Table of Contents
Thermische Analyse von 3D-Druck-Keramiken
Keramiken werden in vielen Bereichen der Industrie verwendet. In der Regel werden Keramiken zunächst als Grünkörper aus Rohmasse geformt, bevor dieser „Grünling“ dann auf eine spezielle Art behandelt und gebrannt wird (sog. Sintern), um ihn auszuhärten und in seine endgültige Form zu bringen.
Je nach Branche kann es sich dabei um simples Geschirr, Dekoration oder Sanitärartikel handeln, aber durchaus auch um technische Keramiken wie Prothesen, oder verschiedenste technische Bauteile. Ein Keramikwerkstück wird normalerweise nach erster mechanischer Bearbeitung in einem Ofen gebrannt. Es wird dabei Temperaturen zwischen 900 °C bis 1400 °C ausgesetzt.
Dies geschieht durch Erhitzung in einem definierten Zeitinterwall bei stetig steigender Temperatur, aber auch in genau festgelegten Isothermen Intervallen, um chemische Reaktionen beim Brennen der Keramik zu steuern und das Entgasen von Wasserdampf, Kohlenstoffdioxid und anderen Beimengungen zu kontrollieren. Nach dem ersten Brand kommt oftmals noch eine Glasur auf die Keramik und anschließend wird das Werkstück erneut gebrannt, um es vollständig auszuhärten.
Der gesamte Prozess dauert einige Stunden und ist daher mit einem nicht unerheblichen Zeitaufwand verbunden. Dabei kann zudem nicht garantiert werden, dass das Werkstück nach dem Brennen unbeschädigt aus dem Ofen kommt, es können verschiedene Fehler (Materialmangel, falscher Brennprozess etc.) auftreten, die zu einem Bruch oder Rissen in der Keramik führen kann.
Eine modernere und einfachere Lösung, um verschiedenste keramische Bauteile zu brennen ist die additive Fertigung. Bei Keramiken spricht man hierbei auch oft vom sog. 3D-Druck. Dieser ist ein Fertigungsverfahren, bei denen Material schichtweise aufgetragen wird, um dann daraus dreidimensionale Objekte zu erzeugen.
Der Aufbau erfolgt in der Regel computergesteuert (CAD) und als Ausgangsstoff dienen ein oder mehrere flüssige oder feste Materialien nach vorgegebenen Abmessungen und Formen. Während des Aufbaus mittels Druckprozess finden chemische Aushärtungs- oder Schmelzprozesse statt, oftmals mittels Temperatur oder Laser gesteuert. Es ist sogar auch möglich, einen 3D-Scanner für ein Modell zu verwenden.
Der Vorteil der Methode gegenüber herkömmlichen Brennprozessen liegt dabei klar auf der Hand: Durch das schichtweise Aufbringen der Keramik lassen sich filigrane und komplexe Strukturen fertigen, bei denen das Bruchrisiko während des Brennprozesses besonders hoch wäre. Zudem gelingt eine enorme Zeitersparnis, da ein additiv gesintertes oder 3D-gedrucktes Werkstück wesentlich schneller herzustellen ist aufgrund des nicht notwendigen Brennprozesses im Ofen.
Im Vergleich zu allen materialabtragenden Verfahren wie Schneiden, Drehen und Bohren hat der 3D-Druck den Vorteil, dass der zusätzliche Bearbeitungsschritt nach der Urform entfällt. In den meisten Fällen ist das Verfahren auch energieeffizienter, vor allem wenn das Material nur einmal in der benötigten Größe und Masse aufgebaut werden muss. Außerdem ist es von Vorteil, dass verschiedene Materialien in einer einzigen Maschine verarbeitet werden können.
Ursprünglich wurde das Verfahren 3D-Druck zuerst in der Polymerindustrie angewandt und entwickelt, da Kunststoffe leicht in Schmelze zu bringen und zu handhaben sind und kein Sintern oder Aushärten notwendig ist. Durch Erwärmen knapp über den Erweichungspunkt und das schnelle Abkühlen des gedruckten Filaments konnten so Strukturen in Echtzeit erschaffen werden. Das Verfahren hat sich jedoch schnell weiterentwickelt, sodass nicht nur verschiedene Polymere, sondern mittlerweile auch Metalle und Keramiken gedruckt werden können, was den 3D-Druck zu einer vielseitigen Option für die Fertigung macht.
