposition – process), a similar method, metal powder is deposited from a nozzle, similar to the ink of a regular printer. However, at the nozzle outlet, the powder is directly melted by a laser, allowing for the printing of liquid metal directly.
A combination of additive manufacturing and additive machining is the so-called cold cutting method or cold gas spraying. Here, fine metal particles are pressed through a fine nozzle with a carrier gas (usually helium) at high pressure, causing them to plastically deform upon impact on a substrate and form a layer that can be directly processed without actual melting. However, this method is rarely used due to its high cost.
Metal Binder Jetting
There is also metal binder jetting. Similar to the plastic powder bed process, the metal is mixed with a binder and bonded to form a homogeneous mass. The resulting green part is then freed from the binder using thermal processes, i.e. by burning or laser heating, and given its final shape.
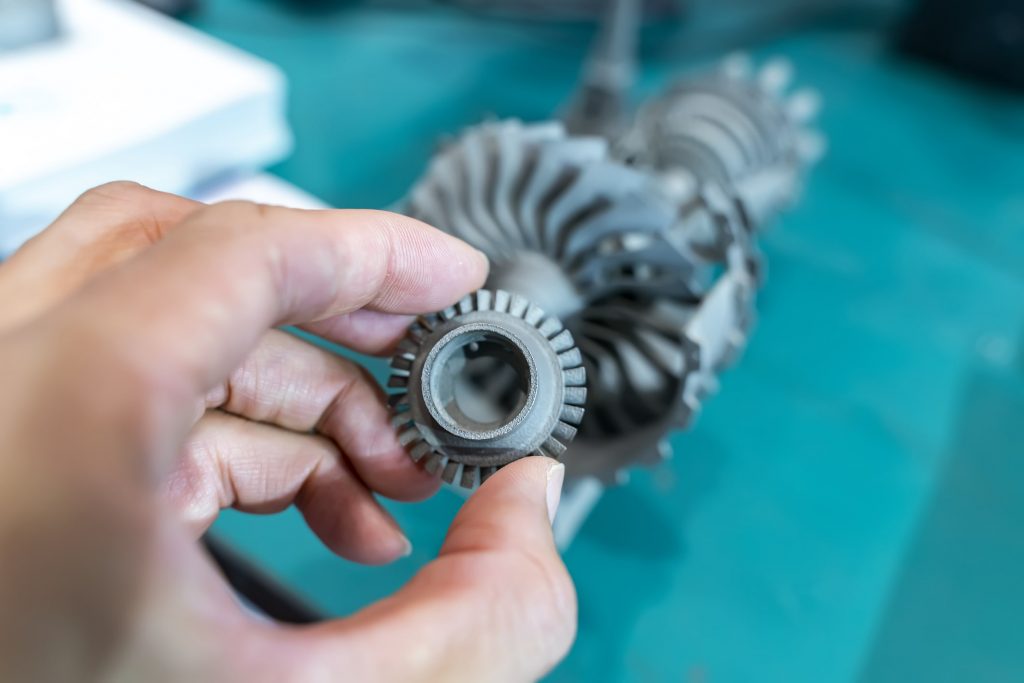
Fused deposition modeling
Similar to the plastic process, there is also fused deposition modeling (FDM), in which a metallic filament (usually made of low-melting-point metals or alloys) is simply heated until it softens and then applied in layers via a nozzle.
All of the mentioned methods share the commonality that they do not work with every metal. The common metals for metallic 3D printing are aluminum and its alloys, steels and iron alloys, as well as materials such as gallium, indium, titanium, cobalt, or chromium. Despite relatively high costs, precious metals like gold and silver are now also being used. However, shaping these metals can be somewhat more challenging. Heavy metals and very hard or high-melting metals are used little to not at all.
Applications of metallic 3D printing
The most common applications of metallic 3D printing are primarily prototyping and research and development, especially when only individual parts and not series are to be manufactured. Here, the tooling for a cast workpiece is often very expensive and can be cleverly avoided by 3D printing.
The energy costs saved compared to a cast workpiece are also significant. Likewise, the material savings on the often expensive metallic raw material. In addition, especially for individually manufactured implants in medical technology or specially adapted machine spare parts, the advantages of 3D printing with metals are undeniable.
In contrast to ceramic or polymer 3D printing, not all shapes or structures are readily achievable with metal sintering or cold gas printing, as different metals have significantly different melting zones and application of mixtures or specific layers may not always be feasible. Nevertheless, research is currently ongoing on these methods to unlock even more flexible and diverse applications in the future.
Advantages of 3D printing with metals:
- No tooling required
- Savings on energy costs
- Savings on metallic raw material
- Individual manufacturing of parts possible
Thermal analysis of 3D printed metals
Thermal analysis can characterize the generated metals regarding their properties and help to identify differences and deviations between conventionally manufactured and 3D-printed components with its methods.
- With DSC, melting points and phase transitions can be determined, optimizing the alloys for use in 3D printing. (Application of alloyed steel)
- Through dilatometry, expansion behavior as well as hardness and phase transitions can be demonstrated. (Application with iron)
- The thermal conductivity and heat transfer properties of both cured products and powders and alloys can be well characterized using THB and laser flash methods. (Application with copper and aluminum)
- And also, thermo-electric properties such as electrical resistance, conductivity, and Seebeck coefficient can be precisely determined with the methods of modern thermal analysis. (Application with copper)