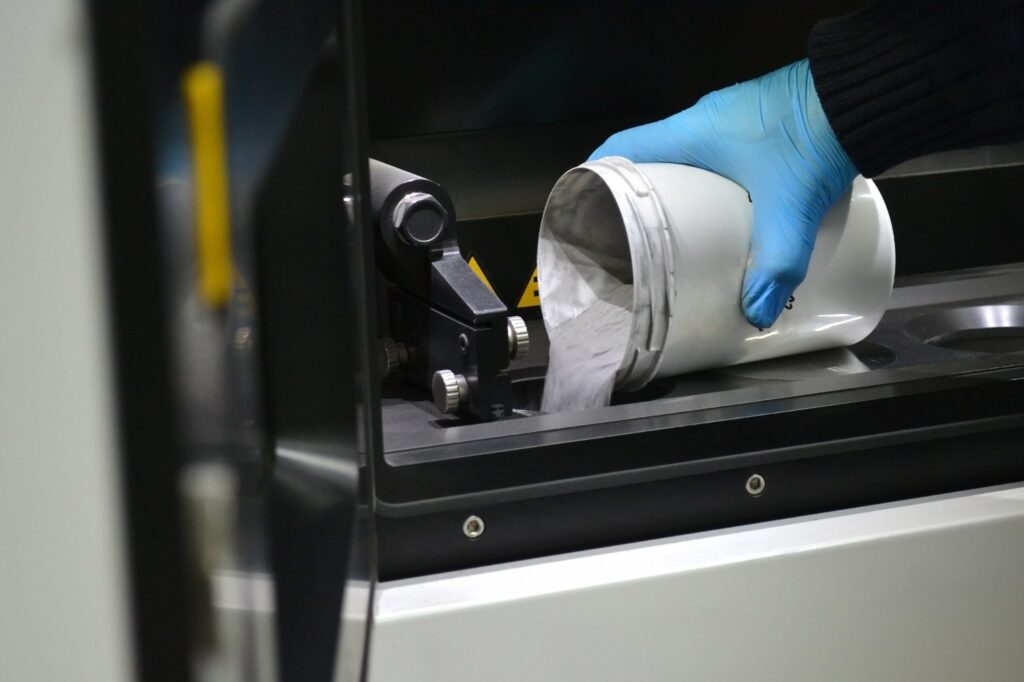
Die Herstellungsverfahren der additiven Fertigung können in sieben Hauptkategorien eingeteilt werden und sind inzwischen auch in einigen Normen genau beschrieben(DIN EN ISO/ASTM 52900, früher ASTM F2792):
- Bindemittelausstoß
- Materialausstoß
- Pulverbettfusion
- Materialextrusion
- Bottich-Photopolymerisation
- Gezielte Energiedeposition
- Laminierung von Bögen
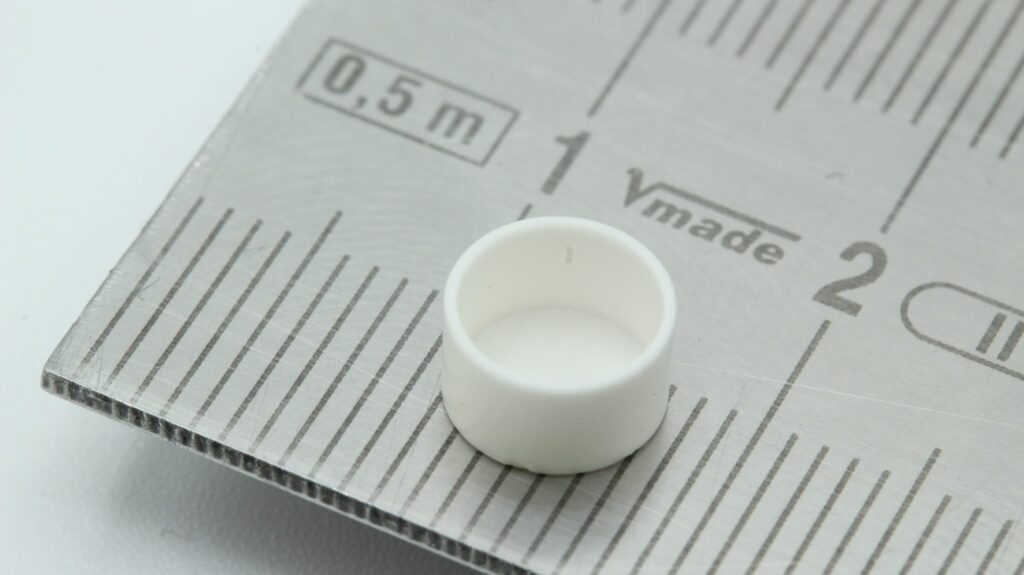
Der Hauptunterschied zwischen ihnen besteht in der Art und Weise, wie die Schichten zur Herstellung der Teile aufgetragen werden und welche Materialien verwendet werden. Die wichtigsten Faktoren bei der Wahl der Maschine und des 3D-Druck-Verfahrens sind Geschwindigkeit (abhängig von der Größe des Objekts) und Kosten (für Material und Maschine). Materialien im Allgemeinen: Metall, Keramik, Kunststoff.
Hauptanwendungsgebiet der additiven Fertigungstechnik ist nach wie vor die Forschung und vor allem die Produktentwicklung bzw. der Prototypenbau in der Industrie. Sie eignet sich hervorragend zur Herstellung von Modellen, Prototypen, Werkzeugen oder bestimmten Produkten, da keine speziellen Werkzeuge erforderlich sind und die Umsetzung von Zeichnung zu Modell sehr schnell realisiert werden kann.
Weitere Anwendungsbereiche sind vor allem die Medizintechnik, wo speziell angepasste Prothesen und Implantate (vor allem auch in der Zahnmedizin) angefertigt werden müssen, die oft individuell auf Maß angepasst sind. Aber auch eher ungewöhnliche Anwendungsfelder wie z.B. Bildhauerei und Kunst setzen additive Fertigung für die Herstellung von Skulpturen ein. Mittlerweile können 3D-Drucker auch im privaten Gebrauch eingesetzt werden, da die Verfahren und Drucker inzwischen die Serienreife erlangt haben und relativ kostengünstig der Öffentlichkeit zugänglich sind. Im Haushalt lassen sich vor allem Kunststoff-Erzeugnisse wie Spielzeuge, Ersatzteile oder kleine Halterungen leicht und ohne große Vorkenntnisse herstellen.
Für Keramiken werden dabei folgenden Methoden zum 3D-Druck verwendet:
- Pulverbettfusionsverfahren, wie das selektive Lasersintern (SLS).
- Dieses Verfahren kann generell zum Drucken von Polymeren, Keramikpulvern oder Metallen verwendet werden. Dabei schmilzt man das Materialpulver mit einem Hochenergielaser, um schichtweise völlig dichte Materialien zu erzeugen. Eine dünne Schicht des Pulvers wird mittels Düse auf ein Tablett gegeben. Ein Laser beginnt dann, das Pulver lokal zu sintern und dadurch die erste Schicht zu erzeugen. Eine Abwandlung davon ist der 3D-Tintenstrahldruck. Hier wird ein Bindemittel mit einem tintenstrahlähnlichen Verfahren auf eine Pulverschicht (Gips oder Harz) im Querschnitt des Teils gedruckt. Ein Vorteil der Pulverbettfusionstechniken ist, dass das überschüssige Pulver als Träger für das gedruckte Objekt dient.
- Beim Fused Deposition Modeling (FDM) oder Fused Filament Fabrication (FFF) werden kleine Patrikel der gewünschten Keramik verarbeitet.
- Damit das funktioniert, wird im Filament ein bestimmter Binder eingesetzt, meist ein spezieller Kunststoff, der das Keramikpulver zusammenhält.
- Anschließend wird das Filament so stark erhitz das es sich verflüssigt und gedruckt werden kann, wie bei einem herkömmlichen Kunststofffilament. Die Keramikkörner haben hier einen Durchmesser von ungefähr 1-2 µm.
- Dadurch, kommen sie beim Drucken mit dem Kunststoff direkt aus der Düse und man kann die gewünschten Schichten direkt drucken.
- Nur der Kunststoff, der das Pulver zusammenhält und transportiert, schmilzt bei diesem Prozess und dient somit als Bindemittel.
- Es entsteht letztendlich eine gedruckte Form, die jedoch im Wesentlichen noch aus dem Keramikpulver besteht und nicht aus einem festen Keramikkörper.
- Dies ist noch nicht das Endprodukt, sondern es ist ein Grünling der erst noch nachgearbeitet werden muss.
- Durch einen speziellen Prozess wird schließlich ein Teil des Kunststoffes entfernt. Anschließend folgt der Sinterprozess, bei welchem das Werkstück in einem speziellen Ofen unter hohen Temperaturen und chemischen Stoffen ausgesetzt wird.
- Die Keramikteile verbinden sich dabei und der Kunststoff wird vollständig entfernt. Damit ist das FDM letztendlich dem ursprünglichen Keramik-Brennprozess sehr ähnlich, da man nur einen Brennschritt einspart, den zweiten aber noch durchführen muss.
Die richtigen Bedingungen für das Material, das in einem 3D-Drucker verwendet werden soll, hängen vom Temperaturverhalten wie z.B. der Schmelztemperatur ab und davon, wie sich das Material unter Temperatur ausdehnt oder welche Wärmeleitfähigkeit vorliegt. Es ist somit sinnvoll, die thermischen Eigenschaften der eingesetzten Materialien für den 3D-Druck ausgiebig zu testen. Für diese Untersuchungen sind die folgenden Geräte relevant:
- Mit der klassischen Dilatometrie (DIL) können die thermische Längenausdehnung und das Sinterverhalten von Festkörpern und pulvern ausgiebig untersucht werden. Damit gehört die Dilatometrie in der kermischen Fertigung mittlerweile zum Standardverfahren.
- Daneben sind diverse Methoden zur Untersuchung der Wärmeleitfähigkeit sinnvoll, um die Temperaturverteilung und -Weiterleitung im Werkstück simulieren und steuern zu können. Die gängigsten Verfahren sind hierbei Flash-Techniken wie das Laser-Flash-Verfahren (LFA) bei dem in der Regel Temperatur- und Wärmeleitfähigkeit von Festkörpern oder Pulvern mittels Hochenergie-Lichtblitz ausgemessen werden können. Daneben gibt es Heizdrahtverfahren wie das Transient-Hot-Bridge (THB), welches bei Raumtemperatur relativ schnell verlässliche Werte hinsichtlich des Wärmetransports liefern kann. Für Pasten und Pulver eignet sich zudem der Trans-Interface-Material-Tester (TIM), eine Abwandlung des Guarded-Hot-Plate-Verfahrens, der vor allem verschiedene Schüttdichten und die sich damit ändernden thermischen Transporteigenschaften messen kann.
Wenn ein Bauteil erst einmal gefertigt ist, ist es wichtig, die Anforderungen an das Bauteil in Bezug auf die thermischen und mechanischen Eigenschaften zu ermitteln und sie mit einem speziell auf den Prozess zugeschnittenen Design zu entwickeln. Dies gilt normalerweise unabhängig vom Fertigungsverfahren, mit dem das Bauteil gefertigt wurde. Bei additiv gefertigten Bauteilen ist es jedoch besonders notwendig, die mechanischen Eigenschaften zu überprüfen, da diese unter Umständen durch den Schichtaufbau anders ausfallen als bei einem gegossenen oder gebrannten Objekt. Besonders bei Keramiken verkleinert sich das Werkstück nach dem Sintern oder additivem Aufbringen massiv und es können diverse Fehlerquellen vorhanden sein, die zum Materialversagen führen. Auch hier kommt in der Regel ein Dilatometer zum Einsatz, unter Umständen sogar die thermo-mechanische Analyse (TMA), die in der Lage ist, die mechanischen Materialeigenschaften durch Biege-, Zug- und Druckversuche genau zu erfassen.